BLOG 44 - Marine Musings 10 - Bombay to Kobe. I join MV Theben at Kobe
- ranganathanblog
- Jun 5, 2022
- 12 min read
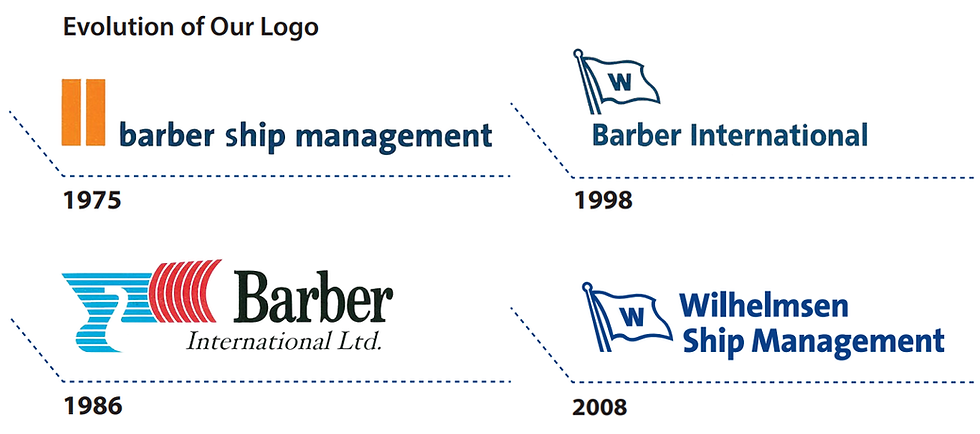
Marine Musings 10 – I join Barber Ship Management as 2nd Engineer
Chapter 1 – A Short Narrative on Barber Ship Management and Management Companies
Barber Ship Management, Hong Kong, was a sister company of Wilh Wilhelmsen of Oslo. The parent company’s old ships were given to their Hong Kong unit for management, flag changed but name retained. This management section was started in end 1975, with the ships registered in Singapore initially. They initially transferred 5 old ships to the Hong Kong unit in 1975, with the idea of increasing the fleet by slowly transferring more ships from Oslo to Hong Kong.
The first five ships had a full staff of Indians, all Officers and Crew being from India. We were being paid almost double of Indian Company wages.
Why did the Management Companies come into existence? In those days, Europe based shipping companies were more or less monopolizing world trade, with Japanese companies slowly entering the market. European wages were high, at least 3 times as much as what Indians were getting in foreign companies. The ships were also getting old.
Some of the German companies like ‘Hansa’ and British companies like P&O, Blue Star and several other companies had been employing Indian Officers in lower junior ranks, even if they were holding Master’s or Chief Engineer’s Certificates, the Europeans and the British assigning the senior ranks to their own countryman. Quite a number of the crew were also Indian. At that time, staff wages were a major part of the ship’s running expenses.
The oil crisis of 1973 saw many a shipping company trying to survive by cutting costs. To cut costs in a well entrenched financial and national setup meant thinking out of the box, which gave rise to Management Companies.
Captain Charles Vanderperre, known as the “Father of Third Party Ship Management” was the pioneer in this who, after a brief stint with Wallems, set up his own Company “Univan”. Soon after, seeing the benefits, many European Ship Owners set up their own Ship Management companies, most of which were head quartered in Hong Kong.
Setting up Management Companies was a boost to their coffers as they had to pay only around 1/3rd the wages, they needed to pay no pensions, no provident funds, no gratuity, no social security or many other benefits that were normally accrued to European or British staff. They had to only change the registry of their ships to another country that had more tolerant tax and shipping laws. They could, then, send their national crew to their newer acquisitions and take on Indian staff for their older ships who were, even then, as equally or better qualified as their national staff.
At the same time, they were getting rid of their older ships and milking them dry in their last years. Fresh new tonnage was needed due to the pace of world wide expansion of trade.
Today, we may see it as discrimination. But during those times, the Indian economy was pretty bad, with most lower middle class families struggling for their daily needs. Any aspiration to move to middle class status was a stupendous one. Families spent most of their income mainly in educating their children. A shipping job, especially in a foreign company was God sent, as it really boosted financial conditions for a family.
