BLOG 53 - "Marine Musings 14" - MV Taronga - Back to the 'Willine' Run - Still a Second Engineer
- ranganathanblog
- Jul 6, 2022
- 12 min read
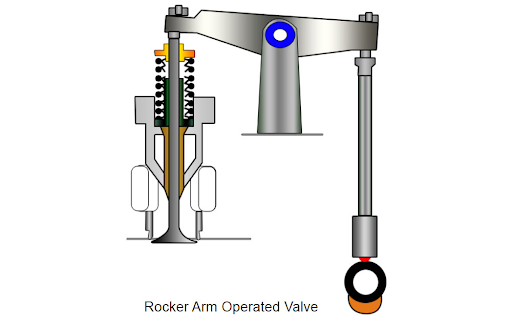
Courtesy Crew Traffic
Marine Musings 14 – MV Taronga – One More Tenure as Second Engineer.
Tenure From 15th July 1980 to 3rd April 1981
Chapter 1 – We Spend a Few Months in Singapore – We join the Taronga at Outer Roads on 15th July 1980
More than a year passed before I joined back for my next contract. I had got off the ‘Tema’ in May 1979, got married in Nov 1979 and gave notice for rejoining in January 1980. Barber Ship Management had very few ships at that time, most of the older vessels having been sold by our Principals, Wilhelmsen. The earliest they could give me one was in end June or beginning July of 1980. I said I would wait.
Meanwhile, in order to once again start getting my Non Resident status, my wife and I flew to Singapore end March 1980. Those days no visas were required. As it turned out, I had to wait more than 100 days for a ship. So, we went around Singapore, toured Malaysia and came back to Singapore. I also spent a lot of time with the Manager of the Singapore Office, Mr. K. Datta, helping him with his work and, in the process, became familiar with Office work. During this stay, I also spent quite a bit of time in the ‘Unitor’ workshop, honing my welding skills and advancing my welding knowledge.
The observant reader may have noticed that, after leaving SISCO, all the ships that I worked on were named with the letter ‘T’ in the beginning. All Wilhelmsen ships have had this lineage for a very long time, over a hundred years. The funnels differed from two orange vertical stripes to two blue bands. Both shown below.


Photograph courtesy globalmariner.com, whilst ship was at Manila, sometime in 1978
On 15th July 1980, my wife and I, after clearing Immigration at Clifford Pier, boarded the MV Taronga as she was passing Singapore. We went out by a launch and boarded the ship at ‘Outer Roads’ as she slowed down. The gangway was lowered. Helpful hands picked up our luggage from the launch and we safely came aboard. The outgoing Second Engineer signed off when the ship reached Hong Kong.
After the take over of the ship by BSM Hong Kong in 1979 and changing her country / Port of Registration from Trondheim (Norway) to Singapore, the Funnel (Logo) was changed from the two vertical orange stripes to the two blue horizontal bands, as shown in the photograph above.
The set up on this ship was different in terms of nationalities. The Captain, Chief Engineer and Chief Officer were Norwegian, the rest of the Officers being from India. The crew were from Singapore. I was the senior most amongst the Indian Officers. This became relevant after a few months, as I will explain later.
Unlike the previous 28 and 20 year old ships, this one was 12 years old, built in Uddevalla, Sweden in 1967. and was in very good condition. The outgoing 2nd Engineer – I think it was Gonsalvez – had done a good job. Unlike the Tarantel, we had a good and detailed ‘handing over’, in which he explained about some long standing issues which can give problems, in order to insulate and soften the pain of finding out at a later date. I have to thank him for such openness.
During a take over, many a time you inherit legacies of previous years and mistakes of others. It is important that a detailed mention of it is made by the party handing over. There are ethics involved here, the ethics being that one is as open and as honest as he can be in preparing an incoming Engineer. He should be briefed on the problems faced and existing condition of each bit of machinery in the Engine Room and on Deck. But sadly, not many people brief the incoming person either verbally or through prepared notes. More on taking over later.
We were on the Willine Line Service, just as on the Trianon. 3 ports in Japan namely Kobe, Nagoya, Yokohama, Hong Kong, sometimes Manila, Singapore, then Persian Gulf ports namely Dubai, Abu Dhabi, Dammam, Bahrain, Kuwait and back. We had to keep our schedule to the last 30 minutes. The schedule was for 6 months, published in newspapers, printed in attractive pamphlets and marketed.
