Blog 108 == One of Several Pet Projects of Mine Starting from my Second Engineer Days.
- ranganathanblog
- Jan 15, 2023
- 7 min read
“ Marine Musings 36” - My Research
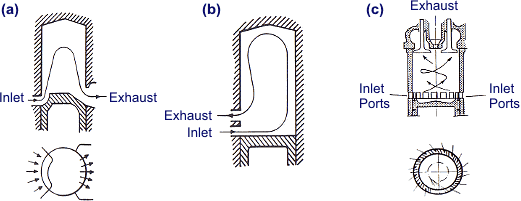
Before I begin this narrative, I would like to wish all a very Happy Pongal.
The 14th and 15th of January is celebrated all over India by various names.
In Tamil Nadu it is "Pongal". The Harvest is in. The house has been cleaned and painted. In the old days the 'paint' used to be limestone and chalk. New clothes for all, including the field labour. The livestock are all washed down. The bullock and the plough are venerated (pre tractor days). These days the tractors are washed and painted. There is an air of gaiety all over. The traditional folk dances, "Kollaattam" (akin to the 'Dandiya' in the Northern states) add colour to the festivities.
The main dish of the day is "Pongal", a sweet dish of rice, jaggery, cardamom, cashewnuts, ghee etc, which is allowed to boil and froth over the side of the clay pot - the word 'Pongal' meaning 'boiling over' - at an auspicious time on the 15th of January. The 'boiling over' of the cooked dish represents the bounty of the harvest, signifying an excess, even when it is meagre.
On the Tamil calendar, a lunar based one, the month of "Thi" (pronounced as 'thigh') begins. In old folklore, there is a saying "Thi pirandhaal vazhi pirakkum", meaning "when the month of 'thi' is born, one will see the way, the path." Most farmers would have availed of loans from various sources for seeds, fertilisers, planting, irrigating and harvesting. The belief is that , after the harvest is in, all the loans can be paid back and the surplus sufficient for all their aspirations.
In my childhood years, I spent a lot of time with my maternal Grandfather, a farmer. Instinctively, I came to understand the harmony, the closeness, the bond, the respect, the veneration that the farmer had with the Earth. Simple lives, no complexities.
In Kerala this day is known as "Makaravilakku" and is synonymous with the lighting of a lamp in the hills of Sabarimala, celebrating an ancient event written up in the 'Ramayana'. It also signifies the culmination of harvesting.
In Karnataka it is celebrated as "Suggi" or 'MakarSankaranthi', the latter being used in Maharashtra - all to do with the bringing in of the harvest.
Prior joining DMET at the age of 17, my travels had been limited to the interior of Tamil Nadu and a year in Secunderabad. In Marine Engineering College, Calcutta, my vista expanded as we celebrated all the festivals of all the states of India.
14th January is one such, with the festival of Lohri being celebrated, one that is celebrated by most residents of the states in North West India, signifying the end of winter. Bonfires, bhangra and boisterousness - I loved every moment of it.
I extend my greetings to all on the occasion of the 15th and 14th of January.
Dew Point, Relative Humidity and Main Engine Air Inlet Temperatures - The Emergence of a Symbiotic Relationship if Closely Monitored and Controlled
The below narrative / findings have been one of several pet projects of mine from my Second Engineer days. One could call it an extended 34 year (private) study of the whys, whens and wherefores of a singular phenomenon - why do piston rings break very often on some engines and why do liners wear excessively on some engines? What can I, as Second Engineer or Chief Engineer, do to improve conditions, alleviate the problem? Can I get to the root of the problem?
So started, from 1973, a venture that has taken me into the scavenge spaces countless times of a vast array of Main Engines to inspect pistons, their rings, the deposit behind the rings (to the extent visible), the condition of the rings, the liner lubrication, the percentage of choking of scavenge ports on loop scavenged engines, the checks on fuel injectors to find probable cause etc.
At every decarbonisation, I would find myself observing each detail closely - how much of residue is accumulated on top of the liner (which needs to be cleaned and removed before lifting a piston), what is its composition (roughly), how many rings are stuck or broken, how much of deposit behind the rings in the grooves, how does it compare to what I had surmised through a scavenge space inspection, how had the unit performed during operation and a myriad of other observations.
Over a period of years, with a lot of practical observations and studying articles written by experts in the field, I was able to list some of the factors that caused piston rings to deteriorate and liners to wear faster than the norm.
Below, I am taking up one of the factors, an ingredient that has a decisive effect on rings and liners.
One of the very serious repercussions of uncontrolled quality / temperature of air into the Main Engine, is the steady build up of thick sludge like compounds behind piston rings, which inhibits the expansion and contraction of the piston rings in the cylinder, causing them to either break or get stuck. Thus, they become ineffective.