One must remember that if the Management Companies’ employees pay was on par with their European counterparts, then the parent company may as well employ their own countryman. We Indians benefited tremendously, so did the Owners.
For about 8 years, Barber Ship Management Hong Kong were, mostly, looking after their parent company vessels, after flag and crew changes. I played a big part in many of these transfers during my service with BSM, as I was sent as advance party on a few occasions.
Around 1984 / 1985, a resolution was passed by the Wilhelmsen Board that each entity will, henceforth, have to be financially responsible for itself. In other words, they had to start being self dependent and not look for financial sustenance from the parent company. The Ship Management entity and the Wilhelmsen Agencies entity which, till then, had been dealing with the parent company ships alone, had now to market their wares to the world and solicit business for themselves.
Over the years, competition in the Ship Management sector became more and more fierce, but a few companies held their own by virtue of quality of personnel, all trained in in-house institutions. Many of them became larger entities with a Management arm in Hong Kong, Singapore, Malaysia or India, a Recruiting arm in India and Philippines as also a Training arm in both the places.
The 1970s and 1980s saw the presence of mostly Indian Officers, who monopolised the staffing of ships and the Management positions. The end of the 1980s saw a demographic shift wherein more and more Filipinos were being selected as Junior Officers, with all the ratings and crew also from the Philippine Islands.
Unlike the Indian Government, the Philippines Government provided heavy support to their Seafarers and other Expatriates working in different countries. India could have had a monopoly in providing crew to world shipping if Government policies had been more liberal with emphasis on opening more institutions and training them. Those were the days when only the Government was allowed to run such institutions.
Even now, after liberalisation, there is hardly any consideration given to train more sea faring crew, whereas intake into Marine Institutes – Government and private – for Officers has gone up manifold, to an extent where the Graduates are not finding employment, even after spending about Rs 2 million. The Philippines, on the other hand, have expanded all facilities to the extent that the majority of seafarers in the world are from the Philippines today. India lost its chance in the 1980s to provide gainful employment to tens of thousands, after which they could have had a monopoly in the market even today.
Around 1983, Barber’s were in the open market to manage ships for any ship owner. Owners had come to realise that giving ships for management reduces their staffing and their headaches. Barber’s took up only the technical management of ships, the cargo part still being retained by the Owners.
Likewise, over the years, many of the larger ship owners found that it made sense to have their own Ship Management division, as it allowed them to not only get their ships managed by an independent arm of the Company, but also allowed them the opportunity to manage ships for other owners, at a fee.
The number of Ship Management Companies – for Technical Management and Crewing – has increased exponentially in the last 20 years, with many fly-by-night companies in the fray. Nowadays it is possible to find a lot of information on the net, which was not the case in the 70s, 80s and 90s.
(In 2016, even I was about to start a ship management company. Negotiations were on to acquire eleven ships for management from Bangalore. A rather large Ship Management company, already well established, entered the fray and, in one fell swoop, took it away from us. By the time we knew about it, it was a done deal.)
As can be seen from the logos below, Barber Ship Management / Wilhelmsen went through some crucial changes every once in a while, to keep pace with changing trends. They remain one of the top few companies in the world even today. I have sailed under all the logos shown below and also on ships belonging to other companies, who had given their ships to Barber’s for management.
