Blog 67 - "Marine Musings 18" - "Talabot" - Interesting 'Generator' Problem
- ranganathanblog
- Aug 24, 2022
- 10 min read

Foreword:
On the incident of the Anchor Chain running out to the 'bitter end', (Blog 65), I have received two comments, detailing their own experiences of a similar nature, one of which I had narrated in Blog 66.
Here is a second such incident from my batch mate and colleague, Auldius Pais.
Quote
I also had 2 instances of anchor chain running out to the bitter end due to the spline coupling between the motor & the hydraulic pump breaking.
The 1st instance it was while trying to re-float the grounded ship (tanker) in the navigation channel of a port in Algeria. We were departing port & the pilot had got off a bit early and the Captain misjudged the current at the right angle turning in the channel. We were trying to re-float the vessel with the help of tugs. I think that initially there were 4 tugs & no luck for 2 days. Then on the 3rd day an extra offshore anchor handling tug barge came to assist. That tug took one of our anchors on its barge and dropped it down a little distance away to help in pulling the ship away from the shoal on which we were sitting. With 5 tugs pulling & ship using engines alternatively in ahead & astern direction, the re-floating operation continued for another over 12 hours.
Then suddenly the ship came free when the engine was on full astern, all the reverse thrust came on the dropped anchor and the spline coupling broke. The anchor chain ran out to the bitter end & held on. The port was very keen on our vacating the channel, so that they can resume port operations. So with the engine on astern direction, we dragged the run out anchor with us out of the channel up to the anchorage. We had to remove the damaged motor/pump combined unit from place & replace it with the other side one, working overnight and next morning we were able to heave in the anchor & set sail. This was on a ship owned by the then East China Ship Mgt, which later became Farsund Ship Management.
The 2nd instance was on a car carrier in Barbers. We were waiting in anchorage at Nakanoseki, as the port was closed due to an approaching typhoon. In the morning around 9 am when the wind picked up speed, I was on the bridge with Captain at that time. Captain felt that the ship was dragging anchor. (It was not. Just the yawing action & ship swinging made it appear like we were dragging as he was checking on the visual bearing.) He decided to heave up anchor & move away and keep steaming to ride the typhoon. I told him wait for 10 minutes for us to get the engines ready & then heave the anchor.
From the bridge itself I rang up the engine room & told them to get the engine ready & rushed to the engine room. (On car carriers the bridge is forward of the ship & engine is aft). But the Bangladeshi Captain panicked and ordered the Chief Officer to start heaving up the anchor before we could get the engine ready. We had 6 cables on deck. Ch. Off. was able to heave in 1 cable against the gale force wind & then the spline coupling broke & the chain ran out to the bitter end. Captain wanted to cut the anchor chain & run away. But the office & the port authorities said no. We could not work forward with the wind force. So we came back to the safety of the accommodation. The anchor held the ship in position till the wind subsided in the evening.
In the mean time we were in touch with the office. I told the office (with my previous experience on the tanker ship) that the only solution was to shift the windlass motor from the other side & then heave up the anchor. But those in the office wanted to prove that they knew better. They did not believe that the spline coupling could or would have broken. They asked me to drain the oil from the motor & see if there are any broken coupling metal pieces in the oil. We could not find any. So they doubted my theory of coupling breaking.
Then all sorts of recommendations started coming. "On another ship in Fujairah anchorage similar thing happened and we were able to heave up the anchor by using mooring ropes from the other windlass tied to the run out anchor chain & heave it in. You also do it." (What they forgot was that on that ship the anchor was down only 6 cables when the electric motor burnt. Here we had full 12 cables run out to bitter end). Any way, trying their ideas, we wasted a day.
Then finally they reluctantly agreed to my idea of shifting the hydraulic motor from the other side. With that we were able to heave up the anchor to 6 on deck, again working over night till 3 am. We were all dead tired after running around for two days. Since the port was closed, we wanted to take rest.
But the office said heave up the anchor fully & proceed to the next port. All engine crew refused to come to the engine room as they were all dead tired. So I said OK you guys take rest, I will give engines. Hearing this 3/E reluctantly agreed to accompany me to the engine room. We gave engines till we came out of the bay next morning, put the engine on UMS on 2/E cabin & went off to sleep, till the pilot came for the next bay pilot.
