Blog 95 - "Marine Musings 29" - "Thornhill" - Frustrating Ship - Running to Stay in the Same Place
- ranganathanblog
- Nov 30, 2022
- 5 min read

This is the shortest blog - duration 4+ minutes - that I have published so far and, in terms of content, a continuation of an explanation of the fuel process from Fuel Oil Double Bottom Tanks right up to the Main Engine. This is more for the benefit of the non seafaring readers of my blog.
I have briefly written - in this blog - on Ship Management Practices and the ISM Code, as perceived by me. As the seafarer is the one who joins a ship and takes care of her during his tenure and because he is the ultimate service provider, all the decisions taken by the Management - whether good or bad - falls heavily on his shoulders. His being overburdened with the responsibility of following and implementing Local, National and International laws at all times can be quite strenuous. In today's world, the prospect of arrest and prison time in a foreign land is akin to a Damocles Sword during every moment he is on board.
To continue from my last Blog:
Next comes the purification.
Using centrifuges, the size of which is determined by, and equated to, the consumption of that particular ship, the fuel oil is purified, taking suction from the Settling Tank. Most of the water gets dispelled. Most of the sludge is removed during this purification. Specific Gravity of the fuel oil and the temperature maintained while purifying, are the extremely important parameters for proper purification.
Drawing of purifier

Courtesy mainersgalaxy

Courtesy Alfa Laval

Courtesy Alfa Laval
The most common of centrifuges are manufactured by Alfa Laval. There are also quite a few ships with Mitsubishi purifiers. The principle of operation is the same, the construction also nearly similar. Dismantling and assembling procedures are different.
This purified oil next goes into the Service Tanks.
Through a series of pumps, heaters and filters this oil from the Service Tank reaches the Main Engine.
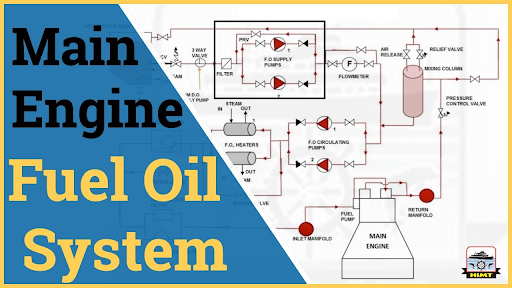

Courtesy Marinesite.info
From Service Tank to Main Engine
Probably the most difficult 2 ingredients present in the fuel oil that cannot be easily purified are vanadium compounds and wax.
To a certain extent, microfilters in the fuel oil line reduce the wax and the compounds of vanadium.
Starting from the mid 1980s, a 1 litre sample of the fuel oil bunkered was being sent for analysis to a recognised laboratory mandatorily. As the years went by, the sophistication of this fuel analysis grew in inverse proportion to the quality of the fuel oil bunkered, as the quality of the fuel oil went downhill fast, till we - looking at the fuel - did not know if we were receiving fuel oil or heated tar.
Fuel Oil Analysis is really a vast subject and cannot be treated casually. It requires a lot more than what I can give in these few lines.
Perhaps I can devote an entire “Marine Musings” blog on this subject at a later date.
The ship was run down and neglect showed in practically every sphere.
During the 5 months I was on board I tried my best to improve the standards all round, but was handicapped by lack of spares and stores. I hope my successor received these, as I had requisitioned them. A detailed report on my plans to upgrade the ship went out to the Office, with copy to the incoming Chief Engineer.
Ship Management
With the proliferation of Management Companies in the 1980s and the consequence of increased competition, Management companies such as Barber’s were forced to rethink their policies on acceptance of ships for Management.
In the early and mid 1980s, a few ships were rejected by Barber’s and were not taken in for Management, on the basis that they were not of good standard and likely to be troublesome.
All that changed dramatically in the late 1980s and a U-turn was made in terms of acceptance of vessels for management, based on the condition of the vessel. Now practically all comers were welcome - only the Management fee mattered, some based on just a ½ hour inspection.
Substandard ships were now being taken into the Management. This policy would have been acceptable if there was a commitment on the part of the Owners and the Management to fix a time frame for improving the condition of the ship by at least 40% in the course of a year.
This, obviously, costs money, hence rejected.
We, the staff on board, were now running around trying to prevent breakdowns, trying not to put the ship in jeopardy with untimely breakdowns, all the while doing so without the important Spares or stores supply.
It is, then, no surprise to see the on board staff not being interested in maintaining the ship, as they run into stone walls every time they show interest.
Indifferent staff, indifferent office, indifferent ship. The 1990s saw a losing battle between the ship and the management. To make a bad situation worse, we had to start contending with Office mid level staff with very little experience, who were unable to picture on board scenarios by simply reading reports. So the magnitude of a problem actually goes unnoticed till it mushrooms into a threat.
Standards were declining all around and Marine accidents were on a sharp rise.
Monthly Maintenance Reports from the ship, which had always been a fount of informative history, became merely one liners. If we had trouble with one set of machinery, we would always go back in time into the earlier Maintenance Reports for signs of any recurring problems and, possibly, solutions.
Starting from the 1990s, Maintenance Reports became sparse in content and gave no clue about the history of a particular machinery.
The "I S M Code"
The second half of the 1990s saw the phased implementation of the International Safety Management Code, about which I intend to elaborate soon in my “Musings”.
As a prelude - in today’s terminology ‘a teaser’ - I had always thought that the implementation of the ISO 9000 standards through the formulation of the International Safety Management Code, was for the purpose of increased accountability on the part of a Management in case of accidents, along with better quality control and a stated policy in what the Management expect of themselves, the ship and the seafarers sailing on them, so that all parties are clear in their objectives and are in sync in working towards the same goals. The burden of ‘accountability’ was supposed to fall directly on the shoulders of the Management, the Office and the personnel in that Office.
But what actually happened was entirely different from what was envisaged. The ‘responsibility’ for each decision was shifted on to the Master, with the ship becoming accountable. This was done through the mechanism of a series of ‘Check Lists’, for every imaginable situation, thus separating the burden of ‘accountability’.
I ended my tenure of 5 months on this ship rather frustrated at my inability to drag the ship out of its stagnation of years. She was fast becoming a junk. It seemed, to me, that the only thing that could be done for this ship was to send her to the breakers.
My final reports were explicit in this detail.
===== Continued in "Marine Musings 30" =====
Comentários