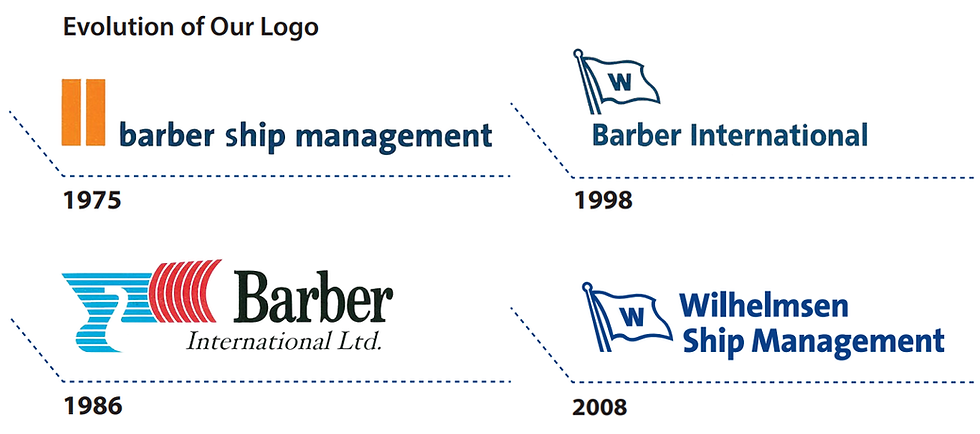
Courtesy Wilhelmsen Website
Chapter 2 – I join MV Theben at Kobe – A Short Tenure of only 45 days before I get transferred

Buildingyard: Eriksbergs Mek. Verkstad A/B., Gothenburg/ Sweden
Built year: 1953
Yard no: 440
Tonnage : GRT: 7010/ NET: 4120/ TDW: 8,421
Dims: LOA: 155,58/ BR: 19,87/ DR: 8,421mtr
Machinery: 10-cyl B&W by the shipbuilder - 9300bhp
Speed: 17,50 knots
Reefer space: 735,10 cbm / Passengers: 12
21.07.1953: Launched
24.09.1953: Delivered. Price: NOK18.852.466,43
03.03.1975: Transferred to Arctic Shipping Singapore Pte Ltd. (Torvan Shipping Ltd.), Singapore
00.00.1976: Manager: Barber Ship Management Ltd., Singapore
Before I left the Agent’s Office, I had to sign a One Year Employment Contract. After having spent much longer periods at sea in SISCO, a one year contract was like a vacation. Over the course of the next 31 years, this contract period would reduce to 10 months, then 9, 8, 7 and 6 months.
A flight from Mumbai took me to Osaka. The excellent thing about joining a ship in Japan is the Agent comes inside the airport, clears me quickly through Immigration and Customs and looks after me till I am on board. All done efficiently, even if passing through several hands.
I was finally taken by boat at Kobe Port out to where the ship was anchored. I had no idea of what type of ship or how old nor what run she was on – I had jumped into a deep well, without knowing how to swim and also blindfolded.
In actuality, I only knew how to float on my back in water, did not know how to swim. An oxymoron – how could a seafarer not know how to swim? But I went through 38 years at sea without it. My only precaution during all those years was that I trained myself to very quickly don warm clothes, and wear life jackets or immersion suits.
The launch was moving past many anchored ships in the evening twilight. As we came near each ship looking like a junk, I prayed silently this should not be the one. After crossing 3 or 4 such ships, the next junk loomed, one more prayer was added to the cosmos but to no avail.
I joined the MV Theben at Kobe, Japan, on 2nd April 1977. The ship, built in 1953, was nearly as old as I was – 24 years. No air conditioning, only fans and a blower in the cabin, that was the only negative aspect of the vessel.
But she proved to be a solid and sturdy ship, with solid decks, antiquated but good quality machinery on deck and in the Engine Room. After just a few days, I liked the ship. As 2nd Engineer, my responsibilities remained the same. I was totally at home in a new company’s ship. Officers and crew were all Indian, including the pantry staff, so the food was excellent. For a vegetarian, this is an important facet of shipboard life or else it could lead to bodily weakness.
The ship was registered in Singapore. It had a lot of cargo gear, mostly winches with derricks. It had – I think – 4 refrigerated chambers in one hold for carrying refrigerated cargo. It was a two island ship, with a midship accommodation for the Officers, a midship Engine Room and an aft poop deck or stern deck accommodation for the crew.
A midship engine room meant long shafting, a shaft tunnel and many shaft bearings that required proper lubrication at regular intervals. The Main Engine was, once again, a B&W VT2BF but with 10 cylinders, which model I was familiar with.
The run was from Japan to the Persian Gulf, with cargo stops at Hong Kong, Singapore with discharge being scheduled for 4 of the Persian Gulf ports. Being a General Cargo ship, she had holds with upper decks, ‘tween decks and lower holds, refrigerated cargo spaces, and palm oil tanks. The type of cargo loaded was known as ‘Break Bulk’. “The term BREAK BULK relates to trades where the cargoes are carried in unitised form such as palletised, bagged, strapped, bundled, drummed and crated and also non unitised general cargo (vehicles, steel etc).” (As defined in ‘shippingandfreightresource.com).