Regards
Auldy.
Unquote
A point to be noted here is the two different types of arrangements for the windlass'. One is directly coupled electric motor to a gear box and a shift gear system. The other is a hydraulic motor coupled to the windlass', powered by a hydraulic pump located - most of the time - inside the fore peak store.
Each have their advantages and disadvantages.
The disadvantage of the electric motor is - as the windlass size is scaled up for large ships, the size of the motor needed becomes untenable.
The disadvantage of the hydraulic pump / hydraulic motor combination is that the exposed parts of the hydraulic circuit, which are on deck and exposed to the elements, are prone to corrosion and oil leaks from control valves and pipe joints.
Renewal or repair of control valves is not that easy - it can get messy at times- mostly at the wrong times, when all mooring equipment is being worked full swing.
Leaks from the pipeline joints are difficult to eliminate. Renewal of these hydraulic pipes is also difficult for ship's staff, as they are - normally - Schedule 160 pipes.
In hot climates, the exposed hydraulic system runs hot, reducing the viscosity of the oil and, consequently, the torque it can provide. Keeping the intercooler clean will alleviate this kind of a problem. If the hydraulic oil temperature peaks, a thermostatic cutout prevents the motor from being started, thereby rendering all thee winches and windlass' ineffective.
But the advantage is, the hydraulic system can assist with more torque when needed, as in the case of a 'runaway' anchor chain, if handled properly.
Very few electric motors can take the strain.
Marine Musings 18 (Cont'd): Talabot - Advance Party - Parallel Voyage of 27 Days and Taking Over from the Norwegians
ONE OF THE GENERATORS WAS BEING RUN FOR ABOUT 4 HOURS EVERY DAY AND THEN STOPPED
By the fifth day I had noted that one of the generators was being run for about 4 to 5 hours, then stopped, then restarted next morning. I asked the 1st Engineer if there was a problem with running it for longer periods. Normally, he would not have answered me properly, but after the couple of incidents that I had stated where I was able to sort out problems, he was freely telling me all the problems that existed.
The generator was one of them. He said that, over the last 6 months, this generator would run properly for about 6 to 8 hours on load, then would gradually slow down, till the rpm had reduced to a level where it would trip from the Main Switch Board. If started again after 2 or 3 hours, it would again work properly for the next 6 hours or so and trip again.
They had overhauled the entire engine, renewed all the fuel injectors, renewed the governor and overhauled the turbo charger, but to no avail. It would work well for 6 to 8 hours and slow down to the extent where the frequency and voltage would come down and the generator would trip off from the Main Switch Board. The generator would run without any problem when running idle, ie. without load. Luckily, he told me about it. If he had hidden this, it could have been disastrous later, when we had taken over, if the generator tripped during crucial times. I noted that their log book indicated the running hours of this generator was much lesser per month than the others.
From the next day, the Norwegians were bemused and intrigued when I spent all my time watching every aspect of the generator and, sure enough, the rpm slowly started to come down, the trip took place and then the generator would speed up to its constant speed of the set rpm. I understood that, because of this problem, they had not been running this generator on full load. They had always run it in parallel with another generator. I asked them to monitor the turbocharger rpm (using a hand held tachometer) against engine rpm and generator frequency. The turbocharger rpm would also drop along with speed drop.
The problem intrigued me over the next two days. After a lot of reflection, I started checking off various items on my mental list. It cannot be the Main Switch Board. The Governor was brand new. The turbocharger had been overhauled. The full engine had been overhauled, including the fuel pumps. It cannot be the fuel oil, as the other generators were using the same oil.
Along with their First Engineer, we checked the fuel pumps' timing after which I had to discard the notion that fuel pumps' timings could be a cause, after checking and finding the timing to be within the prescribed parameters.
With the drop in turbocharger rpm, I suspected that exhaust gas kinetic energy was dropping, which meant that exhaust gas was not flowing out freely. I started inspecting the exhaust pipe closely and slowly found myself 2 levels beneath the funnel top. There the exhaust pipe expanded for about a 2 metre height and again reduced back to the original size.
Almost all ships have spark arrestors and silencers fitted on to the exhaust pipes of Main Engines and Generators. They vary in design from simply expanded pipes to arrestors with meshes or fins to reduce noise levels and prevent sparks from going out of the funnel, as they can cause a fire.