We could carry containerized cargo, break bulk cargo, heavy cargoes up to 200 tons, refrigerated cargo in holds, palm and coconut oil in segregated tanks and other combinations of cargoes. For that particular period, she was a very versatile ship because of the variety of cargo she could carry.
It contained top class deck gear for cargo work. A 40 ton derrick plumbing # 1 hold, a 200 ton ‘Stulkien’ Derrick plumbing # 2 and # 3 holds, 2 sets of 4 cranes that can lift 25 tons, these can be used for container holds A and B and also for # 2 hold and the hold just forward of the super structure. There were also 4 x 5 ton cranes, running on center rails, midships. So, the hatch covers were divided port and starboard, with a space in between for the 5 ton cranes to move on rails.
With this much of deck gear, the machinery involved also was numerous. Loads on generators will definitely be high, hence generator maintenance will be very important.
The Norwegians were on a 4 month rotation cycle. Being from the parent company, their tenures and pay scales were different. The first set of 3 Norwegians that I dealt with were nice people and I got along well with them.
Chapter 2 – About the MV Taronga’s Machinery
Once again, the Main Engine was a later model of B&W, but still with rocker arms and push rods. Design changes were more in the material of the components, making them more reliable. Crankcase bearings, when opened, were found to be in perfect condition after more than 12 years in service. One new feature that I saw was the introduction of 2 Auxiliary Blowers, one fitted forward and another aft of the scavenge spaces to supply air to the engine at lower speeds. An automatic cut in / cut out processor was installed for these blowers.
For the first time, I worked in an Air Conditioned Engine Control Room (ECR), from which some of the machinery could be started and stopped. The Main Engine was one of them, but not the Generators. The Main Switch Board was located in the ECR, making the processors more reliable. Many more parameters were being monitored through several analog processors, which would give an alarm at the set point. Most of the donkey work that we had been doing on other ships, like temperature control, level control were all automatically controlled through sensors, feedbacks and regulators, all of which could be monitored either locally or in the ECR.
The Alfa Laval Purifiers were automatic and reliable. If any of the pumps failed or pressure drops, the standby pump would come on automatically. We were just short of being classed as ‘Unmanned Machinery Spaces’. The Auxiliary Boiler was automatic, saving us loads of man hours.
Since it was a General cargo + Container ship, the ballasting and de-ballasting operations were not as severe or as frequent. The Deck Cranes were ‘Haggelund’ cranes and required constant care. Some of the winch motors used to burn out once in a while, a long standing problem, cause unknown.
Life Boats were still open boats. To me, this was a disappointment, since I always felt that covered boats gave a psychological boost to the survivors who had to take to the boats. More about this in another narrative.
Chapter 3 – Problems and Solutions – Burn Out of Exhaust Valves
One of the advantages of Norwegians sailing on Barber Ship Management vessels was that, at the time of the Management taking over from the Parent company, all the Norwegian maintenance records remained on board. They were in the Norwegian language.
As on other ships, my eyes fell on the long lasting problems almost immediately. There were several.
Burn Out of Exhaust Valves - at Least 3 Every 2 Months for Over 4 Years
A recurring and persisting problem was one of burning out of exhaust valves. If one is alert enough, a virtual red flag will be displayed if excessive amount of spares for one part or unit or pump or compressor or boiler etc. are present on board. It means that the problem has occurred often in the past and each time the parts have been renewed, but the cause has not been found. This was the case with the Main Engine Exhaust Valves. The normal quantity of Exhaust Valve spares carried for a 9 cylindered Engine would be a maximum of 3 sets. Here we had 8 spindles, 8 seats, O-rings galore, bushes in plenty, along with plenty of other parts that constitute an Exhaust Valve. Out of the 8 spindles and seats, 2 of each were burnt and had to be landed in Japan for reconditioning, to be picked up after 2 months. So, I anticipated exhaust valve burn outs. Since these had not been recurring problems from when the ship was launched and had been occurring for, may be, five or six years or whatever time period, it is logical to assume some circumstance changed when it first occurred and nobody checked then or subsequently.
