BLOG 25 - MARINE MUSINGS 4 - Life as a Fourth Engineer
- ranganathanblog
- Mar 30, 2022
- 14 min read
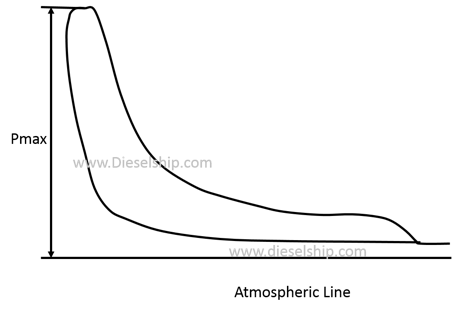
I have always found happiness in the humour in the late PG Wodehouse' books. The love affair with his books started when I was around 14 and continues to this day. I was a recent recipient of a mail where some of his humourous lines were repeated. At the cost of me receiving some acidic comments, I am sharing some of them with you.
"He had just about enough intelligence to open his mouth when he wanted to eat, but certainly no more."
― P.G. Wodehouse
"At the age of eleven or thereabouts women acquire a poise and an ability to handle difficult situations which a man, if he is lucky, manages to achieve somewhere in the later seventies."
― P.G. Wodehouse, Uneasy Money
"There are moments, Jeeves, when one asks oneself, 'Do trousers matter?'" - Bertie Wooster
"The mood will pass, sir." - Jeeves
― P.G. Wodehouse, The Code of the Woosters
"He had the look of one who had drunk the cup of life and found a dead beetle at the bottom."
― P.G. Wodehouse
"I could see that, if not actually disgruntled, he was far from being gruntled."
― P.G. Wodehouse, The Code of the Woosters
"She looked as if she had been poured into her clothes and had forgotten to say "when". "
― P.G. Wodehouse
"A melancholy-looking man, he had the appearance of one who has searched for the leak in life's gas-pipe with a lighted candle."
― P.G. Wodehouse, The Man Upstairs and Other Stories
Vintage PGW !!
One more :
It was a confusion of ideas between him and one of the lions he was hunting in Kenya that had caused A. B. Spottsworth to make the obituary column. He thought the lion was dead, and the lion thought it wasn't.
Ring for Jeeves (1953)
"And she has got brains enough for two, which is exact quantity the girl who marries you will need".
Chapter 10 – Now Promoted to rank of 4th Engineer, Routines and Problems at Sea, Preparing for 2nd Class Part ‘B’
My routine on board as 5th Engineer was different from the later ranks. I was given unsupervised jobs only after I had proven that I could do them well in front of the Second Engineer. The routine depended on which watch I kept.
4 ~ 8 and 1600 ~ 2000 watches with 2nd Engineer meant I got up at 0315H every morning (whilst at sea) and, after a quick freshening up, I would start taking my round of the Engine Room from 0345H or 1545H and reach the manoeuvring platform, where the Third Engineer would be waiting with the Engine Room Log Book filled in. The Second Engineer would also have arrived by then, and he would take over the watch from the Third Engineer and relieve him.
Ideally, they would discuss small problems that existed or had cropped up and remedies made. Any ongoing maintenance issues would also be discussed. I say ‘ideally’ because many a time, the Third Engineer would be too senior and a bit of friction would exist with the Second Engineer, hence an attitude of ‘I know this Engine Room as well, if not better, than the Second Engineer. So, is he trying to teach me?’.
I have seen the same attitude mirrored between Senior Second Engineers and Chief Engineers. To be fair, this was more the exception than the norm, about a 25% / 75% split.
At the back of my mind, I filed this aspect of behaviour of a few of my seniors and decided not to emulate them when I reached senior positions.
Unlike the more modern ships of my later years, practically all aspects of machinery operation were manually maintained. Engine temperatures and pressures fluctuated with varying sea water and Engine Room ambient temperatures. Since sea water – taken from the sea – was the primary cooling medium used practically everywhere, any drop or increase in temperature of sea water would result in Main Engine and Generator Fresh Water Cooling and Lubricating Oil and Air Temperatures going down or going up, which all had to be adjusted manually, at each cooler, by adjusting the feed flow out of cooler or bypassing the cooler. This needed to be done in order to maintain the prescribed parameters that the manufacturer had given.
The cooled Fresh Water is needed to be circulated in the engine to take away the heat of combustion. Typically, it was adjusted to enter the engine at around 45 to 50 degrees C and exit at 70 degrees C. Too high a temperature could result in an engine failure from seizure of parts, cracking of components. Too low a temperature would mean improper combustion in the cylinder and, due to increased thermal gradient, cause parts like liners, cylinder heads, pistons, engine jackets to crack. Over the years, due to various causes, I have had to deal with damage / holes / cracks in the various parts mentioned. I will deal with them later in the narrative, as and when they occurred.
