BLOG 26 - MARINE MUSINGS 4 - A BREAKDOWN AND A DRY DOCKING
- ranganathanblog
- Apr 3, 2022
- 15 min read
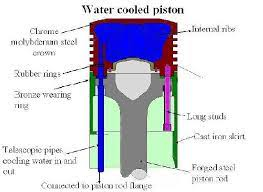
This narrative is more technical and engineering-oriented than normal. Non seafarers may not relish it, but I have tried to keep it as simple as possible by illustrations and drawings - not my own, all copied from the Internet God.
These days, because of very short tenures on board, not many seafarers would have entered a dry dock, nor seen what work is done when the vessel is on the 'blocks'. The subsequent chapter below covers a bit of my my first dry dock.
Subsequently, I was part of the process of dry docking many a ship that I sailed on. I found dry docking periods fascinating. It was the culmination of a year of planning, making specifications detailing each job to be done, ensuring requisitions for parts are sent out and also received on board, planning the allocation of personnel for each job, gathering and analysing reports submitted, meeting the shipyard staff every day to review progress - and much, much more.
I always claim that the seafarer is the only professional who gets complete job satisfaction in his work.
Chapter 11 - Major Breakdown at Sea
BREAKDOWN AT SEA:
One such stoppage occurred during this voyage due to a cracked Main Engine piston. This was actually a harbinger of a series of breakdowns that occurred a few months later.
As a 4th Engineer, one of my many duties was to ensure that the Fresh Water Expansion tank levels were maintained, analysing the water every week and keeping an eye on water loss per day. This Expansion Tank is located at a height well above the Main Engine and is part of the Fresh Water cooling system for Main Engine, Generators and, on most ships, Air Compressors.
We were at sea, on a long voyage, along with the monotony of routines that go with watch keeping during long sea passages. I noticed a couple of incongruities over a two day period. The water consumption had increased slightly, by about 30 litres per day – which may not sound like much for a system which is circulating 4000 litres. The second thing noted was that the water was not as clear as before and had a slightly blackish sediment floating on the surface of the water in the tank. I cleared off this sediment the first day. I checked for fresh water leaks on pipe lines, coolers, pump glands and found none.
On taking over the watch, approximately 24 hours later, I brought it to the attention of the 2nd Engineer and he apprised the Chief Engineer of what I had found thus far. To my surprise, they both took it seriously and started investigating. That they took me seriously was an indicator of their professionalism. More than a day passed and no faults had been unearthed. Meanwhile the water consumption had gone up by another twenty litres and the blackish residue on the water surface of the Expansion Tank had increased slightly, indicating that the fault is increasing.
In this engine (MAN K9Z 70/120 D), fresh water is used to cool the liner – by circulating the water between the jacket and liner, the flow path being from bottom to top – the cylinder head and also the piston.
Except for this type of engine, the pistons of all others that I worked on were cooled by oil, thus significantly reducing piston failures.
There were two other observations that I made on the running engine that I later realised were of utmost significance.
The first was one of the nine cylinder’s exhaust temperature was slowly but steadily dropping.
As a general rule, because the Main Engine is running at very nearly the same RPM day in and day out during the sea voyage, the Exhaust Temperatures do not vary much and, even if they do vary, will vary across the board in all cylinders, depending on wind or state of the sea. A significant drop of atmospheric temperature will cool the Engine Room due to 4 massive blowers taking suction of air from the atmosphere outside and sending it to the Engine Room, from which Turbochargers will take suction of this air and send it into the engine to aid in proper combustion in the cylinder. With ambient temperature dropping, all exhaust temperatures will drop.
But here we had a situation of only one cylinder temperature dropping. The fault needed to be localised and pin pointed to one source, otherwise we will all be running around like headless chickens.
The second observation seemed a slightly bizarre one. The piston cooling system was isolated from the other cooling systems, their commonality being that all the cooling systems used the same Expansion Tank. The other cooling systems had a flow that passed the water through static or stationary parts.
