BLOG 81 - "Citadel Hill" - Self Unloader - A Quiet Hint - A Major Foray into Ballast Wing Tanks
- ranganathanblog
- Oct 12, 2022
- 9 min read

Chapter 3 - Dividing my time between Engine Room work and Self Unloader Plant work
The ship was built in 1967 as a Bulk Carrier by a UK Shipyard and later converted into a Self Unloader. She was 20 years old when I joined her.
The machinery on board was as old as the ship. Additional machinery were installed when the conversion took place. They included 3 more generators to take care of the load requirements of the newly installed Bow Thruster or the newly installed Self Unloader Plant.
Since I had two plants to look after - the Engine Room and the Self Unloader plants - I had to now juggle my time so that I can do justice to both. Quickly, I fell into a 30 -70 approach, where I spent 30% of the time for Engine Room work and 70% for Self Unloader work. For this, I needed efficient Second Engineers. My suggestion to the Head Office was that they send experienced Second Engineers who were nearly ready for promotion. Ships like the Citadel Hill were the perfect training ground to groom them for their promotion, as they were forced to take more responsibility.
The run was usually Houston or Tampa in the USA to load for Belledune or St John’s in Canada. We coasted the eastern seaboard of the USA both ways.
Currents
Right from my school days, I had been fascinated by the subject of Geography, particularly of Ocean Currents. Here we were being subjected to the Gulf Stream current for the majority of the voyage, either positively or negatively. I had many discussions with the Captain on how he takes advantage of the current one way and negates the influence of an opposing current the other way.
Under the tutelage of Capt Abraham on the “Taronga”, I had come to acquire a lot of knowledge about ocean currents, especially the “Kuro Siwo” current as we had to be in its vicinity for many days every month. How he would take advantage of it to increase the speed of the ship and how he would stay away from the current when it was against the ship, proved to be fascinating, albeit quietly.
My curiosity had been piqued - on the “Taronga” - when I found that the Bridge had been ringing down to ask ‘What is the sea water temperature’ practically every 15 minutes or so. So I had gone up to the Bridge to find out what was going on. It was then that I found the seawater temperatures were being recorded to find the warmest segment of the current, as it is likely to be the swiftest. Temperatures and velocities varied across the wide swath of the current flow, with the warmest and swiftest being in the very centre. Today, with satellite technology and information, all details of the current can be displayed for the Captain to make an informed decision. Pre 1990s, the water temperature was the best determinant of the swiftest part of the ocean current.
The reason why Capt Abraham used to ask for the temperatures in spite of the current being clearly marked on the navigational chart was that the current does not stick to one particular lane at all times. If flowing in a south to north direction, it moves slightly east or west depending on some meteorological variables. More like a car meandering along an empty highway, not bothering about lanes.
On the Citadel Hill, knowing that we were in the Gulf Stream, a warm current like the Kuro Siwo, I found it difficult to stop myself from quietly finding if the Bridge had called and asked for sea water temperatures frequently. I was told that no one had rung down.
Later, when I was with the Captain, I obliquely referred to my time with Capt Abraham and how he would be asking for sea water temperatures when in a following current. An hour later, the Engine Room started receiving calls asking for the sea water temperature. Mission accomplished without hurting any egos.
After that, on the flip side, I found that I was being called for or consulted on situations that really did not require my expertise.

Scijinks.gov - Gulf Stream Drift
Chapter 4
Slopes of Top Side Wing Tanks, Web Frames, Stiffeners

