BLOG 63 - A Main Fresh Water Pump Survey and Assembly of its Bearings
- ranganathanblog
- Aug 10, 2022
- 7 min read
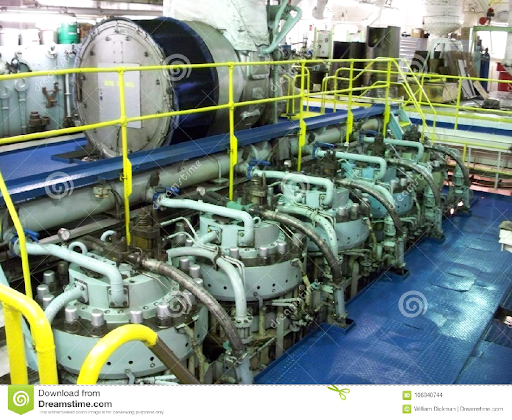
Chapter 4 – More About the ‘Willine Tysla’
Within a period of ten days, I came to realise that the last Chief Engineer had not only left me the legacy of personnel problems - created solely by him - but also one of logistics. Engine Stores were down to absolute zero. Simple and common items like rags for cleaning and hand gloves had not been ordered for months together, with the Engine Roof staff requesting the Deck staff for a few gloves and some rags and making do with this, without the knowledge of the Chief Engineer. Hand cleaners were not available, as they had not been ordered.
Welding equipment had not been ordered. Items like safety gear for welding were in a bad state. Various welding rods were missing. Silver brazing rods were not available. Even the Oxy - Acetylene cylinders’ gauges were not working.
On most ships, there is a common box for good quality ball and roller bearings that are used for all pumps and purifiers. Empty.
Spares for Main Engine and Generators were below minimum level. Similar situation existed for nearly all other machinery.
I spent the next two weeks making out requisitions.
The Engine complement were only three engineers, the Chief, 2nd and 3rd. The others were the Electrical Officer, the Fitter, 2 Motormen and one Wiper, for a total of eight. Previous ships had a minimum of 14. This ship, classed as an ‘Unmanned Machinery Spaces’ ship, had reduced staffing for the Engine Room.
With reduced manning came the problem of quality of maintenance, of the contribution of every member of the team and proper co-operation between all members. I was given a fragmented Engine Room – in terms of personnel – and I had to bring them all together. The stumbling blocks were the arrogance of the Fitter and the ignorance of the Electrician.
I found, very quickly, that the Electrician was not fit to even be a ‘wireman’. His knowledge of electricity was worse than mine, and mine was pretty poor, to start with. His job description included looking after the deck machinery. The derricks were electric winch’ operated. A number of contacts were part of the circuitry. His method of cleaning contacts was to use emery paper on the contact surfaces. (When writing this, I was, amusingly, reminded of the Australian cricket players using sand paper to get the ball to ‘reverse swing’ in South Africa).
The cranes were hydraulic, with a number of different types of valves. His method of fixing a problem was to take a hammer and bang on all the valves – I saw most valve bodies had dents from the hammering that they had received. He had been surviving in the Company by ingratiating himself with the Chief Engineer and Captain for over 4 years. I had no choice but to ask for his replacement, which was done within a week.
I started being strict with the Fitter, which was rather unusual of me. But his shouting at the 2nd Engineer bugged me. He was competent enough, but arrogant, and thought he knew everything.
Hardly 2 weeks later, a few machinery surveys by Class were to take place. One of them was the Main Fresh Water Pump. I told him to dismantle the vertical pump and keep it ready for survey and showed him how free the pump was by turning the coupling with my hand. I also told him I expected the same free rotation after assembly. He was assisted by the wiper. The vessel was in port for nearly 3 days. All items were passed by the Surveyor on the 1st day itself, so assembly could be done immediately.
The pump was nearly similar to the drawing below. Two double row angular contact bearings were used to take up the axial as well as the radial thrust. Both bearings are the same in every respect, but they have to be assembled 180 degrees from each other. So, on dismantling, one has to carefully note how the bearings are installed. All other assembly is pretty simple. I ensured I was present when the bearings were removed and had noted the assembly.