The water going to the piston had a more complex path, as it had to go through inlet and outlet pressurised chambers (called ‘dashpots’), telescopic pipes that reciprocated and moved the same vertical distance as the piston travel. It had to then travel through a bore in the piston rod and enter the piston crown. The construction of the piston was such that the piston cooling system water had to then reach the top most part of the inside of the crown on a continuous basis, without getting affected by the up and down movement of the piston. So, dashpots for the inlet and outlet to the piston, with compressed air at a constant pressure on top of the chamber of the dashpot needed to be supplied, to keep up a constant and steady flow over approximately 2 metre distance / height.
Some details of above can be seen at
This site talks about oil cooled pistons first and later water cooled pistons.
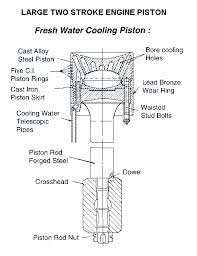
Copied from Besiktas marine.com

Copied from ‘ship’s machinery spaces’
On engines where the piston, cylinder liner and cylinder head are water cooled, it is difficult to pinpoint which of the three parts are cracked or damaged. The symptoms are exactly the same. But the subtle difference between a piston crown crack versus the liner or cylinder cover is by observing a small lever on the butterfly valve on the outlet side of the piston cooling water.
The outlet side of the pipe carrying the cooling water has a butterfly valve, the shaft of which has a small lever at the end of the shaft outside the pipe. Feeling this lever, one can make out the fluctuations in the flow of cooling water to the top of the piston, on the basis of which the air pressure to the dashpot can be adjusted. When I was a 5th Engineer keeping watch under 3rd Engineer Mr. Raman, he had taught me to 'hold and feel' this lever and to understand the very subtle differences at the fingertips. (He was one the unsung stalwarts I had mentioned before, who could not get past the 3rd Engineer stage).
My observation was that one of the units had a different ‘feel’ to the flow of piston cooling water. I had the habit of making thorough checks during the watch, my ‘feeling’ this lever on the butterfly valve being one of them. This habit came in handy in differentiating the ‘feel’.
I brought this also to the attention of my seniors. The combination of the lower exhaust temperature AND the erratic flow of piston cooling water (as described above) occurring on the same unit, helped in leading us to localising and pinpointing the location of the fault.
Upon their checking and finding that it was indeed so, we stopped the engine, put in the turning gear, opened the 'kidney shaped' scavenge ports’ inspection door provided on the fuel pump side of the engine and brought the piston down to Bottom Dead Centre. Through the port, we could see the top of the crown and water issuing from the crown, which should not have been happening.
We had to, then, remove the cylinder cover. By looking into the cylinder combustion space, we could see the top of the piston – there was a hole right in the middle of the dished crown.
We took out the damaged piston, used the spare piston and, within 7 hours, resumed our passage.
Later, when preparing for my Second Class Part 'B' exams, I came across a very scientific explanation for exactly the same damage in one of the two (books) of the Marine Engineer's Bible - John Lamb's "Questions and Answers on Marine Diesel Engines". Why I mention this specifically was that a very closely related question on piston crown failures came up during the examination, which I was able to answer with confidence, based on actual experience, bolstered by some research from 'John Lamb'. We experienced several such breakdowns later under extreme conditions, which multiplied my knowledge of such breakdowns. During the 'Orals' or viva voce' that one has to clear after the written examinations, I was particularly asked by the interviewing Surveyor about the confidence with which I had written the answers when others came up with haphazard answers. I had to explain in detail to a very interested Surveyor what I had gone through in actuality. I passed.
Coming back to the actual events, we went on to dismantle the damaged piston and changed the crown, using a spare crown. Now we had a complete spare piston, but no separate spare crowns.
