Blog 84 - Happy Deepavali to all - I board a Pure Car Carrier - "Anna"
- ranganathanblog
- Oct 23, 2022
- 10 min read

Marine Musings 23 - MV Anna - Pure Car Carrier
Two consecutive tenures
First from 14th Aug 1989 ( Sheerness) to 14th Jan 1990 (Singapore)
Second from 15th Sept 1990 (Long Beach) to 16th May 1991 (Shimizu)

Courtesy Youtube
Shows an 18 cylinder engine - ours was 16 cylindered
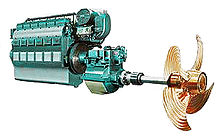
Courtesy Wikipedia

Courtesy dieselduck.info

Courtesy dieselduck.net
A 16 cylinder V type Engine, nearly similar to the 'Anna'

Courtesy Study Marine Engineering On Line

Courtesy National Maritime Center

Courtesy indiamart
Marine Musings 22
Chapter 1 - I join the ship at Sheerness, UK
As usual, I had gone to Mumbai to finish all formalities, sign my contract, pick up my air ticket and leave.
I know it is wrong of me, but I normally do not read the contract before signing it. It states what are the wages I am to receive during this contract.
I was, then, senior enough to receive the highest grade of pay which, then, was the 6th year scale. Something did not seem right when the Clerk, who was responsible for the ‘Anna’ staff, pushed across the contract for me to sign. I asked the Clerk what year wages he had put into the contract. He replied “First year wages’. I pushed it back and told him “I am going home in one hour if I do not get the right wages. Check it, correct it and let me know”.
After 15 minutes, he called me and told me “I have decided to give you 6th year wages. Sign the contract”. I was taken aback by the sheer gall of that Clerk and as I signed the contract, I said to him “ Shall I hold out my begging bowl for you to throw in some money? Don’t push your luck. Treat people properly and you will survive. Act arrogantly like this and you will soon find yourself at the door”. He paled and took my advice. I soon found out that he had been bullying and terrorising all the ship's staff who were obliged to go to him for completion of their documentation, contract clauses and other paperwork, with the threat that they will not get the job. I was certain of my suspicions, through some whispers, that there were also some money transactions. At the end of day, after my medicals, I collected all my papers from him, sat down in front of him and warned him about mistreating the floating staff. I read him the riot act and told him If he had not changed his behaviour by the time I next come to the Office, the consequences will be severe.
The ship “Anna” was a 11 year old Pure Car Carrier, with fixed decks and my first V Type Main Engine., medium speed with gearing. If memory serves me right, there was also a shaft generator.
I am unable to find a photograph of the ship.
There was no stern ramp, only side ramps. The 2 Main Side Ramps, one on the port side and one on the starboard side, were slightly forward of midships which, when lowered, served as the main ramp for entry into the Main Deck, with fixed internal sloping passageways, the only exception being one movable section on the main deck, to make it gas and watertight. A combination of hydraulic rams and winches / wire ropes were in place to lower and raise this ramp.