Courtesy Pumpsandsystems.com
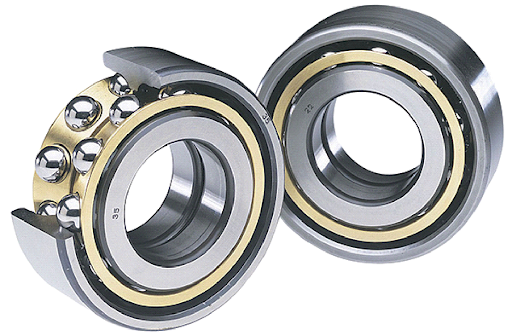
Double-row angular contact ball bearings. These bearing arrangements are used extensively as the primary thrust bearing in ANSI standard centrifugal pumps, among others.
After the survey, the Fitter assembled the pump and wanted to try out the pump. No parts had been exchanged or renewed.I told him to wait and checked to see if the shaft rotated freely, as it was before work was started. The shaft was very tight and could not be turned by hand. He insisted that after starting the motor, it will become free. I told him I want it to rotate as freely as it had done before working on the pump, which I had shown him. I told him to open and redo the pump assembly. He was also consulting the instruction manual regularly.
Just to make sure that he does not try to start the motor in my absence, I took out the fuses and the contacts and kept them with me. Over the next full day, he kept dismantling and assembling the pump. He must have done so at least 10 times without success.
I was being vindictive, but he needed to learn a lesson. 4 hours before we were to keep engines ready, he gave up and said it cannot be done and we have to start the motor to make it free. I told him to leave the job and sent him away. Calling the Wiper, I opened the pump, placed the ball bearings correctly, assembled the pump. The shaft now rotated freely and the pump was ready in 2 hours.
The Fitter was shaken. After this incident, he became docile and a good worker.
Chapter 5 – About the Engine, Accommodation and Deck
THE MAIN ENGINE
This ship had a Mitsubishi Sulzer 7 RND 76 Main Engine.
Sulzer RD and RND types had no exhaust valves. They came later, on Sulzer RTA and other models.
With no exhaust valves, cross scavenging prevailed, which was much better than the loop scavenging on MAN engines of that period. But, surprisingly, the deposits in the ports of this engine were much lesser.
The reversing system was different and unique and used ‘lost motion’.
Sulzer engines have lost-motion servomotors on the camshaft. These servomotors are useful to rotate the fuel pump cams to their astern positions. ... Lost motion is a term which means the timing has been retarded by a certain angle with respect to the new direction of rotation.
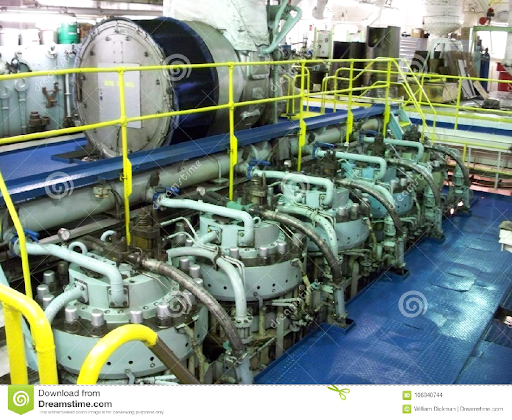
Courtesy Dreamtime.com
Note the absence of exhaust valves.
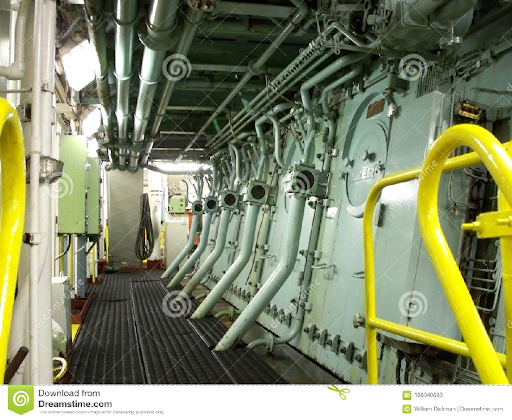
Typical Lower Level of a Sulzer RND Engine
The Sulzer engine was supposed to be the “Engineer’s Engine”, as per some of my colleagues who were studying with me during my Chief Engineer’s exam.
They would extol its virtues and its refinements.
I did not find it any different in any way, except that there were more servomotors used. It used the same 2 stroke cycles and the same principles for combustion. But I had an opportunity to become familiar with a new type of engine. The Sulzer Instruction Manuals were definitely better than other engine types. Along with the rest of the work, it kept me occupied.