This experience fine tuned our diagnostic abilities to the point where we knew that if observations a+b+c+d are noted, then the fault lies in ‘E’. If f+g+h … are observed, then the fault lies in ‘J’. It also honed our watch keeping abilities.
Requisitions were immediately sent out, asking for 2 spare new crowns, along with associated items. This was because piston calibrations of other units during the last two years revealed that significant wear and tear had taken place on piston surfaces, piston ring grooves and piston skirts. There was no guarantee that the other pistons would not break down. Requisitions for these parts were already pending for quite a while, but the Head Office had not supplied them. This act on the Company’s part would cost them dear, on which I will write in detail in the forthcoming pages.
After rectifying the breakdown, we proceeded on our voyage to Constanza. Winter time meant that the Indian Ocean and Atlantic Ocean were none too gentle. Since the cargo was iron ore, the Centre of Gravity of the ship was way down, which meant a ‘stiff’ ship, causing the rolling to be violent and jerky. Here I am being simplistic and have not mentioned ‘GM’ or ‘Metacentric Height’, which measure determines stability, as it would be cumbersome to explain in detail and would cross over into the realms of ‘Ship’s Stability Calculations’, which is a separate subject in itself.
Chapter 12 – Dry Docking at Malta
Another stopover at Constanza to discharge and, once again crossing the Bosphorus and Aegean Seas, we stopped at Malta in the Mediterranean Sea for the first dry docking of my career that paved the way for successful dry dockings in later years.
To my bemusement, in later years as a Second Engineer and a Chief Engineer, I found that most Engineers avoided the dry docking period of a ship, because of the extra work involved. From the beginning, I found it challenging and a highly focused learning experience, as it involved getting to know the outside and underwater portions of the ship more clearly.
I have a vague memory of having gone to Malta twice, once for drydocking the Chennai Perumai and, years later, once again to discharge cars on a Car Carrier. On the first, in the dock, we stayed for about 15 days and on the second occasion 3 hours.
The Chennai Perumai docking was in total contrast to dockings that I had done on other ships after joining Barber Ship Management, about 6 years later.
In today’s world, it is customary to treat the docking period as a much needed intense service period, to carry out jobs that otherwise would be difficult or dangerous at sea or in a port or to catch up on pending maintenance of major machinery or rectify faults which the ship staff have been unable to rectify, because of lack sophisticated equipment on board. Stays in port having been reduced to mere hours instead of days or weeks - as in the past - only urgent repairs or mandatory surveys are taken up by the ship’s staff. In most cases, shore workshop assistance is used to expedite the work.
In the 1970s, by regulations, all ships had to drydock every 5 years in order to continue to be ‘classed’ by a Classification society. The object is to inspect and examine all underwater parts – the hull, the rudder, the propeller, the various suctions and sometimes discharges.
The most important and most awaited clearances / readings immediately after the ship rests on the keel blocks in the dry dock are the Rudder Clearances and Propeller Drop measurements. If the trend of the readings indicate that they are unlikely to reach, at the present wear rate, their maximum limits over the next 5 years, they are left alone.
Otherwise, the rudder would have to be dismantled and the pintle bearings and housings renewed, if rudder clearances indicate abnormal wear. If Propeller ‘drop’ is excessive, it would mean removal of the tail shaft to check wear – and renew – stern tube bearings. These 2 jobs alone would extend the vessel’s stay in dry dock by a considerable period if unplanned. Stern tube bearings and rudder pintle bearings are not items one gets off the shelf and take around 3 to 6 months to manufacture. So, at least a year before the planned dry dock, these items are requisitioned and kept ready for use.

Typical Rudder and Propeller Arrangement
Copied from Marine Insight

Rudder Bearings and Pintles
Copied from Marine Insight
The hull is checked for sea growth and then washed with high pressure water. The shell plating is examined for loss of the specified thickness or pitted areas and thickness measured. If the plate has reduced in thickness by more than 10% of its original, that section is cut out and a new section is welded on. Any contact damage is examined from outside and inside, as supporting members may also have damage and may need renewal. The hull is then prepared for painting by ‘grit blasting’, washed again and paint coatings applied according to the paint manufacturer’s specifications.