Courtesy macgregor.com
A Typical Side Ramp
This ship also had a narrower side door, located on the starboard side, about 3/4th or more towards aft of the ship’s length that could be raised and locked at either of two locations, to serve as the exit or entry point for vehicles into 2 decks well above the Main Deck. Pretty confusing?
A long, reasonably wide, portable ramp stowed on the topmost deck, starboard aft of the accommodation, weighing about 15 tons, would be lifted with a 25 ton crane and lowered over the side to hook on and lock on to the entry space created by the raising of the aft side door. (My purpose of these details will become apparent shortly).
This crane was also used for domestic use, to lift up stores and spares.
Unlike on later car carriers, the Accommodation spaces and other ancillary rooms were spread out over the large expanse of the top deck. This made for larger spaced cabins. But, being Japanese built and meant for Japanese personnel - her former name had been 'Hojin Maru' - the furnishings in the cabins were sparse and staid. Only the Captain and Chief Engineer cabins had attached bathrooms, toilets. The toilets being unheated and poorly insulated, we had to contend with ice in the toilet room. I took the liberty of directly ordering as many heaters as required from the Ship's Chandler in Japan.
For the others, there were common, open bathrooms that had showers and a heated 2 metre square cement tub for them to have a communal soak. They were supposed to have a shower and then jump in together. Good bonding.
After Barber’s took over the full management of the ship and after our crew joined, some makeshift stalls were provided to save the modesty of the Indian sailor. The problem came when Chief Officers or Second Engineers, or others below those ranks brought their families.
More modern, or later, car carriers had half their top deck area taken up as cargo space for cars, example Nosac Taishan. In consequence, as all cabins were on the top deck, they were smaller.
The Chief Engineer was going home in a hurry for a family emergency. The unwritten protocol during those kinds of takeovers is to assist in freeing him of his duties as quickly as possible.
That said, a few documents of vital importance need to be verified before signing, which can sometimes get to be an issue.
The quantities remaining on board (ROBs) of Fuel Oils, Diesel Oil, Lubricating oils is one such. The incoming Chief Engineer has to assure himself that the quantities listed in the Handing Over Documents are actually on board, as he will have to provide explanations - and maybe penalised - if any shortfalls are found at a later date.
I found there was no need of that, as the ullages and ultimate calculations were all done by the Second Engineer, who was a protege’ of mine, who I trusted. I only compared the calculated figures to the Engine Room Log Book figures and, finding the discrepancies to be minimal, signed the ROB document.
He was pretty distraught about his family. I told him not to worry, patted him on the shoulder and told him to forget about the ship and get home to look after his family.
He left within one hour of my boarding the vessel.
I was not too worried about the Engine Room, as the Second Engineer was a very capable hand.
The Captain was on his first tenure as Master.
The Chief Mate was an experienced one, just in reach of his promotion.
All in all, first impressions were that it was going to be a smooth tenure. And so it proved to be, except for some serious, unsolved problems that had been carried over for several years. On hearing of them, I took the bait and made it my mission.
The Aft Crane:
It was around 4 pm, on the same day that I had joined the ship. Discharging was going on. I was in the Engine Room, making myself familiar with various items.
I became aware and ‘heard’ of one of the long standing, chronic problems, when a huge ‘thud’ sounded from the top deck.
Running up on deck, I saw that the crane wire had parted just after the ramp had been removed from its locked position at one of the locations for cargo discharge. After lowering the ramp on to the wharf, the crew had rigged four wire ropes for the final lift to the vessel.
As the crane lifted the ramp from the wharf, the wire had parted.
The practice was to have four wire ropes to lift the ramp horizontally from the ship, lower it on the wharf, change to two wire ropes for one corner, lift one end till it reached the locking arrangement on the side door, lock the ramp in place - it would now be angled down to the wharf - and take away the crane hook.
The whole operation is reversed for stowing the ramp back on board after cargo work.
All had gone well when the crew had unhooked the ramp from the side door and laid it on the wharf, for changing over to four wire ropes and had started lifting, with long guide ropes to position the ramp and prevent any swing. Normally, the ramp would be swung around so that it comes parallel to the ship, lifted, brought on board, stowed in a forward-aft direction on the starboard side and secured.
But the crane wire had parted, the ramp fell about a metre on to the wharf. The crane jib, which was practically just above horizontal, came crashing down on deck.
There were no injuries, only a bit of cement had come off the wharf, the ramp was bent a little. The crane jib had suffered the maximum damage and was bent at the middle.
The Deck crew and staff did not seem very perturbed about it.
When I asked them if any had been injured, they replied that they were all fine. Their further comment jolted me; they said they were always careful of themselves and others when using this crane, as it is accepted that the jib will fall every 6 to 8 months or so.
The Chief Mate added that he had personally inspected the wires just a few days back and all was fine. Because of the history of this luffing wire parting and subsequent jib damage, every inch of the crane wire was inspected every month and the wire greased.
It seemed to be a problem even when the Japanese were operating the ship. The crane wire would part at intervals of around 8 months, seemingly for the last 11 years, from the time she came out of the shipyard.
For the moment, a shore crane with a good outreach and capable of lifting 15 tons was called. The crane jib, which was bent with nearly half the length protruding over the side, was first hooked up, brakes released, picked up, swung inboard and laid on the deck. The damaged ramp was picked up and landed on board.
The Hong Kong Office, when informed, took it in their stride knowing the history of the crane damage. They asked us to wait till Japan for shore workshop repairs, which was more than a month away.
I asked the Chief Mate to cover and tape the broken ends of the wire, to prevent corrosion by seawater or sea air.
I had just taken over a few hours back. It bugged me that a long standing problem had been dropped into my lap, like a ton of bricks, even though everyone accepted it and expected it to happen.
It also challenged me.
Over the course of the next two weeks, whenever I found the time, I went through the records of the past two years, since Barber’s had taken over. Everyone had done their best - they had inspected the wires frequently and found nothing amiss, they had checked the sheaves for any burrs, none found. They had checked to see if the right wire was being used; all wires, both luffing and hoisting wires, were as per manufacturer’s specifications. The Japanese, when handing over to Barber’s had cautioned them about the crane.
Only one report had mentioned that the split had occurred over the same length of the wire twice in a row.
A couple of weeks later, after attending to comparatively smaller problems in the Engine Room and in the Car Decks, I once again found myself sitting on the damaged jib and picturing the whole scenario.

