Blog 91 - "Lakers" - Ethics of a Hand Over - In the Event of a CPP Failure Emergency Measures
- ranganathanblog
- Nov 16, 2022
- 11 min read
Marine Musings 27 - “Atlantic Erie” - Another Self Unloader Belonging to CSL - 7th Nov 1993 (Bremen) to 03rd Feb 1994 (Mo i Rana)

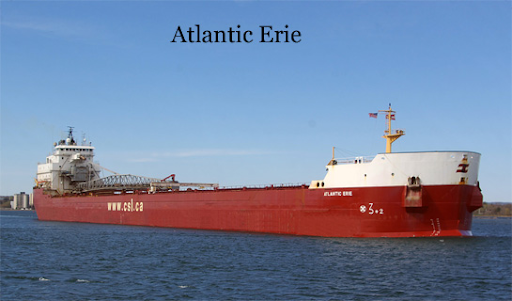
In spite of my being persona-non-grata on Vulica Self Unloaders, I was called to join a Canadian Steamship Lines Self Unloader, the ‘Atlantic Erie’.
This time around, while in Bombay, I made it very clear that I will not join any more Self Unloaders unless there is a dramatic change in the wage scale for Chief Engineers. I joined the ‘Atlantic Erie’ more as a debt (several) of gratitude and courtesy to Capt Mehra’s and Capt Karnik’s (who headed the Bombay Office) requests, as they were unable to find a suitable Self Unloader experienced Chief Engineer, with a proviso that I be relieved in 3 months.
The Atlantic Erie was a Laker, long in length and narrow of beam. She was now plying between Bremen in Germany and a couple of ports in Norway, carrying steel pellets from Norway to Germany - a short run of 4 days through the North Sea.
Mo-i-Rana and Bodo were the two load ports in Norway - the first just within touching distance of the Arctic Circle and the second just beyond the Arctic Circle.
With this crossing, I had crossed 4 of the 5 primary latitudes, the Arctic Circle, the Tropic of Cancer, the Equator and the Tropic of capricorn. Only the Arctic Circle remained.
(A seafarer on international voyages does not keep track of the crossing of the primary longitudes - the Greenwich Line and the International Date Line. For that matter, neither does he keep track of the crossing of the three primary latitudes).
I joined the ship at Bremen, Germany and, after a few hours, the other Chief Engineer got off. A very poor ‘handing over’ - it has become a recent malaise.
Ethics of a ‘Hand Over’
Ethically, the outgoing Chief Engineer is duty bound to be totally honest in his written ‘Handing Over Report’ and also take the incoming Chief Engineer verbally through the problems that he has faced and what kind of problems that he is handing over. If he does not have time enough to state them verbally, all this should, anyway, be mentioned and highlighted in his written report.
In order to make himself look good in the eyes of the Management, there is a tendency to hide major - either past, present or impending - problems, which the incoming Chief Engineer is suddenly confronted with at a later stage. The incumbent, then, is looked upon with villainous eyes by the Management, through no fault of his own.
Classic examples of these are
Exhaust Boiler or Auxiliary Boiler tubes leaking, result heavy losses of fresh water. No mention is made of this rather disturbing problem, either in the Maintenance Records or in the Handing Over Notes. I have categorised it as a ‘disturbing problem’ since it can, over a period of time, have catastrophic results. Lack of qualitative water treatment over a couple of years can lead to this problem.
Steam coils in Fuel Oil tanks leaking, result oil contamination of condensate water. With the same water being fed into the Auxiliary Boiler, this surface oil slowly coagulates and sinks down to the spaces between the furnace and the boiler shell plating, where it solidifies into a tar like gel due to the furnace heat, which is very difficult to remove and clean out. If not rectified, one day the Boiler is likely to explode.
Spares deficit - no order placed for required spares. Further, no order placed for spares and stores that have been consumed in his tenure, wanting to please the Vessel Superintendent who is trying to spend the minimum for his ship, in turn trying to get into the good books of his boss. In the event of a breakdown, the incoming Chief Engineer becomes accountable due to the perfidies of others.
Stores deficit - denuding the ship of stores and not ordering replacements.
Fuel Oil quantities discrepancy - This is a bugbear that I had to contend with quite a few times. In order to show more efficiency for the Main Engine, the callous Chief Engineer would show less consumption, fudging the flow meter readings on a daily basis. Over a period of 5 to 6 months, there would be a shortfall of around 100 to 120 tons. They would then need to cover up the deficit when handing over. They would, then, keep a tabulation of soundings and quantities ready, all fictitious, hoping that I would pass over my right to take all soundings and calculate present quantities for myself.
There were very few occasions when I would veto that right, not take any soundings and accept the one given to me as official.
One occasion would be time constraints - the ship would be sailing within a couple of hours of my joining.
Second would be when I was taking over from juniors who had been my protege’s.
Diesel Oil quantities were often found to be problematical. Since the mid 1980s, more and more diesel generators were being run on heavy fuel oil. But due to lack of understanding the system and lack of timely maintenance, they would find themselves running the generators on diesel oil, while logging the consumption as ‘fuel oil’, thereby creating a discrepancy in the quantities remaining on board, for which there would be no reasonable explanation.