The cooled Lubricating Oil is needed to be circulated inside the crankcase to lubricate all bearings – Cross Head bearings, Crank or Bottom End bearings and Main Bearings. Typically, it was adjusted to maintain an outlet temperature of around 55 degrees C. Too low Lubricating oil temperatures meant the viscosity of the oil would increase, pressures at pumps would increase and the shaft would find it harder to rotate with the increased viscosity. Too high a temperature meant overheating of the bearings, damage to bearings and a possible crankcase explosion. For Engine Room staff, the worst possible scenario would be to have a crankcase explosion, which could cause loss of lives and a severe fire. Luckily, I did not have this Crank Case Explosion to contend with during my 38 years’ period of service at sea. I think this was more due to the training I received in my first year of service and the training I imparted to my juniors and staff in later years.
The cooled Air is required in plenty by the Main Engine and Generators. The hotter the air, the higher the exhaust temperatures of the engines, leading to possible heat stresses of parts.
So, maintaining temperatures across the engine room is of primary importance.
Using sea water as a cooling medium meant that the sea water side of all coolers would get choked, the cast iron end covers’ division plates would get corroded, which meant pretty frequent cleaning and maintenance. So we became adept at machining zinc bars to the right sizes, to use these pieces as sacrificial anodes.
In later years, I came to sail on ships that used fresh water to cool the various components, thereby reducing corrosion drastically. During my DMET days, in 1969, I visited a Great Eastern ship that had the same technology. It depended on the Owners and their budgets.
As if this were not enough to keep one busy, various levels have to be maintained.
Fuel Oil and Diesel oil levels in their respective tanks have to be maintained, so that supply of fuel to the Main Engine and Generators is never interrupted. This meant starting the fuel oil transfer pump and, taking suction from a double bottom fuel oil tank, pumping oil into one of the two fuel oil settling tanks, watching the level so as not to overflow the tank and, on completion of the fill, slowly raise the temperature by opening steam and ensure a temperature of around 85 degrees C is maintained, so that the oil inside is ready for purification, when the other settling tank level reduces. In later years, all these operations were done automatically through the use of numerous sensors - all this being part of the requisites for certification as an 'Unmanned Machinery Space'.
Diesel Oil, being used for Generators, also receives the same treatment as above, except that there is no heating involved.
Fuel Oil and Diesel Oil Purifiers have to be operated and run, continuously for Fuel Oil and intermittently for Diesel Oil. For Fuel Oil, the ideal temperature at which separation and purification takes place is found by using a graph of viscosity and temperature and that temperature maintained correctly, or else the centrifugal purifier is likely to overflow. Water and solids are separated from the oil in the purifier. The solids stick to the outer periphery of the purifier bowl and need to be expelled once every four hours or so by a process known as ‘desludging’. This ‘desludging’ had to be done manually in the first phase of my sea career, before the advent of more and more automation in purifiers, which meant that staff were taking it for granted and were not able to foresee breakdowns. These purifiers also needed to be opened, cleaned and assembled on a scheduled maintenance cycle, based on running hours. This task of cleaning and maintaining the purifiers was part of a 4th Engineer’s routine.
So, as the 2nd Engineer’s assistant, after a month or so, I was given the routine tasks mentioned above. Initially, I was running up and down to carry out all these adjustments, look after levels, monitor pressures. Once I got the hang of it and I found that there was a cyclic simplicity to it, the jobs became simpler.
Three or four months down the line, I would find myself the lone engineer, along with a motorman, as the Second Engineer would come down later into the watch. Initially he would come down at 0500H, then it became 0600H and later 0730H, more to sign the log book and hand out the work to the day workers at 0800H.
I liked being in sole charge of the watch, grew more confident day by day and started enjoying the work. This enjoyment gave me the impetus to learn more and more, this learning process never stopping throughout my sea career. It was during this period that I made an oath to myself that I will learn at least one new thing about the ship every day and I kept that promise till my last sea going day 38 years later.
After watch, I would go up, have a bath, change, go for breakfast. By 0900H I would be down in the Engine Room with the 2nd Engineer, carrying out maintenance tasks on standby machinery or items that needed overhaul. Working alongside Mr RP Singh, I learnt a lot about the innards of all parts and machinery.1130H meant a beer and lunch and after a 2 hour rest / nap, it would be back to the Engine Room at 1545H, till 2000H, with a brief break for dinner at 1800H. Most of the days, I would be free after 2000H to rest or do what I like till 0345H next morning. So, this was the routine day after day - sometimes for 30 odd days at a stretch at sea and in order to prevent this routine from becoming monotonous, it was necessary to keep up an unflagging interest in knowing things in greater depth than already known.