Courtesy marineinsight.com

Courtesy picclub.or.jp
A damaged and bent jib
Slowly, I visualised each step of each operation, including the smaller nuances like limit switches etc. and could find nothing wrong.
Then I went into the crane housing and started working my way up. The hoisting and luffing drums seemed good. The wire guides were in good condition. The limit switches were all operational.
The next day, I went still further up and came to the trap door leading to the head or crown of the crane, where all the sheaves are located. Climbing up the ladder, I undogged the watertight trap door and climbed to the small platform next to the sheaves.
I was now standing on the topmost part of the crane and had a grand view of the entire ship. Looking aft, I could see the wake of the ship for miles. Looking forward, I was practically on the same horizontal eye line as the Engine Room funnel, with all the various exhaust gas uptakes’ goose necks pointing aft, towards me.
The ship was at full speed and the clear smoke was flowing past both sides of me and above my head - I could feel the current and the heat. Because of the exhaust, I could not stand there for more than a minute and was forced to come down, sit and breathe in some fresh air.
I am, by nature, a very slow thinker and have no ‘Eureka’ moments. But the thought processes slowly started evolving.
Reading some of the manuals, I listed some of the constituents of the flue gases that are emanated.
Oxides of Nitrogen (NOx) – create ozone
Oxides of Sulphur (SOx) – create acidification
Carbon Dioxide (CO2) – is a ‘greenhouse’ gas
Carbon Monoxide (CO) – a product of incomplete combustion
Hydrocarbons (HC) – gas, soot and some particulates
(Above list is from the Engine Manual).
Unburnt Hydrocarbons will dirty the place, as soot particles. Sparks ca be seen at night.
Carbon monoxide can cause death if inhaled.
Carbon Dioxide can disorient you and, finally, cause death through lack of oxygen.
Oxides of Sulphur - creates acidification.
Here I had it.
The exhaust or flue gases passing over the crane head was passing over the wires as well. Rain water and sulphur compounds form Sulphuric Acid, which gets soaked up by the wires, causes internal corrosion, weakens the core of the wire over a period of time. In this weakened state, the wire can part whether on load or an empty hook.
Records showed that only the luffing wire parted each time, as in this case.
The question, then, begs the asking “Why is only the luffing wire affected and not the hoisting wire”?
Because the luffing sheaves were directly in line with the flue gases, whereas the hoisting sheaves were located about half a metre below the luffing sleeves and did not get the full impact of the gases.
We cut pieces of the wire at the broken section and sent it by courier for lab analysis in Japan. Acidic corrosion from acids of sulphur was confirmed at a much later date, by the time we reached Japan.
Solution? At the next dry dock, raise all exhaust gas outlets in the funnel by a metre or so. Dry Dock Specifications were made.
Temporary fix? After every use, cover the entire crane head with canvas and tie it down to minimise smoke touching the wires.
The crane and ramp were repaired in Japan. The crane was load tested and certified. The ramp was tested statically and certified.
A few years later, I was told that there had been no more accidents on the crane.
===== Continued in Blog 85 =====
Wow! Ranga that's what is expected from a level headed, calm engineer, trained by DMET. Kudos to your finds and solving such a lingering problem, for years together. Don't you think our training in DMET and seniors brought us up to such levels, Now that you are talking about all such achievements, readers can have a rough ides about we the trained Marine Engineers. All said and done this is what we are trained for.