I have been involved in three such ‘take overs’, where the quantities, as measured in the tanks, were found to be alright but tanks found to be contaminated with water. I stumbled upon this method of adding fresh water into a diesel oil tank to make up the deficit when I noticed that the generator was running on diesel oil, but being shown as ‘fuel oil consumed’ in the Engine Room Log Book.
On those three occasions, I refused to ‘take over’ and informed the Office of my reasons. There was confusion all round, with the outgoing Chief Engineer finally signing for accurate fuel and diesel figures, which showed a big difference between the official log book figures and actual quantities on board.
As the years went by, there were less and less of these falsifications, as the ship would come to know of my arrival much in advance.
The Atlantic Erie
The ship was discharging steel pellets during which I noted that there was a bit of spillage from the Loop Belts. I was told that it was normal, as the steel pellets kept slipping down the vertical of the Loop Belt. But the spillage was sufficient enough to keep 2 men busy in shoveling the spillage back on to the belts throughout the period of discharge. It was a total waste of manpower. That was my first notation in the pocket book I always carried.
The term “Lakers” was given to ships that plied within the confines of the Great Lakes, mostly bulk carriers of various sizes.
The history of Lakers are a fascinating read, as it encompasses all the drama of how a certain design of ships helped bring about an industrial revolution starting from the late 1800s, in a rather restricted area that was very difficult to traverse by land.
In the early phases of expansion of trade, of carrying ore, grain, salt, limestone, coal from one Lake to another, every activity was within the confines of the Lake Area, each supporting the other.
Ships were built for very specific purposes in a shipyard abutting the Lakes.
Ships were launched into the Lakes.
Ships plied within the confines of the Lakes for long periods of time, except for ice bound winters, when everybody shut down all activities and went home.
The evolution of Ice Breakers was a consequence of these idle months, with many ports being made accessible year round. But, there was always a marked decrease of nautical activity.
Small villages became ports and very rapidly mushroomed into towns and cities, almost all being prosperous cities even to this day. This was mostly on the United States side and less on the Canadian Side, more because of US Laws that allowed only US Flag vessels to carry US cargo between US Ports.
All the Great Lakes - Superior, Michigan, Erie, Ontario and Huron - being fresh water lakes, meant that ships plying in this area all year round were not subjected to the corrosion that sea water gives.
For the purpose of accessing more and more remote areas, where port facilities were more or less non-existent, Self Unloaders came into vogue between the years 1900 and 1910, starting from very simple and crude mechanisms to the more sophisticated equipment of today.
Lakers were primarily for trade in the Great Lakes’ areas, the restrictions of beam being more important than the length, to accommodate themselves in various locks. So, unlike the ships of today, they were longer in length and lesser of beam. Other ships, built in other countries, were built to certain proportion standards of length to beam.
Like I said, they were built for the Lakes. But, when the bulk carrier market was booming, many a Laker would escape the confines of the Lake and ply in international waters.
I was now on one such Self Unloading vessel, on a long term charter.
One of the more eerie aspects of a narrow of beam / long in length Laker vessel in rough seas, was the quite extreme flexing of the vessel, sometimes leading me to ask myself “When will she break?”
Controllable Pitch Propeller
As soon as we sailed out of Bremen, my first interest was in the mechanisms of the Controllable Pitch Propeller (CPP), which we had on board. When I queried the senior engineers about the system, the replies were very vague. When I asked them how they prepared the CPP for use (akin to getting the engine ready), their answer was the Hydraulic pump for the CPP was started remotely by the Bridge personnel and, as such, the Engine Staff had very little or nothing at all to do with the CPP, except check hydraulic oil levels in the tank.
I was uneasy about this attitude and checked for myself. There was a running hydraulic pump. But the standby pump had been dismantled and the casing was lying nude. A check revealed that the ship had been awaiting spares for this pump for more than six months.
I, then, started researching all aspects from a different direction.
What if the second (and running) hydraulic pump fails? How can the Bridge change the pitch of the propeller?
Answer : They cannot.
So, what can we then do?
Answer : We have to permanently secure the propeller blades at ‘Full Ahead’ position and use the Main Engine as a reversible engine till repairs are carried out.
There were, in that period, two schools at play in this niche segment of the marine industry, the leading lights being ‘Kawasaki’ 'Ka-me-Wa' CPP manufacturers and ‘LIPS’ CPP manufacturers.
Question : What will happen if the hydraulic pressure fails?
Now, I am not absolutely certain which is which, but one of the systems takes the propeller blades and moves them to ‘Full Ahead’ position (Kawasaki?), using the internal springs to push the blades to ‘ahead’ position.
In the other system, the propeller blades automatically take up a zero pitch position in the absence of hydraulic pressure. (LIPS?), after which, using a hand hydraulic pump, the blades need to be pushed to ‘Full Ahead’ position and locked.
My next question to my staff was “What are we supposed to do if this lone hydraulic pump were to fail?”
