Blog 98 -- A Flawless External Audit - An Electrical Fire Affects (Initially) 90 Reefer Containers
- ranganathanblog
- Dec 11, 2022
- 7 min read

External Audit and First ISM Certificate:
We had just completely failed in the ISM Internal Audit.
As we sailed out of that port, I went up to the Bridge to talk to the new Captain to get his cooperation and to unitedly prepare for the External Audit.
To my surprise, he beat me to the punch. The first words he told me was “Bada Saab, I will be extending my - and my staff’s - fullest cooperation in getting the vessel ready for the External Audit. Since I know nothing about it, I will follow your lead and please hold lectures if necessary, at your convenience. We will do all the paperwork and the documentation needed”.
So started an intensive three weeks training for all personnel. No time was lost.
No one was allowed to escape training sessions.
The Captain and the Chief Mate, on their parts, prepared their documentation, including all the ship specific check lists, with the four of us brain storming almost every few hours to prepare such documentation.
I even went to the extent of preparing a questionnaire, with answers, of what I thought a Class Surveyor, acting as an External Auditor, would ask the Captain, the Chief Mate and me. It proved to be of tremendous help to all.
The External Audit took place in Singapore, where we had a two day stay for cargo purposes.
The External Auditor was from NKK - Japanese Classification Society.
The same NYK Internal Auditor was in attendance, apprehensive at first and in disbelief later.
The External Auditor concentrated more on our knowledge of the ISM Code and the Company’s SMS Manuals. He questioned each of us individually, asking specific questions and naming the person who would need to answer.
All documentation was spot on, well filed, labelled.
He spent a lot of time on Ship Specific documentation, wanting to know our thought processes during the preparation of these documents.
He called for the Chief Cook and the Third Engineer to answer a few questions on SMS and their own duties.
And then came the physical inspection of the ship.
Bridge Equipment and their function tests received top priority. The documenting of such tests were asked for and shown.
He asked for a couple of the equipment to be tested in his presence.
His inspection on deck was peremptory due to cargo work going on, but he was impressed with the level of maintenance.
He liked the fact that
Ventilation dampers had been repaired and motors overhauled, as depicted on stencilled labels.
Bunker lines had been pressure tested, with details labelled.
All air pipes’ head units and floats had been overhauled, dates labelled.
He was particularly impressed by the Engine Room.
Spic and span, painted.
Machinery that had been overhauled had stencilled labels on them.
Tanks, including Fuel Oil Service and Settling Tanks, had labels on when last cleaned.
Maintenance Records were up to date.
His Audit was supposed to extend into the next day.
He completed his Audit and left the ship on the first day itself, the new Certificate to be delivered the next morning.
The NYK Auditor took us out to dinner, happy with the way the External Audit went. He said that we were the first ship in the NYK fleet to go through our maiden External Audit and not have any ‘Non Conformities’. He was amazed at the complete transformation in just less than a month.
He took away my copy of my prepared questionnaire / answers for his own use.
A month later, I received an official certificate appointing me as an NYK Auditor for NYK ships.
Over the next two years he corresponded with me regularly, asking me to evaluate changes to the SMS or documentation or the introduction of something new even when I was on non NYK ships.
Preparing the ship for an Internal as well as External Audit was a learning experience for me, for it stood me in good stead in the years that followed, especially with the escalating importance of the ISM Code, which finally embedded itself deep into the life of a seafarer.
An Electrical Fire affecting 20 Reefer Containers
We had come around Australia and were now on our last leg from Melbourne to Fremantle.
We always carried at least a 100 Reefer Containers, every voyage, from Australia to other Asian countries. Some meat or meat products and mostly dairy products. As the months went by, we found ourselves carrying nearly 215 Reefer Containers, our full capacity being 220 reefers.
The NYK Providence was a Container ship, probably 5000 TEUs capacity.
As was the design and construction of most Container vessels in the 1970s and 1980s, there were two outboard underdeck passages, port and starboard, running the full length of the ship, with several watertight doors.
The rather large Under Deck Passages served as a conduit for various pipelines and electrical cable conduits and also the container holds. The high capacity cables ran from the Main Switchboard in the Engine Room to all the heavy deck machinery forward and aft, as well as all lighting circuits.
Cables for Reefer Container sockets that were adjacent to the container cells and also on the Main Deck ran through these under deck passages. There were several multi core cables for this purpose.
Incidentally, the ship had undergone a conversion a few years back and had been jumboised to include two more container sections, with Reefer Containers’ capacity being increased from 100 to 220, a rather big jump.
During this jumboisation, nobody gave a thought to the increased load on the generators. We found ourselves running all three generators when the number of Reefer Containers being carried exceeded 120. (Maximum two are supposed to run at sea, while the third underwent maintenance or is kept on ‘standby’).
All electrical cables were in an enclosed rectangular steel cable tray, about 1.5 metres by 1 metre, the top cover plate in sections of 2 metres, screwed down. In the passageway, we had to walk on this, opening and closing watertight doors.
Because of work going on, several watertight doors would be open during the working day and shut off after the day’s work was over.
These under deck passages can be accessed from the Engine Room and from Main Deck forward and aft.
It was a daily practice to open two mushroom natural ventilators right forward to ventilate this passage during working hours.
A day out of Melbourne, thick, heavy smoke started coming into the Engine Room from the starboard under deck passageway, immediately identified as an electrical fire from the smell.
Using the isolation switches on the Main Switchboard in the Engine Room, we cut off power to the starboard side cables.
The Engine Room doors, the forward and aft doors were shut off. The mushroom ventilator was screwed down and shut off.
