BLOG 39 - Thrust Block Burn Out and Subsequent Events - I Finally am Relieved and Sign Off
- ranganathanblog
- May 18, 2022
- 7 min read

The "Chennai Sadhanai" was my last Sisco ship. As such, I carry very fond and pleasant memories of that ship, even though a life threatening fire took place and a rare type of damage took place on the Main Engine.
Good people, good camaraderie and a hard working, happy crew. Throw in good weather (mostly), blue seas full of flying fish, dolphins, an occasional whale, the inspirational beauty of the variety of sun rises and sunsets, going past the Great Barrier Reef and, on occasion actually seeing the Reef in all its beauty - it was contentment for the soul.
Chapter 6 – Marine Musings 8 - A Calm and Routine Period – Then a Rare Type of Breakdown – Not Generally Seen
Time, at times, flew. At times, it weighed heavily on my hands. Technical books and Instruction Manuals became my companions, preparing for the forthcoming exams. Each sunrise and sunset was more beautiful than the one before. My mistress, the Sea, was in her myriad moods and I exulted in her arms. I was at peace with the Cosmos.
Then, one day, while on watch, I smelt burning oil. Following my nose, I noticed slight smoke coming out of the Michell Thrust Block.
I found a little bit of smoke issuing out of the Forward and Aft ends of the Michell Block shaft seals. I immediately reduced rpm and felt around the Thrust Block, but found no evidence of overheating.
I called the Chief Engineer down and showed him. On increasing the rpm, smoke was seen issuing out after a while.
We stopped. We were well away from land, so there were no extraneous dangers.
The small opening for taking clearances was not large enough for a visual inspection.
Unlike modern engines where the thrust block is encased inside the after part of the engine itself, this thrust block was located outside the engine. The principles of operation are the same. The method or path of lubrication is slightly different. On modern ships, oil gets continuously sprayed, through nozzles, on to the thrust pads and thrust face and drains down directly in to the Main Lubricating Oil Sump. On ships with the Thrust Block located outside the engine, the initial stage of lubrication is the same, through nozzles. The difference is in the draining of the oil after lubrication, where the drained oil collects in the bottom of the box-like Michell Thrust Block, after which a drain pipe leads the oil into the Main Lubricating Oil Sump.
The top cover was opened to check.
All ahead thrust pads were heavily scored, with all of the white metal missing as well as some of the metal of the thrust pad.. If the damage had been limited to only the thrust pads, we would have been fine as, then, it would have been only a matter of renewing the Pads.
The bad news was that the Forward side of the Thrust Collar on the shaft, which takes up the full thrust of the ship when the ship is moving ahead, was badly scored. This Thrust Collar, at the time of manufacture, is precisely machined and is machined to a smoothness that beats the softness of a baby’s bottom.
Even worse, the shaft had taken a permanent shift forward by 8 mm, which more or less corresponded to the 10 mm white metal bearing coating on the Thrust Pads that had been wiped out.
At this time, we checked all the Connecting Rod Bottom End sides, to ensure they were not rubbing against the webs. We were lucky. If the shaft had shifted another 4 mm, due to heavier damage to the Thrust Collar, we could have had rotating parts rubbing against the webs, causing extreme hot spots and a, likely, crankcase explosion.
A Thrust Block is designed to take up the axial forces transmitted by the Propeller and distribute it to frames in the Engine Room constructed for this purpose.
In yesteryears, the Thrust Block was a separate unit placed aft of the Main Engine and had a bypass feed of Lubricating oil for its lubrication. From the 1980s onwards, almost all designs had the Thrust Block within the Main Engine frame and as an integral part of the Engine, sharing the pressure of the Engine’s Lubricating Oil system.

Diagram of a typical and simplified Michell Thrust Block located outside the Main Engine – Thanks to You Tube and DG E Learning ADU Academy.
This is exactly what we had on the Chennai Sadhanai. Although it looks simple in the diagram, it is rather complicated. Removal and replacement of the thrust pads is difficult, requires skill and precision and an understanding of the working of the Thrust Block.
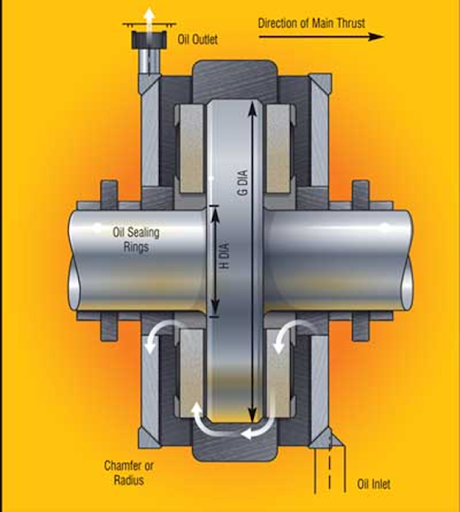
Nearly similar to what we had. Copied from ‘Machinery Lubrication’
By Heinz P. Bloch
The Ahead Pads were badly damaged. But we could not take them out as the shaft had shifted forward and had jammed the Thrust Pads. So we welded two steel supports on the tank top close to the intermediate shaft flange, fitted two hydraulic jacks and jacked the shaft aft. This loosened the jammed pads which were then removed.