Ship side valves are opened, overhauled and thoroughly inspected, as they have to last for another five years without failing. The ‘stub’ pipes that connect these valves to the ship side are welded to the ship’s hull and are sources of worry to the ship’s staff as, if they corrode and fail, flooding of the Engine Room is certain. In modern times, these ‘stub’ pipes are subjected to Ultrasonic Tests to find how sound they are. Before the 1990s, it was more by tapping the pipe with a small hammer - known colloquially as a 'Surveyor's Hammer' - and the thickness ascertained by the sound elicited.
The propeller, which weight may vary from 5 tons to 15 tons depending on the type and size of ship, is removed and seating faces between propeller and tail shaft, the cone, subjected to crack detection tests or ‘magna flux’ test and, finally, ‘bedded’ like one does for a white metal bearing.
Ships built from the 1960s onwards had force fed lubricated stern tubes. (A stern tube is the tubular structure in the aft portion of the ship that houses the shaft bearings.) The tail shaft is then inserted either from within the Engine Room (mostly so) or from the outside. Stern tube seals at the forward and aft portions of the stern tube seal off the lubricated shaft. The aft seal is designed to prevent ingress of sea water into the stern tube and also prevent leakage and loss of lubricating oil into the sea. The forward seal prevents the leakage of oil into the Engine Room.

Force fed Lubricated Stern Tube and Tail Shaft Arrangement

A 'Simples' Stern Tube Seal Assembly Section, which prevents sea water ingress AND Lubricating Oil Outflow
I was fascinated enough, at that time, with the stern tube and its arrangements that, at a later date, I did some thorough research into historical progression of stern tubes and seals.
Briefly:
Sailing ships of yesteryear needed no stern tubes, It was only after an engine was put inside a ship and, by means of a connecting shaft, was attached to a propeller, that the opening in the stern of the ship – that had to necessarily be cut into the after hull of the ship – needed to be sealed in some way to prevent sea water from entering the inside of a ship.

Arrangement showing propeller at one end, the stern tube seal, the stern tube, the tail shaft and the forward seal on the right.
The initial designs had stern tubes with strips of ‘Lignum Vitae’ along the length of the stern tube and around the circumference of the stern tube. These ‘Lignum Vitae’ strips acted as bearings for the tail shaft, within which the shaft would rotate. The aft end was kept partially open to the sea, sea water itself being the lubricating medium for the strips of ‘Lignum Vitae’. To prevent ingress of this water into the Engine room, a massive gland, with packings inserted, was employed.
“Lignum Vitae’ is a very hard type of wood having very good bearing properties. Although found in plenty, the growth of these trees were confined to the South American countries only, such as Venezuela and Argentina and was a cash cow for these countries.
Once worn, these ‘Lignum Vitae’ strips of wood proved to be cumbersome to renew and would entail delay to the ship’s schedule.
So, oil lubricated stern tube came into vogue and became a permanent fixture of a vessel’s construction from the mid 1950s. What delayed this from happening was that bearing metal technology was still in its infancy. The developments later made were instrumental in the oil cooled stern tube becoming the ascendent technology.
Hundreds of jobs get done in the dry dock, mostly by the shipyard staff. SISCO, having assigned very frugal budgets for the docking, cancelled many of the jobs that we wanted done. The ship’s staff carried out many of the cancelled jobs, but could not complete all of them.
Later breakdowns at sea could be attributed to this frugality, which would cost them dear. Penny wise, pound foolish. At that particular time, I was unable to see the larger picture due to my inexperience. Later years provided insights as to how everything could be handled, so that the ship has a trouble free run for the next five years.