If there were breakdowns and stopping of the Main Engine at sea, it would mean working around the clock till the problem is fixed.
For a brief period, as 5th Engineer, I was assigned to the 3rd Engineer’s watch, so kept what was known as the ‘Graveyard Watch’ from 0000H to 0400H. Apart from, maybe, 5 persons, the whole ship would be sleeping. So, with the 12~4 watch, sleep patterns became different and one needed to adjust accordingly.
Our crossing time zones, would create havoc with our biological clocks. The fastr ships of later years were the worst - mpre on that subject later.
After 11 months, I was promoted, but continued carrying out the duties of a Fifth Engineer, till new Fifth Engineers were assigned to the ship. My wages more than doubled.
then, put When I rejoined the ship in Goa, in December 1971, I was delighted to find that 2 new Fifth Engineers had joined the ship, I was, then, put in sole charge of the 8-12 watch and no longer had to keep nights in port.
The additional responsibility was that I had 'shipkeeping' duties every alternate day n port and could be called / woken up anytime in case of a problem.
As a Fourth Engineer, I was now in charge of maintenance of the diesel engines attached to the alternators, colloquially known as Generators. These engines had a running hour based maintenance cycle. For example, we had to
Every 250 hrs Clean lub oil and fuel oil filters
Every 500 hrs Check tappets and inspect crankcase
Every 1000 hours Change fuel injectors
Every 3000 hours Overhaul cylinder heads, check crank web deflections
Every 6000 hours Overhaul all pistons, starting systems, governors, inspect a few of the main bearings and a lot of other related work that would normally involve most of the staff for nearly 4 to 5 days.
Purifiers were also my responsibility.
Having the responsibility of certain machinery, I put in a lot of effort – academically and technically – to know the ins and outs of the machinery under my responsibility by studying the Instruction Manuals thoroughly and comparing and checking the particular machinery concerned.
For example, Purifiers are complicated pieces of machinery. The only easy part is its cleaning. Going for a complete overhaul of the vertical and horizontal shafts requires attention to detail. The ‘Alfa Laval Purifiers’ that we had on board the SISCO ships had excellent and well elaborated Instruction Manuals and Drawings. Running at close to 3000 revolutions (RPM), mistakes cannot be made in assembly or else the high centrifugal forces can destroy the whole purifier in a minute. How temperature affects the purification of a fuel oil at various densities, how gravity discs affect purification, how speed of the purifier affects the process, what is the flow path of the fuel oil from the time it enters the purifier till it discharges itself out of the purifier, the importance of ‘flow rate’. Its adjustment and effect and hundreds of small, seemingly trivial, but plays an unseen, major part in the process, details were to be found in the Alfa Laval manuals. I learnt a lot.
Since then, I became a student and lover of Alfa Laval Purifiers and kept up with their updated models and technological / design changes over the years, till I left sea life. It was a fascinating subject, which evolved from my 4th Engineer days. Knowing such machinery intricately made problem solving easier and I was able to pinpoint the defective parts, rather than open up everything and check.

The innards of a Purifier, showing how the oil (dark brown) first flows down the centre and is then forced upwards and outward by the centrifugal force created by rotating at around 3000 revolutions, passes between the separating discs (light brown in colour). When the oil is in between the dics, solid particles in the oil is flung out towards the periphery due to the high centrifugal forces. So are the water particles. The purified oil (shown in yellow) then exits the purifier. This is the simplified version - it is actually much more complicated, due to the involvement of various other factors.
Over the next 12 months, I was able to bring the same concentration to other important pieces of machinery, as a prelude to advancement of my technical knowledge and also keeping in mind my preparation for II Class Part ‘B’ exam, the passing of which would qualify me for the rank of 2nd Engineer.
In the meanwhile, the Chief Engineer and Second Engineer had changed on the ship. Mr Rajagopal, 8 years senior to me in College, had joined as Chief Engineer. A suave, articulate person, he was a brilliant engineer.
I had started preparing for my 2nd Class Part ‘B’ exams in earnest, by studying the manuals on board and taking copious notes. In fact, by the time I left the ship a year later, I had accumulated over 2400 foolscap pages of notes.
Many Engineering books were also available in the Chief Engineer’s Office, courtesy the Company, as they anticipated and expected junior engineers or deck officers to prepare for the examinations that led to higher rank, during their free time on board. I took full advantage of the material available. What I could not follow or understand, I asked the Chief Engineer questions and received either a detailed reply or a reply stating he would find out and let me know.