To smoothen out the grooving on the Thrust face of the Thrust Collar, we used different grades of files to file the grooves, turning the shaft on turning gear simultaneously. After quite a while, we achieved a degree of smoothness which we thought would be sufficient.
Meanwhile, we found the cause of why the Thrust Block failed.
The Michell Thrust Block of those days had a sump at the bottom where the lubricating oil falls after doing its job of cooling and lubricating the Thrust Pads, Thrust Face. This Lubricating Oil that falls into the sump is drained by a drain pipe located about 50 mm above the bottom of the sump. So about 50 mm of oil always remains inside. Over a period of the last 9 years, this remaining oil had turned into sludge and partially choked the 60 mm drain pipe. The sludge slowly got splashed on to the pads and collar, causing fine particles to get lodged between the pads and the collar, resulting in grooving. The white metal of the pads, being the softest metal, sustained damage first, transmitted the damage little by little to the Thrust Face and slowly worsened. Once metal to metal contact occurred, smoke emanated from the block.
We used the spare Thrust Pads, fitted after a thorough cleaning of the bottom of the Block and flushing out with copious amounts of fresh lubricating oil. The pads were fitted, the block assembled and the jacks removed. We slowly increased the rpm and ran at “Full Ahead” rpm of 60 for nearly a day. But the new pads also got damaged, as we were not able to achieve the low ‘micron’ finish that was needed, with the rough tools that we had.
We were back to square one. The ‘Astern’ Pads and the ‘Astern’ Face of the Thrust Collar were undamaged.
So, we tried steaming astern. After six hours, we had made no progress.
The only alternative was a tow by a sea going tug. The Company arranged for one, which reached after a 3 day wait. A ‘messenger’ rope from a Line Throwing Apparatus shot accurately brought a thin line, then successive thicker varieties of ropes and finally two thick wire ropes, all handled by winches. After tying the wire ropes, the tow began.
I am not aware of what was the agreement for towing between our Company and the Towing Company. Sometimes a Lloyds Open Form is used.
We were towed at a steady 6 to 7 knots and finally made it to Japan.
A Japanese workshop came, dismantled the Thrust Block, machined the Thrust Face of the Collar using a tool holder that went round and round the shaft (in situ machining), fabricated a ring which was screwed on to one end to compensate for the 8 mm of machining done on the Collar (to obtain a smooth, low micron) finish and the axial shift of shaft, assembled everything and, after an Engine trial, left. All this took 3 days of continuous work.
A few weeks later, I signed off the vessel on 29th July 1975 at Wakayama after some protests regarding not being relieved.
A Shinkansen ride to Osaka, a flight via Singapore to Chennai and I was home.
I had been at sea on 4 ships totally for a period of 24 months, a long stretch by any stretch of imagination.
Chapter 7 – What did I learn on the Chennai Sadhanai? What were the takeaways?
The Captain and his wife were very good friends of mine, as I had known them for quite a few years. My friendship caused a bit of friction between the Chief Engineer and me, as I was his 2nd Engineer. The Chief Engineer also was a good friend of mine, so it took a while for him to see the broader picture, where professional conduct and friendship can be kept apart. I learnt to walk a tight rope.
One needs to apprise himself of the personality traits of each individual working under him, along with his professional prowess. Some become nervous under pressure, some panic in circumstances needing clear thought and action. The leader should be able to sift them out by studying them.
One needs to lead by example after earning their trust, after which others of courage will follow. To earn their trust, you should ensure that you think more about their safety, by which action you automatically ensure your own safety. The Motormen who fought the fire alongside the Chief Officer and me did so because they trusted me, trusted my leadership.
Muster Lists for Fire Stations are not realistic, as they do not take into account the phobias that people have. Duties are distributed by the rank held by that person. But he may be totally wrong for the job. Case in point was the 2nd Officer who was in charge of the Smoke Helmet and, during the fire, just panicked, threw everything down and ran away. It is a necessary duty of a Fire Chief to know his team, train them well and allot them their duties as per their strengths.
In retrospect, I realise that I did the most stupid thing an Engineer could do, when we were on tow after the Trust Block damage and the Main Engine had been shut down. Along with others, we did a lot of work inside the crankcase of the Main Engine, with the turning gear engaged. With the 7 knots speed that we were being towed, the propeller could have suddenly turned, the shaft could have rotated, smashed the tiny turning gear and rotated the crankshaft of the engine, thereby moving all the parts inside the crankcase. If not death, this movement of parts would have have maimed limbs, smashed bodies. We were lucky. It made me realise that I have to have a more holistic view in all aspects of Safety, within and without.
On joining a ship, try to find out what part of the machinery or which sector of the Engine Room has not been maintained for years and rectify the lack. You may be preventing a massive breakdown, like when we lost our Thrust Block.
Be at peace with yourself. This will allow you to make clear decisions.
Rangan
===== Marine Musings 9 to continue =====
Kommentare