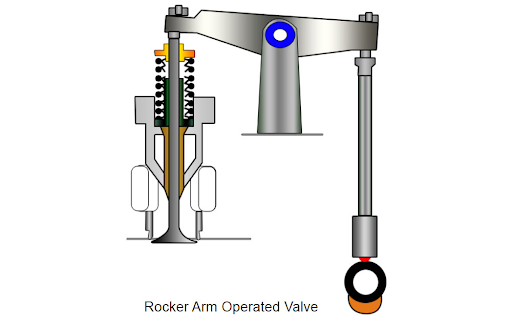
Courtesy Crew Traffic
I had been told that, for the past few years, all personnel had assumed the cause to be either metal fatigue or bad ‘stelliting’.
“Stelliting” is a process by which an amalgam of alloys, like cobalt, chromium, tungsten, molybdenum and carbon are heated together and are spray welded on to surfaces to harden them and make them abrasion resistant and also acid resistant. The future would also see ‘nimonic valves’ as an improvement on ‘stellite’ valves.
Sure enough, one day before reaching Japan, one of the unit’s exhaust temperatures started soaring. We stopped engines for a couple of hours and did the needful and changed the Exhaust valve with a spare, ready one. When we reached Yokohama, we landed all the burnt valves, seats and a cracked cylinder head for reconditioning.
During the stoppage, as the burnt Exhaust valve was being lifted out from the cylinder head, I noted that the Valve Seat and the Valve Lid had a burnt hole. Taking the center point of the cylinder head, it could be seen that the angle of the burn out and the angle of the fuel injector was on the same line. I drew a diagram in my note book as a record and as a start to my investigation.
The next burn out occurred after Hong Kong, exactly 180 degrees away from the first one. There were two injectors on the cylinder covers, 180 degrees apart and burn outs have occurred on the same radius from the center.
Et sequitur, the fuel injector has something to do with the burn outs. So, I tested a couple of the overhauled spare fuel injectors.
Unlike other engines, please note that injection is from one side face of the nozzle. Four holes are provided, more or less vertical to each other, one on top of another, so four jets of fuel issue out of these four holes.

Courtesy teambhp
Note the angularity of the studs in the inner periphery

Courtesy marinediesels.info
Usual nozzle design is to have several injection holes, all on a horizontal plane around the circumference of the nozzle or have one hole in the center of the nozzle.
Due to the centre space on the cylinder head being dominated by a vertical exhaust valve, all other mountings, perforce, have to be on an outer periphery, that too at an angle, so that they are relevant to the hemispherical combustion space.
Here we have a design where, first of all, the bore for the injectors on the cylinder cover is not vertically drilled into the cylinder cover, but is at an angle.
Below is a pictorial representation of the placement of fuel injectors with respect to the exhaust valve, not at all to scale. Both fuel injectors’ 4 nozzle holes spray their jets inwards into the cylinder; to be more realistic towards the small amount the exhaust valve lid that protrudes into the combustion space.

Courtesy Marindiesels.info – not to scale

Showing Nozzle Holes
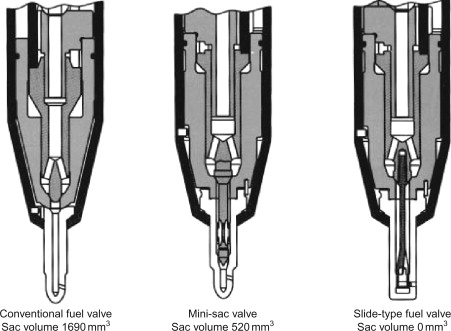
Courtesy sciencedirect.com
The first nozzle on the left is a good representation of what we had.
I do not recollect the nozzle hole size. These nozzle holes are drilled into the metal and then milled to give a smooth, stream lined flow to the fuel flowing through. With this stream lined flow and the pressure of fuel at this point, good atomisation and penetration takes place. But, after sometime, the smooth flow of the fuel through the nozzle hole is upset by erosion and the fuel starts getting scattered and following unpredicted paths. Besides impinging on the exhaust and causing the burn outs, a turbulence is created within the combustion space, which makes for poor combustion. In consequence, exhaust temperatures were higher, the smoke was black and output lower.
Jets of fuel in those unpredictable paths sometimes start landing on the exhaust valve lid which is already hot. This causes localized overheating at the point of contact of the fuel on the metal of the exhaust valve lid. This happens over 100 times a minute. Within a short period of time, a hole appears in the metal, more or less as if drilled by the jet of fuel and the extreme heat in the combustion space.