Stuck piston rings
Broken or stuck piston rings mean that, as the rings are not performing their jobs, a series of cumulatively deteriorating events take place in the particular cylinder of the Main Engine.
The Compression Pressure inside the cylinder drops sharply, as the piston rings are not sealing the combustion spaces well enough, causing pressure built up during combustion to leak past the rings.
As Compression Pressure drops, the ignition temperature of the injected fuel oil may not have been reached. Although the fuel may be nearly atomised and injected, all the micro droplets may not get ignited. Incomplete combustion results. If this condition is allowed to deteriorate, the exhaust gas blackens, combustion pressure fluctuations take place between cylinders, the engine rpm fluctuates and the turbochargers start surging.
Another consequence is the leakage of hot exhaust gases past the rings, causing what is termed a ‘blowpast’, causing a scavenge fire. The accumulated oil and sludge in the under piston spaces start burning. If this is not immediately brought under control, the ‘scavenge fire’ can spread to other under piston spaces.
To control this before it spreads, the engine rpm is brought down, the fuel for that particular unit is cut off and the cylinder lubrication is increased (to offset the dryness of the cylinder liner, as the scavenge fire would have burnt the light coating of oil).
It is better to rectify this condition before proceeding.
So where does air quality come in to minimise or prevent the above conditions from prevailing?
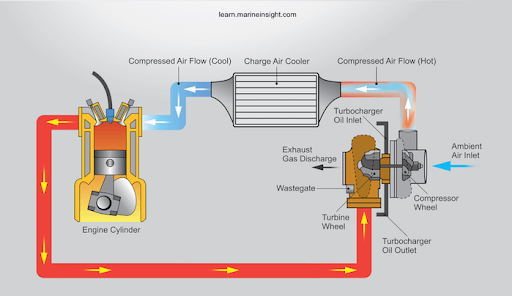
Basics

Uniflow Scavenging

The left and centre images apply for 2 stroke engines
A quick look at the step by step change in air parameters:
Engine Room air at an average temperature of 45 degrees C. Humidity is dependent on what it is outside the ship on that day, mostly high humidity. Is sucked in by the turbocharger air side compressor.
Engine Room Air – Sucked in by the Turbocharger Air Side Compressor - Average 45 Degrees C - Mostly High Humidity - Slightly above atmospheric pressure of 1.01325 bar.
In Turbocharger Air Side Compressor - Pressure increases to around 1.6 to 2.2 bar - Temperature increases to around 100 to 120 deg C - velocity has increased tremendously - flows to the Air Cooler.

A New Air Cooler - Air Side is Red Coloured (Fins)
Air Flows Top to Bottom
Flanges on the Left are for Cooling Water (Tubes)
Cooling Water Flows
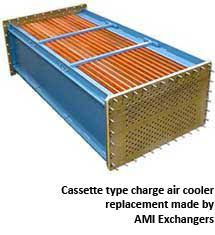
Image (forefront) shows the tubes through which cooling water flows

An Air Cooler After a Few Years of Use -
Note Deterioration of Fins due to uncontrolled Water Vapour.
Fins of Aluminium or Copper Finally Turn to Powder at the touch of a finger, if Not Looked After or Badly Maintained
In the Air Cooler - Cooling Water flow through tubes - In old ships sea water is the cooling medium - in most ships built after 2000, fresh water is the cooling medium - maybe a single pass cooler but, mostly, double pass coolers. Some ships have four pass coolers.
Assuming a two pass horizontal, finned cooler, the cooling water enters the bottom half of the air cooler, cools the air surrounding those tubes, reaches the other end of the air cooler, reaches the top half section of the tubes, changes direction and flows backwards to the outlet connection.
After changing direction, the cooling water - which has increased in temperature - flows through the top bank of tubes, which are surrounded by the hot air (100 to 120 deg C).
The top bank of the air cooler is cooled by the slightly heated up cooling water, flowing at a lesser velocity and pressure (which is lost in its transit through the bottom half of the cooler, filling the back cover of the cooler and reversing direction to flow through the top tube bank). The lesser velocity of the water allows more heat to be absorbed from the hot air surrounding the tubes. By the time this hot air reaches mid way of the air cooler, it has dropped from 120 deg C to around 60 deg C.
The bottom bank of the air cooler now contains air that has cooled to around 60 deg C, being cooled by the colder water (assume to be 28 deg C), which has just entered the air cooler. If effective cooling has taken place, the outlet temperature of air will be around 35 deg C.
This outlet temperature can be controlled to maintain any temperature above 35 deg C, by throttling the outlet valve enough to give the desired temperature.
Water flows through the tubes and absorbs the heat from the air that surrounds the cooling tubes.
Hot, pressurised air is now flowing between the fins that surround the cooling tubes. These fins absorb the heat and transmit it to the water in the cooling tubes.
The hot and humid air at a (relatively) high pressure passes through the Air Cooler and cools to (between) about 35 degrees C to 55 degrees C, depending on the cooling water valve settings that can regulate the temperatures. The pressure drops slightly (because of passing through a rather large seized air cooler. The velocity also drops slightly for the same reason.
The cooled air enters the scavenge space, which is constantly at around 2 bar pressure.
But the humidity in the air fluctuates wildly throughout if unregulated, being totally dependent on the air temperature achieved by the cooling water valves’ settings.
Something known as “Dew Point” becomes very important from this point on.
Two definitions of “Dew Point”:
“The temperature at which air can hold no more water vapour. Below this temperature the water comes out of the air in the form of drops.”
“The dew point is the temperature the air needs to be cooled to (at constant pressure) in order to achieve a relative humidity (RH) of 100%. At this point the air cannot hold more water in the gas form.”
What does ‘Dew Point’ have to do with scavenge air being sent into the engine?
If the temperature of air is at or below the ‘dew point’, there is a high possibility of a heavy concentration of water droplets, in the form of anything between micro droplets to larger sized droplets, being carried over into the Main Engine.
===== Same Topic Continues in Blog 109 =====
Comments