Maintenance / breakdown records showed that the first hydraulic pump had failed about 8 months ago and an ‘urgent’ requisition for spares was put up the same day.
The instruction manual stated the method by which the blades could be pushed to ‘Full Ahead’ position in an emergency, detailing the equipment / parts that are supposed to be on board for this operation.
The two most important ‘emergency’ parts were a hand hydraulic pump and the other a device like a large insertion thermometer with threaded top and a side connection with a female snap coupling.
No one on board knew that such things existed. A frantic hunt took place and 24 hours later the needed parts were found, having been relegated to a dark corner.
After we reached Norway, we tried out the emergency device.
A broad countersunk screw needed to be removed from the intermediate shaft. Done.
A 120 mm long tube (the insertion thermometer type of device mentioned above) with a quick coupling at its end had to be screwed into the intermediate shaft. Done.
A hand hydraulic pump had to be connected to this quick coupling after bleeding any air. Done.
A maximum of 20 litres of hydraulic oil - as per the manual - had been evaluated as the quantity of oil required to push the blades to ‘Full Ahead’ pitch. The pitch indicator did not show any movement.
We pumped almost 200 litres - no response.
Studying the drawing, I came to the conclusion that the safety valve in the hub of the propeller was leaking, thereby preventing the build up of pressure and allowing the oil pumped in to leak back to the hydraulic tank in the Engine Room. (The hydraulic tank had shown an increase of about 200 litres, noted on the float indicator).
The safety valve in the hub of the propeller can only be accessed after removing the propeller in a dry dock.
So, right now, we were in a situation where, if the only running hydraulic pump were to fail, the propeller pitch will come to zero pitch and we would be unable to pump the propeller blade pitch to ‘full ahead’.
If we were in mid sea when the last hydraulic pump failed, we would have no recourse but to call for a tow.


Our next port - discharge port - was Bremen, a voyage of 4 ½ days. We would have to cross the North Sea in winter and already the weather reports were not good.
However, there was one ray of hope. There was a different hydraulic pump meant for a different purpose, with different capacity and flow rate which could be used, but only after a lot of modifications to foundations and pipelines - an estimated 30 hour job. I did not like the risks that we would have to run if the weather were to decline. I had already been in such life threatening situations before and I did not wish to put the ship, crew and myself into such spots ever again, if I could help it.
And I could help it by making a bold decision.
I went up to the Captain’s cabin - a Canadian working directly for the Owners, Canadian Steamship Lines (CSL) - and briefed him. Although he had been on board (on rotation) several times, he was totally unaware of the risks that the ship had been running and asked me for a solution. We were still alongside in Norway, loading and had some time.
Two of the previous Chief Engineers had made these crossing several times, every 6th day, for the last 8 months, without understanding or realising the risks they had been running. They had not even checked out the 'emergency' arrangements.
I also did not like the fact that an ‘Urgent’ requisition for spare parts had been withheld this long - more than seven months - and in such a casual fashion.
The Captain and I then went up to the Bridge, where a GMDSS - Marconi Sailor set - was being used - no Radio Officer.
Having been trained by previous Captains in the use of the same Marconi set, I quickly sat down and sent out a medium sized message to Barber’s New Orleans, asking them to expedite the spares needed for the Hydraulic Pump before we sailed out of the Norwegian load port, Mo I Rana.
The reply was quick in coming - I was asked to wait till Bremen, which was about a week later, as they pointed out that the two previous Chief Engineers had not complained at all. I had been expecting this comment.
In my reply, I did not mince words that they should not expect me to be foolish enough to take such life threatening risks, which the previous staff had taken, knowingly or unknowingly, also pointing out that an ‘Urgent’ requisition should not take 7 to 8 months to be supplied. I told them I am advising the Captain not to sail out without the second pump being operational.
The Captain, who was beside me all the time, was, firstly, surprised at how I handled the ‘Sailor’ equipment and, secondly, the firmness of my decisions. After I finished, he wrote a brief note to CSL and copied all my Barber messages to CSL.
We finished loading the next evening and went out to anchorage to wait for the spares. Seven hours after we anchored, around 4 am, the spares were delivered on board. We took 6 hours to assemble and try out the repaired pump, after which we set sail.
The next two weeks saw a spate of stores and spares deliveries that had been pending for many months.
To round this particular incident off, I had sent for, and received, one more set of spares for the same type of hydraulic pump, suspecting that the pump that had been running all this while will give way soon. 40 days later, it did fail.
On such a fragile thread our lives do hang.
As for the failed operation of the change of pitch using the ‘Emergency’ device, the propeller was opened up in the next dry dock and, as I had suspected, the safety valve in the hub of the propeller was leaking. All overhauled.
One of the symptoms of internal or external leakage of hydraulic oil in or from the circuit is either the continuous running of the hydraulic pump - in case of a major leakage - or a repetitive stop / start of the hydraulic pump - in case of minor leakages. (something akin to ‘fridge plant problems). External leakages result in frequent replenishing of hydraulic oil.
Suffice it to say that a detailed set of instructions went into files, displays and ‘Handing Over notes’.
===== Continued in Blog 92 =====
Comments