The loading of these types of cargo, naturally, takes time which gave us a minimum of 3 to 4 days at each port.
Being a ship whose structure and pipelines I was unfamiliar with, I was spending about 14 to 16 hours a day in the Engine Room. My logic was, if I had to spend one year on the ship, I may as well get to know the ship in minute detail, after which I can spend the first three or four months to complete all maintenance work, leaving us all free for just routine ones for the next nine months.
After about a week or so, apart from the Engine Room, I was spending at least 4 hours on deck to become more familiar with deck machinery. Being this busy, I have no recollection of the Japanese ports that we visited for cargo. I think it was Kobe, Nagoya and Yokohama, followed by Hong Kong and Singapore.
We were carrying various types of cargo to an area – the Persian Gulf countries – for the development of countries that were just coming to know about the standard of development in the Western world and wanted to catch up fast. They had all found oil in huge quantities to pay for that development. European and American companies had been contracted to hasten this transformation. Labour from the Indian subcontinent poured in to all the Gulf countries in hundreds of thousands. So the modernization of a region started, accelerating the process like in a time warp, straight from the 1800s to the late 20th century and beyond.
We were carrying cargo destined for building such an infrastructure. So were thousands of other vessels from all over the world. As the ports’ infrastructure was just then coming into existence, the Persian Gulf ports could accommodate only a few ships once in a few days. Understandably, there was chaos.
At that point of time, the Persian Gulf was the main driver of shipping economy and also the world.

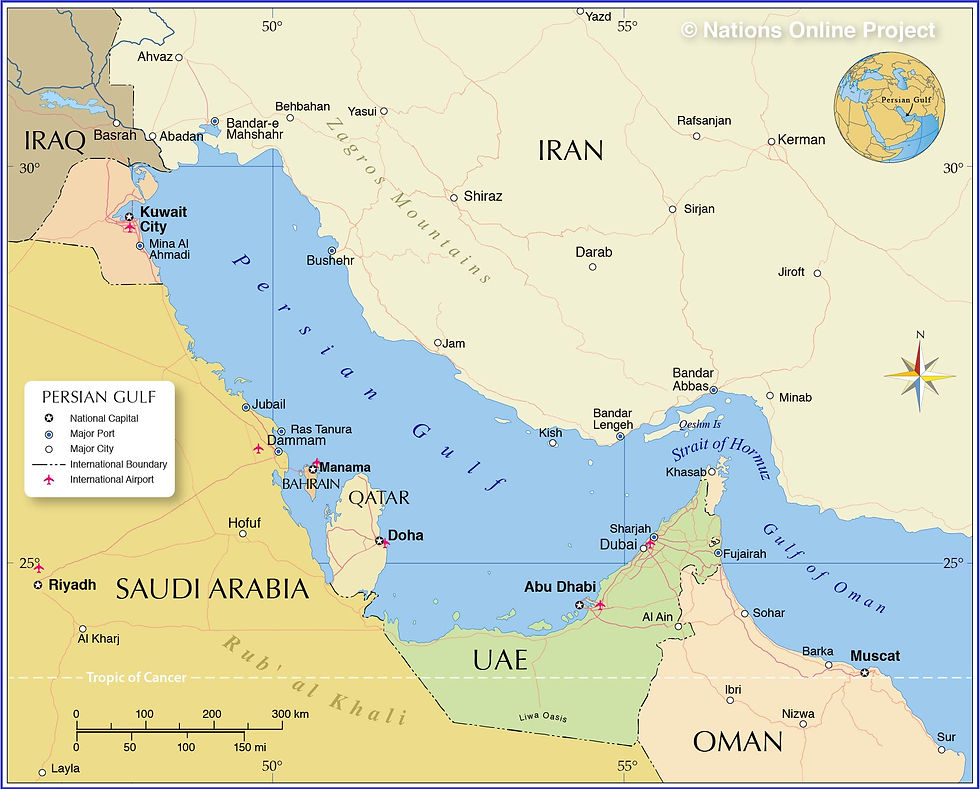
Courtesy Encyclopaedia Britannica - Major Ports in the Persian Gulf
We were scheduled to discharge cargo at Dubai, Dammam, Bahrain, Kuwait and Khoramshahr. The waiting time at each port was about 3 months after the ship registers its arrival in that port. Each ship would receive about 7 days notice prior berthing. Many ship’s Captains had resorted to a little bit of subterfuge in this registration business. They would anchor within Dubai’s anchorage area, report, register, get an acknowledgement and get an approximate date of berthing. They would then quietly lift anchor, go to the next port and do the same. Then the next.