One of the situations that did indeed need my input was a pretty serious one.
A very frequent problem that nobody had really bothered about were the leakages of water from the Ballast Wing Tanks. It was so frequent and substantial in quantity that the water leaking from the Wing Tank would fall into the Hold and seep through the cargo gates and fall on to the Tunnel Belts. The Tunnel Belts would fill up, overflow and fall on to the tunnel floor, (which was the tank top) and make its way to the aft bilge well in the tunnel spaces, triggering an alarm.
The problem was the alarm was installed in the Self Unloader Control Room, which is not manned or tenanted during loading or during sailing, unless some maintenance work is required to be done.
We, later, connected the alarm, using a spare cable point and indicator, to trigger the alarm in the Engine Room - which was manned at all times.
During sailing on ballast, we woke up one morning to find the vessel slightly listed. The next observation came from the tunnel crew, who had gone down to find nearly a metre of water in the tunnel. Luckily, there had been no water ingress into any machinery. We pumped out the water.
After sounding all tanks, it was noted that one wing tank was nearly empty, where it should have been full. This ship had top side tanks and double bottoms not connected to each other, which meant a valve needed to be opened from the main deck to either fill ballast or drop ballast overboard by gravity.
To locate the leak, we had to fill the wing tank and watch from inside the hold. Since the wing tank covered (nearly) two hold lengths, we had to watch from both holds. To get into the empty hold, all we had to do was open one cargo discharging gate from inside the tunnel, get on to the tunnel belt and climb into the hold.
There were several leaks, 4 of them major. We then emptied the tank, went inside and checked the slopes. The plating was good but the welds between plates had eroded and, in some places, had wasted away completely, exposing the wing tank to the hold below.
As a temporary solution, a 90 degree angle bar was welded, resting both the edges to the steel plate so that it formed a tent above the eroded weld and sealing the ends, so that water could not enter. Many such leaks were repaired.
Chapter 5 - A high level meeting, a resolve, a plan and its execution
Suspecting that there would be many more such leaks in the future, I took a team and inspected all the tanks. Sure enough, there were over a thousand potential points of leakage. The ship side steel was good and the steel of the slopes was good.
But the welded seams were in bad shape. Quite a number of the internal members - stiffeners, web frames - were badly corroded and wasted away.
Within the next ten days, I prepared a detailed report - with a lot of help from the Chief Mate - with notations on drawings and photographs and sent it to the New Orleans Office. I also started thinking about what we can handle, how much we can handle and how we can handle steel jobs.
Meanwhile, we were trading between Miami or Houston to Belledune Canada, occasionally calling St. John's, New Brunswick.
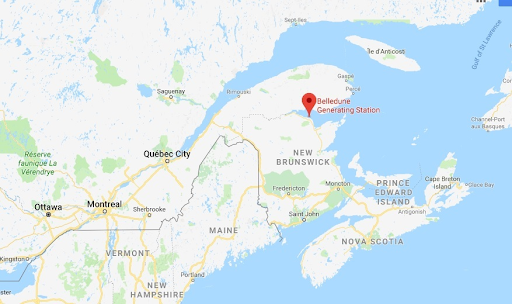
A week later, a message was received that a mini board meeting was going to be held on board with 6 members from the Owners (Upper Lakes), the Vessel Superintendent (Mr Ganapathy), the Captain and myself attending, when the ship reaches Miami.
After boarding, the visitors were taken by me to the worst of the topside tanks and into one of the double bottoms, for a thorough inspection. After lunch, the meeting started.
The Upper Lakes people, all in top positions, 2 from Management, 2 from Commercial and 2 from Engineering were very open and forthcoming. They frankly told us that the condition of the Wing Tanks was sufficient cause for them to decide on scrapping the ship, rather than plying her. Another factor - my input - was that the ship would not pass muster when the Classification inspects her during the next dry docking, due in about 18 months, without costly steel work in a shipyard.
I had already briefed Mr Ganapathy that I would like to be heard, so I was given the opportunity.
From my notes, I gave them an overall picture followed by specifics. I pointed out that the Double Bottoms were, generally, in good condition. Also, the problem in the Wing Tanks lay mostly with the welded seams and corroded web frames and stiffeners, all of which were renewable. Except for this, the ship was in sound condition, even with antiquated machinery.
I submitted a question to the Commercial people if the ship was making money and was profitable. They replied that this ship was making money hand-over-fist, much more than most of the others in the fleet. The scrapping of this ship would mean that they would find it difficult to replace her on this particularly profitable run, along with a dent into their coffers.
With this, I suggested that we do the necessary renewables before we get into the dry dock. I recommended a course of action.
Get an authorised workshop team to gauge the thickness of steel plates at various places - shipside, double bottoms, after peak, forepeak, Top Side wing tanks, their sides, slopes, web frames etc. to get a clear picture of how much of steel has wasted away. If too large an amount, then scrap the ship.
If within a limit that the Owners can work out for themselves, call Class Surveyor to attend and tell him our intentions to do the necessary renewables and ask them if it would be acceptable to Class?
If yes, then we should put 3 welders, 3 gas cutters, 3 platers and 3 helpers on board - 12 in all - on board, get the necessary steel of the required grade and quality, put extra welding and gas equipment on board and start work.
I pointed out the temporary repairs that we had done to the welded seams and suggested a gently sloped angle bar, prefabricated ashore to be welded over the weld seams. Irrespective of whether they were in bad condition or not, we should cover all seams this way.
As far as the web frames were concerned, we can cut away the thinned down areas, then fabricate new ones on board, keep them ready and, on good weather days, stop the ship, cut open the main deck and renew the web frames.
Ditto for the stiffeners.
Extra life rafts to be provided to accommodate the new members. (Accommodation was no problem).
After more detailed discussions, they gave the go-ahead.
The Gauging Team sailed with us one way to Canada, finished their gauging work and submitted their reports to BSM New Orleans, who sent it on to Upper Lakes with their comments. All agreed it was a feasible project.
On reaching the US, a Class Surveyor inspected the tanks, went through all reports and approved our intentions with two provisos.
That all the welding team competency certificates should be approved by Class / him and
That he be informed every time in advance of the vessel’s arrival in the US, so that he can inspect the work done, to ensure it is up to standards. (Actually, he was quite sceptical as to our prowess in doing the job, but changed his mind and admired the way the work was done at the next inspection).
Bombay sent us some top class welders, gas cutters and platers and we started work in earnest. I had been an average to good welder but had stopped doing welding work when it started affecting my eyesight a decade ago. I was really amazed at the skill of the staff sent by Bombay and the quality of their work.
The gauging technicians had marked off all areas of wasted steel. Mr Ganapathy, sitting in New Orleans, ensured a steady and timely supply of all necessary items, based on my (typed out) requisitions.
More details in my next narrative.
"Tip of the Day" -
'Sticking' of fuel injectors or exhaust valves in the respective pockets of cylinder heads are, mostly, due to leakages of fuel or water on top of the cylinder head. The fuel or water enters the small space in the respective pockets, solidifies, hardens and, finally, prevents the easy extraction of the fuel or exhaust valve.
Sometimes, fuel injectors get stuck inside the cylinder cover pockets. What should be a 1/2 job, stretches out to be 2 to 3 hours. Worst case scenario requires the removal of the cylinder head, a 7 to 8 hour job.
If the fuel valve does not come out even with the use of the prescribed jacking tool, the best option is to tighten it back and wait for the next port or anchorage. When the last few movements - starts- are expected on the Main Engine, slacken the holding down nuts of the fuel injector by just two turns and wait.
With the next start, the pressure created inside the cylinder will jerk up the fuel valve and loosen it. It can then be retightened. The fuel valve can then be removed easily when time is available.
Similar method can be used for stuck exhaust valves, but more care needs to be taken as the nuts are hydraulically tensioned. It is the more dangerous operation of the two.
===== Continued in Blog 82 =====
Comments