Mr Rajagopal had the habit of coming down every night after an evening card (bridge) session, while at sea, at around 2100H, to have a cup of coffee with me – even then I made a good cup of coffee – and talk to me. Since I found that he was coming regularly to the Engine Room, I used to prepare questions for him from among the doubts I had. Seeing my deep interest, he also used to ask me questions, for which I would reply or find out the right answers. It became a challenge of minds for both of us.
Another important change in staff was Mr Shankar joining as 2nd Engineer. He was five years senior to me in College. Extremely talented, resourceful and intelligent, he had no qualms in opening up and dismantling spare machinery parts, just so that I can learn. Such was his confidence in himself.
From the studying of Instruction manuals, I had to necessarily progress to dismantling and seeing the various parts involved, to see what makes them tick and do what they do, when in service. Initially, I concentrated on the engine parts that had a short maintenance schedule, most of which I had, by then, overhauled. With small sketches in my notes, I elaborated on the working, diagnosing any problems and finding solutions.
Mr Shankar and I then started working together. He started coming down during my watch and I used to be down anyway during his watch. This provided us the opportunity of dismantling and overhauling Main Engine parts that are only occasionally done, like cylinder heads, pistons, fuel pumps, starting air distributors, Main Starting valve and the like. Study the manual, go down to the Engine Room, open and dismantle the part, inspect, clean and overhaul, record calibrations, renew O-Rings, observe, take notes, make a small sketch, assemble, pressure test and keep ready for service – that was the mantra practically on a daily basis. All Generators and Purifiers, Pumps and Compressors, Boilers, coolers, heaters were subjected to the same in-depth scrutiny.
It was during this period that I dismantled and closely saw a Marine Bosch Fuel Pump. I was fascinated with what happens within the fuel pump, how suction of fuel takes place, how the fuel is pressurised to around 800 kg/cm2 within a stroke of around 35 mm and how fuel is regulated to give a measured quantity of fuel at each stroke, 129 odd times a minute, for over 30 days - if need be - to maintain a certain RPM of the engine.
This led to further research on cams, studying of cam profiles, adjustment of cams. This led to learning about advanced injection of fuel and retarded injection and the effect of this on the engine, the engine’s output, how cylinder pressures and exhaust temperatures vary because of advanced or retarded injection, how to adjust theām for optimum performance.
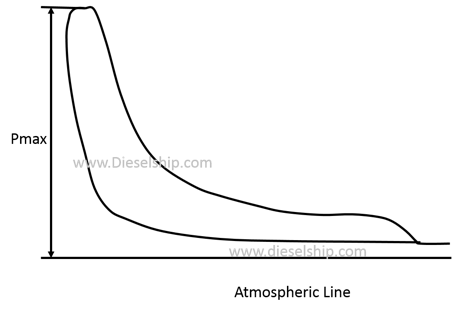

This, again, led to Indicator cards, how to take them, how to calculate various horse powers, when injection and combustion starts, peak pressures, whether sufficient air is being supplied to the cylinders, leading to knowing of the condition of piston rings, scavenge valves and associated equipment. Learning of one item led to a maze of others, all inter connected. So, within a few months, I came to understand the overall picture and how one affects the other and how to go to the root cause and find a solution. This diagnostic ability stood me in very good stead in later years.
It was a time of intense learning, which kept away the loneliness of sea life and the time was spent in a very profitable manner.
Thus, the voyage out of Goa to Constanza was a very busy one. It also had its share of some small breakdowns AND a major one.
Unlike a car or a train, on which the engine can be stopped almost instantaneously or the brakes can be applied, it takes time for a Marine Engine to stop – unless it is an emergency. This is because the revolutions need to be brought down slowly to avoid build up of thermal stresses, as the sudden cooling of the engine can cause running parts to crack due to thermal stresses. At least 20 to 30 minutes are necessary to slow down and stop.
Unlike cars or trains, the ship being in water, has a momentum of its own and takes quite a while for the ship to stop, even though the Main Engine has stopped. Paradoxically, even though the fuel supply to the Main Engine has been stopped, the engine will continue rotating for a few more minutes and, the Main Engine being directly attached to the Propeller by means of shafts, the Propeller will also continue turning. What will make it eventually stop will be the resistance to the propeller in the water, the friction of the various bearings, other running parts and the shaft alignment.
The better the alignment of shafts and the lesser the friction from various parts, the longer it will take for the engine to come to a complete stop. If the shaft were to come to a stop very quickly, it could be indicative of alignment problems or excessive friction from running parts.
===== Blog 26 continues - narrative of a major breakdown at sea =====
The details are interesting! Who knew so many intricate operations take place in a ship! We only get to enjoy a smooth sail. PGW is also my favorite humorist/author.