They would then wait at anchor at the port that is likely to call them soonest. All the while a strict watch would be kept on the VHF and Radio, in case another port calls you to berth. There were risks involved but the gains were very good, as all cargo can be discharged within three to four months, instead of being stuck for 6 months if one followed strict protocol.
But there was a severe drawback. It was summer in the Persian Gulf. It was burning hot with nigh a breeze. The ship had no air conditioning and everything was hot to the touch. At least, when we were moving at sea, port holes could be kept open and, using wind deflectors made of galvanised sheets, direct some relatively cool breeze into the cabins. Now, at anchorage, the air was still and burning. We were forced to make changes to our working hours, so that we worked during the relatively cooler early mornings. Practically everybody was sleeping on the open decks.
After a day of this, I approached the Chief Engineer with the proposal to cool 2 of the cargo reefer chambers and use those chambers at night for sleeping, one for the Officers and one for the crew, with the duty staff keeping watch. We were not carrying any reefer cargo at that time. He jumped at the suggestion, but said the reefer plant had not been in operation for more than 1 year. I told him this is not only a good chance to try it out, but can also rectify any problems associated with the system and continue to keep 2 chambers cool for our purpose. I also suggested to him that we offset the increased power and diesel oil consumption by being more frugal. He jumped at the chance.
I spent the whole day, along with the other engineers, checking the reefer plant, getting it back into working order and putting it online for those 2 chambers. All the others pitched in to clean and wash the chambers, shift mattresses and pillows. The Electrician brought in plug points, reading lamps for people to read in bed. Only thing – you had to climb a ladder and go back to your cabins at the call of nature.
The next night and subsequent nights were spent in an environment of 24 degrees C instead of 45 degrees.. People played Bridge, Carroms, Scrabble and the like before sleeping. It had become one big dormitory for a family.
The Captain was an old Scindia hand, Capt Fernandes. The Chief Mate was ex SCI, who had served on the MV Chidambaram, a passenger ship plying between Madras and Singapore.
A jovial type, the Mate would tell me of his experiences on the MV Chidambaram. One incident that he narrated was the Chief Steward coming to him and telling him that food consumption by the passengers was way above normal and was not sustainable. The Chief Engineer would be brought into the picture and he would retract the ship’s stabilisers. The ship would roll gently and 70% of the passengers would get seasick and would not eat. There were also financial benefits.
Around 2 weeks later, we were asked to berth at Dammam, Saudi Arabia. A few minutes after we berthed, I was surprised to see a new joiner come and introduce himself as Second Engineer. Till then, I had been thinking I was the Second Engineer for the ship.
Meanwhile, unbeknownst to me, the Master and Chief Engineer had been asked by the Company to give a Confidential Report on me, as they had intentions of sending me as advance party for taking over a ship from the Norwegian parent company. I was highly recommended.
I did not know this till we berthed at Dammam. After berthing, the Captain called me to his cabin and, in the presence of the Chief Engineer, asked me if I were willing to go as advance party for another take over. I had become used to this ship, its environs and its personnel. But I thought of the transfer as a good opportunity, hence I said I was willing.
Next day, on 17th May 1977, I was signed off the Theben and flown to Abadan in Iran.
Later, I came to know that, in Bombay, a new entrant had baulked at taking over a ship from the Norwegians and, instead, had wanted a ship that was already under Barber Management. He was sent to the Theben and I was transferred to the ‘Trianon’.
This was the first of many such takeovers over the years.
---------- Rangan
===== Blog 45 continues =====
Comments