Courtesy Marine Insight
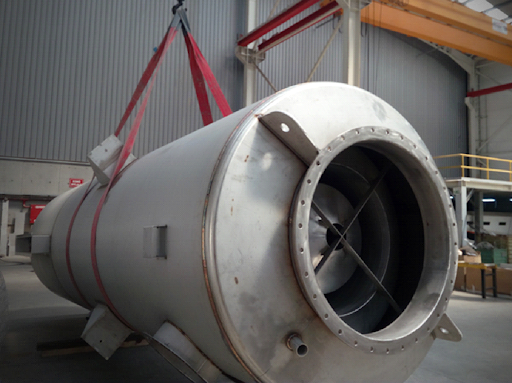
Courtesy Stopson Italiana
Something similar, but on a smaller scale, was what we had on the Talabot. Note the man hole for cleaning on the left lower portion of the spark arrestor. Note drain at bottom.
The 1st Engineer was with me every step of the way, as he was eager to study my thought processes and learn from it. When we reached the stage where we spotted the spark arrestor, we checked the drawing to see what was inside. The drawing showed a mesh and fins inside. We removed the lagging, opened the manhole – it was more like a large hand hole and found the hole choked with carbon. We cleaned out the hole and looked inside, it was choked with carbon. It took a few hours to remove the carbon, clear the choked drain at the bottom, wash the mesh filter and fins with fresh water and close up.
The next run of the generator was perfect, with no trips.
The problem was that exhaust gas did not flow out freely past the spark arrestor to the atmosphere, because of the reduced volume which had choked with carbon. So, the exhaust gas would gradually fill up the full length of the exhaust pipe from the engine up to the spark arrestor. Slowly, the back pressure would build up on the turbocharger and the exhaust trunking of the engine.
We cleaned up the other generators’ spark arrestors too. We stopped and cleaned the Main Engine spark arrestor also.
Searching the records, it was found that bad fuel had been taken on board some 7 or 8 months before, which could have caused an increase in carbon and other residue in the exhaust gas.
The sketch and photograph are to guide the reader as to what I have described above. Another problem solved.
Going from my own experiences, it would have been unusual to find a ship where these spark arrestors were part of the Maintenance Schedule or cleaned regularly.
I started including them in all my subsequent ships, the norm being once every five years. More often if the fuel is bad.
Engineers normally restrict their activities to platforms below the Boiler Platform.
The spaces above are neglected. After this incident, I brought out a check list - monthly - of what all to check from the area around the Boiler Platform and the subsequent platforms above it, right to the top, including opening the manhole hatch and inspecting the top of the funnel and the protruding exhaust pipes and drains.
Invariably, on the first inspection after joining a ship, I would see that
The drain from the funnel would be badly choked, sometimes requiring renewal of 20 metres of piping.
On two of the subsequent ships, the drains were choked, carbon had built up to the extent where the rain water would fill the top-of-the-funnel floor and overflow into the Engine Room.
The 3" coaming around the exit of the exhaust pipes on the funnel floor would be damaged, causing rain water to leak past the funnel floor into the Engine Room.
There would be several holes in many of the exhaust pipes' elbows, which would require attention in a ship yard during a dry dock.
All Engines' crankcase vents - led to a box in the funnel spaces - would be dirty, sometimes choked, causing back pressure to build up in crankcases of engines.
STRIPPING EDUCTOR PROBLEM
The 1st Engineer mentioned that they always had a problem with stripping the ballast tanks down to nil. There had been times when they had left port with 100 to 200 tons of ballast remaining on board.
Together, we opened the eductor and found a pitted diffuser and an eroded nozzle.

I explained to him that, for effective vacuum to be created, the nozzle should be smooth and even and the diffuser without any pitting, otherwise turbulence will be created in the diffuser, which would affect the creation of vacuum. It needed to be a stream lined flow from the nozzle, with supply of the driving fluid – in this case sea water – maintained at a steady 8 kg/cm2 or more. If maintained at that pressure and a nozzle that has no erosion, the stream lined flow is maintained and a good vacuum is created, which would suck out all the water from the tanks.
We renewed the diffuser and the nozzle.
In later months, I had no problems with stripping of tanks.
===== Continued in Blog 68 =====
Комментарии