We slogged it out. 16 hour days were common, with just enough energy left for a bath and dinner before hitting the sack.
The Company’s Operations Manager, Mr AT Joseph, had flown in to Malta to supervise the docking. Wonderful man. I mean, who would bring my Father’s letter and, having searched for me and found me working in the Engine Room, hand over the letter personally.
From the start, he liked me and I liked him. Although disparate in age, it was the start of a close friendship. I considered it a “Guru – Sishya” relationship. He considered it a close friendship. He was from the last batch of Engineering Cadets who passed out of the “TS Dufferin” and had a lot of stories to tell of his “Dufferin” days. After that year, the Navigational training remained on board the Dufferin, while the Engineering training was imparted in DMET Calcutta and Bombay.
One of the days, when in drydock, we were asked to quit work at 5 pm, in order to attend a party on board. given by Mr AT Joseph. A shave, shampoo and shower later, we wore the best civilian clothes we had and attended the party. Enjoyable atmosphere. A lot of chit chat took place, interspersed with work remaining in the dry dock.
Mr Joseph said something about hold bilges (I think) which I was certain was incorrect. Having spent more than 14 months on board, I knew every nook and corner of the vessel. When I disagreed and corrected him, it soon escalated into ‘I know this ship very well, young man. I took delivery of her from the shipyard’ from Mr Joseph to the Captain, Chief Engineer and Chief Officer siding with him, saying they were sure Mr Joseph was right and I was wrong. Mind you, I was a lowly 4th Engineer. My only support was the 2nd Engineer, Mr. Shankar, who stated that ‘If Chaar Saab (4th Engineer) says so, it must be right’. I refused to back down, being very sure of my knowledge. After some time, instead of waiting for the morrow to inspect the hold bilges, the top 4 decided to settle the matter then and there, but a bet of 2 Chivas Regal bottles was to be laid on the table which, for me, meant a whole month’s salary. I took the bet.
The hatch covers were opened, cargo cluster lights fixed and the bilge covers removed. Everybody went down into the hold and checked. What I had explained was found to be correct. This was appreciated by Mr Joseph who said that ‘Even though he is the most junior amongst us, he stuck to his guns when he thought he was right’. The two bottles of Chivas were, of course, consumed at the next party before the ship left Malta.

Malta - a small speck amongst Giants
Copied from worldatlas.cm
MALTA : For more than two centuries, the tiny island in the middle of the Mediterranean, south of Italy, was at the cross roads between Christianity and Islam. Christian Crusaders made this a stopping point before the jump to Jerusalem, to fight the Islamic warriors. Malta also supplied its own ‘The Knights of Malta’ into the fracas. Apart from that period of fame, it had been part of the Byzantium Empire and Ottoman Empire during their periods of dominance.
Churches and Cathedrals lend their history to Valetta, the capital, but are not very imposing. I had a day off from work and took in the sights of Malta. The most memorable was the boat ride to the Blue Grotto – a series of caverns at one end of the island’s cliffs – the water and cavern sides in each being a different colour due to a combination of sunlight, underwater growth and algae. It was a memorable sight.
Another interesting sight was the Harbour Entrance, being fortified with gun turrets to fire down on pirate ships trying to enter and loot the town. It painted a picture of medieval times.
After completion of dry docking at Malta and another bunkering of fuel at Augusta in Italy and we were off across the Atlantic to load grain in USA.
When we were in mid Atlantic, there was a death aboard, the Bosun dying of a heart attack. He just collapsed while at work, nothing strenuous, in front of his shipmates. As we had quite a long way to go, a sea burial took place and his body was consigned to the waters, with all due ceremony.
====== Blog 27 to continue with a 'ghostly' narrative =====
Okay, whoosh - that's the sound of much of the narrative flying over my head! Oh but the last part of the bosun's death is sad. I've only seen sea burials in movies. It must be quite depressing to lose a coworker so suddenly and not able to grieve properly. For the family left on land also!