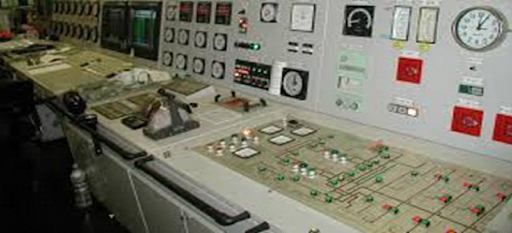
Courtesy marineautonationnj.com
Above is a typical Engine Room Control panel, containing alarm panels, monitoring systems and maneuvering controls.
THE ACCOMMODATION
I thought the ‘Ad Astra’ accommodation had been very good – this was even better. Going by the norm, Japanese built ships had a reputation of having lousy standards as far as accommodation and crew facilities go, but the ‘Tysla’ had obviously been built as per European standards and, more so, for the Norwegians, who pride themselves on giving the best of facilities for their crew.
My cabin, for example, had a well furnished office, a comfortable day room where the highlight was the large bay windows overlooking the main deck and a large bed room with a double bed, which had, for the first time, a good and indulgent mattress. A small bar, a TV with a VCR and a good music system were all part of the day room. It was a mirror of the Captain’s cabin that was on the starboard side of the same deck.
I am certain the Chief Cook and the Galley staff were delighted with the galley equipment. All kinds of gizmos, mostly in stainless steel, were provided. With very little effort, the galley could be kept amazingly clean. The crockery and cutlery were ‘Noritake’, one of world’s leading companies.
Everybody on board were buying 32 piece and 48 piece ‘Noritake’ dinner sets for taking home. I knew that, if I were to buy a set, it would likely be stowed in a corner and used only when a party takes place. So, I was one of the very few who did not buy any ‘Noritake’ items. The same went for ‘Mikimoto’ pearls.
The ship had a unique key system. Each person had a key which would open his cabin. It would also open the doors of whichever area or space that he holds responsibility for or where he will need to work. He cannot enter other cabins or areas where he has no business. The Captain, the Chief Officer and Chief Engineer had a Master Key that would open all doors.
DECK AND DECK MACHINERY
Basically built as a Multi Purpose Carrier (MPC), the cargo carrying concept was similar to the ‘Taronga’. 2 container sections and capacity of carrying containers on hatch tops for a total of 650 odd TEUs, with break bulk cargo in the holds and ‘tween decks, special coated tanks for carrying palm oil, were all part of the variety of cargo that can be carried.
Cargo Gear – Please see photograph below. From forward to aft
Derricks small capacity – I forget the SWL
25 ton (individually) Fuji cranes; 40 Tons SWL when Geminied
200 ton Stulken jumbo – can plumb either side
Smaller derricks
25 ton (individually) Fuji cranes; 40 Tons SWL when Geminied
Derricks just forward of the superstructure – SWL unknown

Courtesy khi.co.jp
Representative of a twin (or Gemini) crane operating separately
Requires 2 separate operators, one for each crane, the advantage being each crane can plumb 2 different holds.
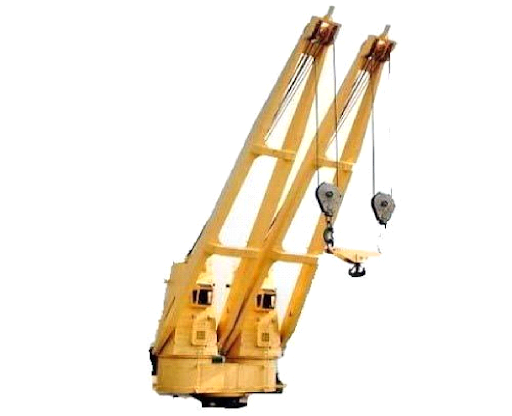
Courtesy India Mart
Representative of the two Gemini cranes working together
Requires only one operator sitting in the Master Crane. When combined, can lift 1.8 times the capacity of a single crane.
With the new Electrical Officer, I was able to upgrade the condition of the hydraulic cranes, in the course of which we had to undo the damage done to valves by the previous Electrician.
After a concerted effort over a period of 15 days of cleaning filters, renewing damaged valves and making the necessary adjustments, I was surprised to see that we did not have any problems over the next 8 months.
Crane and winch operation was done by deck staff. Somehow, they used to invariably make a mess of the twinning of the Gemini cranes, which meant the Electrician and I spent at least 2 to 3 hours rectifying the fault and adjusting the twinning circuit. After the 2nd such incident, the Electrician used to do the twinning himself and hand over to the deck crew.
The ‘Fuji’ cranes were about the best cranes that I have worked on, with no problems if operated properly.
===== Continued in Blog 64 =====
Comentários