Three of us in fire suits and SCBA sets, carrying dry powder extinguishers, w/t sets and screw drivers made entry from the aft end - down wind - and found two of the top cover plates nearly red hot, much forward of midships.
We unscrewed two adjacent top covers and emptied all the three extinguishers. In a while, the red hot top covers stopped glowing. Since all avenues of oxygen flow had been isolated, we opened the two hot covers and pushed them aside to find that three multi core cables were burnt at the joint where the old cables were enjoined to the new cables (Done during jumboisation). Instead of expending dry powder extinguishers, we brought in dry powder spare packets and laid a blanket of dry powder on a good stretch of the cable tray.
The smoke and fire died down.
Next came the investigation of what all we had lost power to.
The starboard forward winch and windlass had no power, along with certain sections of lighting.
The most worrisome part was the loss of power to about 90 sockets for the reefer containers.
The Electrical Officer and I decided to jump cables from the port side power sockets to as many points on as possible on the starboard side.
With all of us pitching, we restored power to 70 of the 90 reefer containers.
Time taken from switching off power to restoring power - about 7 hours.
We did not leave or condemn the 20 reefer containers to their own fate.
Instead, we kept supplying power to all the containers by starving one container for a while and changing the lead cables again and again, based on the temperature.
We kept this up for 2 ½ days on a continuous 24x7 basis and managed to save all the reefer containers, by which time we reached Fremantle.
To provide continuous power supply to the 20 containers, we ordered two ‘generator containers’ to be brought aboard on arrival. (Not sure what it is called, exactly). It comes with a fuel tank and a generator that, when started, gives power supply to 15 reefer sockets. Power cables were also supplied.
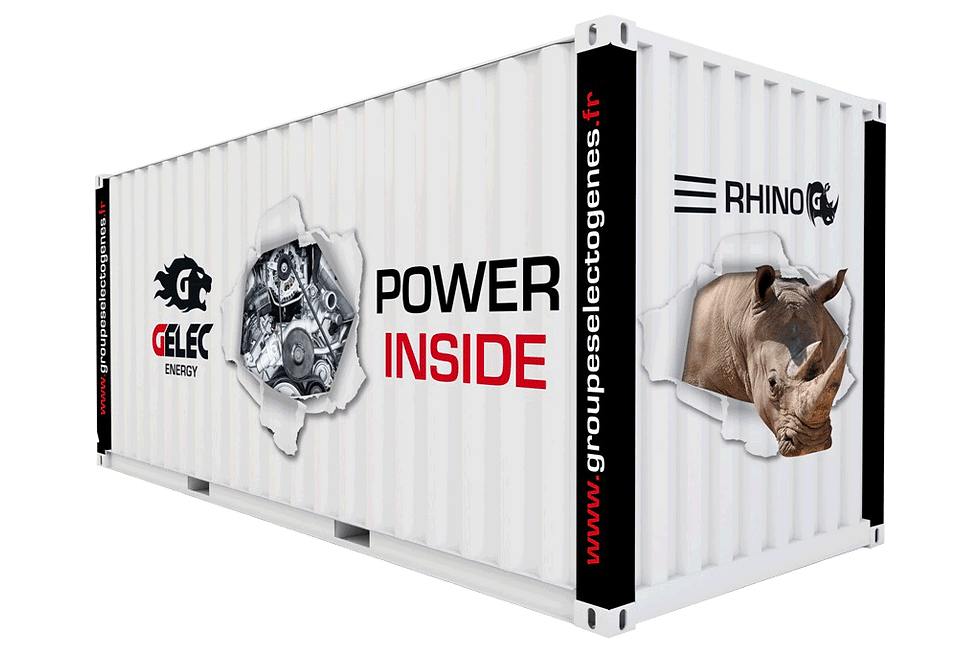
For Representation only
Within two hours of our arrival Fremantle, all reefers had power. Due to our changing cables from one to the other we had managed to maintain all temperatures of all containers.
During the past three days, we had kept NYK Hong Kong apprised of the situation at every stage.
Reefer cargo, whether in reefer holds or in reefer containers, is precious cargo. In that period of time, the freight rates for one chamber, of a 6 chamber reefer hold, was sufficient to pay the operating costs of one round trip of the ship.
When in the form of reefer containers, the successful carriage of around 25 odd reefer containers pays the operating costs of one round trip. I am not sure how it is these days, but carrying refrigerated cargo, whether in reefer chambers or in reefer containers has always been considered precious cargo.
After the fire was put out, with loss of power to so many containers, the possibility of declaring ‘General Average’ was discussed. But by jury rigging connections, we were able to keep all containers active. Hence, the idea of ‘General Average’ was dropped.
It was a very busy three days.
As we expected a horde of Cargo Surveyors to board at Fremantle, each representing a different shipper or consignee, we made about 30 copies of our detailed report and kept them ready.
In the modern world of today, Reefer containers are monitored minute to minute by shore establishments through a GPS connection on each Reefer container. Gone are the days of disc paper and a stylus pen to graph out recorded temperatures.
We reached Fremantle. The two generators that we had ordered came on arrival. Now all containers were plugged in.
21 Cargo Surveyors boarded the vessel all at once and kept Captain and me busy, asking questions, reading our reports. The Chief Mate and the other Officers were kept busy escorting the Surveyors to the particular Reefer containers that he was representing to see for himself the displays.
We nearly ran out of paper for the photo copier in the process of catering to the documentation needs of the Cargo Surveyors.
And into this semi chaotic scene, stepped an unknown character. Not known to any of us nor to any of the Cargo Surveyors.
====== Blog 99 Continues ======
Commentaires