Testing the fuel injectors on the work bench which had old nozzles and comparing the jets / atomisation with ones fitted with brand new nozzles, showed a very erratic pattern with old nozzles and a more stream lined flow with new nozzles. Using a magnifying glass, checks of the old and new nozzles confirmed the serrations inside the old nozzles’ holes.
The Norwegian Chief Engineer was puzzled that, for nearly 4 days, I was spending my time testing fuel injectors, which is a job normally done by the 3rd Engineer. After I took him step-by-step through my investigation of the past week and my final findings, his opinion of Indian Engineers went up several notches. He then checked the Norwegian Maintenance Records and found that the burn out of Exhaust valves had been taking place for at least 4 years and all that everybody had done was to change the Exhaust valve and send the damaged pieces for reconditioning. Nobody had related the burn outs to fuel injector nozzles.
I recommended an immediate renewal of all nozzles of all fuel injectors at one shot, including the spare ones. This is because we did not have a detailed record of nozzle renewals; if renewals had taken place, the particular fuel injector could not be identified.
First order of the day was to requisition enough nozzles for the renewal of the entire number of fuel injectors on board, plus a few to keep as spare. This parcel of spares came within 20 days and within 2 more days all fuel injectors on the engine were running with new nozzles. After that we had one valve burn out, which was a remnant of the effect of previous serrated holes in the nozzle.
Next step was to chart all renewal of components of each fuel injector, using the Manufacturer’s number on each component. We went further and started charting which fuel injector was fitted where and it’s progress to different units and co-relating it with rises in temperatures, valve burn outs and other problems. In today’s world, this would have all been done on spread sheets or Excel or customized, dedicated software. There were no computers then – you had to make your own spread sheets.
It must be remembered that quite a number of components journey from one unit to another over a period of time. For example, take fuel injectors. Both the injectors of # 1 unit are due for overhaul based on their running hours. They are removed and a spare overhauled set of 2 are installed in # 1 unit. The removed valves are overhauled, parts renewed if need be, pressure tested, covered to avoid dust and put on the spares stand. It may find itself being installed on # 6 unit after a few months. This migration, if tracked with diligence, will afford insights into any problem that keep coming up. The running hours so maintained will tell us when to discard the nozzle, after reaching 12,000 running hours or as specified by the Manufacturers. This was a luxury that I had never seen in my first Company, SISCO, where all the nozzles, needle valves, guides, were all reconditioned on board and hardly ever discarded.
The Chief Engineer asked me to write a detailed report, with sketches, and he sent it to the Hong Kong Office as well as the Oslo Office. It was well appreciated and used as a template for other ships having similar problems.
This investigation led me much further than I intended to go. We had been stopping and changing these burnt out exhaust valves mostly at sea, thereby each time throwing the schedule of arrivals off by an arithmetical progression of nearly 2 hours, depending on the number that burnt out in a voyage. These were being changed when the exhaust temperatures of that particular unit shot up by at least 150 degrees to 200 degrees C or more than the other units. I needed to find a way of finding out when the valve starts burning out. There must be some indication from some source.
I had the habit of checking the Exhaust Temperatures of each unit on the remote monitor in the Engine Control Room and comparing them to local pyrometer temperatures, to the extent I nearly knew all the temperatures by heart, how much (approximately) they would fall with each reduction of rpm and so forth. I had seen a strange coincidence – the exhaust valve that would burn out after a week or ten days, would have a higher exhaust temperature for a longer period as compared to other units, when the rpm is brought down to maneuvering levels. As an example, if the average temperature across units is (assumed) 320 degrees C at sea, with deviation of – or + 20 degrees C, nearly this same deviation would prevail when the rpm is brought down in stages, under normal circumstances. But, if an exhaust valve is in the beginning stages of burning out, its exhaust temperature would not come down for a much longer period when the rpm is reduced while all the other units' exhaust temperatures come down much faster, creating a much higher deviation from the average.
Thus, by watching the exhaust temperatures during decreasing rpm and speed, it was possible to locate the beginning of a burn out, which was then seen to in port in lieu of stopping at sea.
Within two months, there were no more burn outs.
===== Blog 54 to Continue =====
Lovely way to show the world of readers how we the Marine Engineers did keep our vessels floating as well as plying all over the world. Delivering cargos at scheduled time. None of us bitched about the daunting work (repair/maintenance) we faced, day out and day in. No complains Mate.