Blog 106 == A Covey of Car Carriers - Two Aspects of Their Vulnerabilities
- ranganathanblog
- Jan 8, 2023
- 9 min read
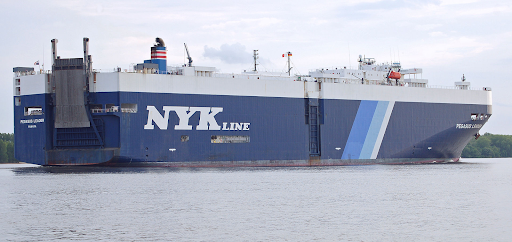
“Marine Musings 35” - A Covey of Car Carriers - My Last Hurrah to the Sea
“Pegasus Leader”
26th Oct 2006 - Yokaiichi
To
02nd March 2007 - Nagoya
9181560
1x Mitsubishi 60LS - 2 stroke single acting 8 cylinder 600 x 2200 mm diesel engine - 14.121 kW at 100,0 rpm
Manufacturer: Kobe Diesel Co., Ltd. Nagasaki Works

“Alioth Leader”
05th Sept 2007 - Mizushima
To
24th February 2008 - Zeebrugge
9166895
6UEC50LS
18750 KW
MITSUBISHI HEAVY INDUSTRIES LTD - KOBE, JAPAN
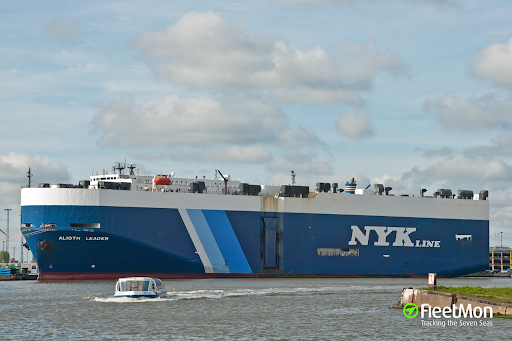
9166895
“Polaris Ace”
20th May 2008 - Durban
To
21st June 2008 - Zamate, Argentina
9153549
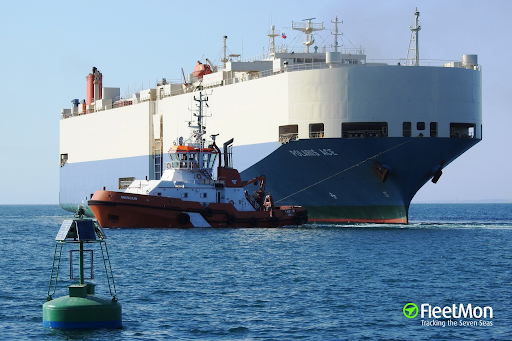
Car Carriers are a different breed, of an exotic class.
Rather frightening at first sight due to its monstrous size, but as meek as a lamb when it comes to carrying its cargo, due to its precise, predetermined, pathways and structured separation schemes. The only aspect that is missing are traffic lights and flyovers, which will probably get introduced soon enough.
When looked at from outside, they seem like massive coloured bath tubs on the move, brightly painted.
The Bridge right in front.
The funnel is not on the longitudinal centre like conventional ships.
Older car carriers, it was on the starboard extreme. The newer car carriers, the funnel is on the port extreme.
Reason? 99% of the time, vessel goes starboard side alongside and soot from the funnel is likely to fall on the thousands of cars on the quay, waiting to be loaded.
The reason for the vessel to go starboard side alongside? The massive stern ramp - 200 to 300 ton weight - is designed to be lowered to the starboard side, diminishing its saleability.
All accommodation is mostly on one single deck, with the forward portion raised to two levels for locating the Bridge, nearly overlooking the bow and foc’sle.
The seafarer on the top deck is living with 10 to 12 decks, each the size of football fields, under him.
On conventional ships, when conning the ship, you look at the bow forward to see the effect of the turn.
On a Car Carrier, you look astern to see how the stern is behaving.
On a conventional ship, when an engine movement is given, you can hear the engine start, feel the vibration almost immediately and - if looking at the funnel which is in close proximity to the Bridge - can see the puff of smoke.
On a Car Carrier, when an engine movement is given, the only evidence of an engine starting or running is from the Bridge tachometers, the puff of smoke sometimes not visible due to the funnel being 150 to 200 metres away. Vibrations are hardly felt when an ‘ahead’ movement is given. Delayed vibrations are felt on the Bridge - delayed by as much as two minutes - when an ‘astern’ movement is given.
Although the vibrations and noise from operating a bow thruster is the same on both types of ships, it is acutely felt on the car carrier, as the thruster is almost vertically below the Bridge.
Bridge perception to conning the car carrier has to change drastically.
Positioning of a car carrier at a berth has to be exact and accurate to within inches, as the stern ramp - when lowered - should land exactly in the space between two bollards, and not come to rest on any of them. The stern ramp is likely to twist and be subjected to a torsional stress if landed on the bollard. If this happens, then it cannot be housed properly.
For an engineer, UMS night duty can be problematical if he has to attend to an alarm in the Engine Room. It may take him as long as 3 minutes to reach the Engine Control Room to attend to any alarm, as he has to cover nearly a full ship’s length, either on open area of the top deck, or go through the car hold, where a narrow lane has been marked out, the rest occupied by cars. Then, at the end of this walk, an elevator awaits, to carry him down to the Engine Control Room.
If out on the open deck at night, it could be pitch black. Sometimes, high winds, bad weather can delay his reaching the Engine Control Room.
The timer for non-acknowledgement of any alarm is set, normally, at 3 minutes, after which it triggers the alarm in all Engineers’ cabins and common spaces. So it comes to pass that everybody is woken up at night at least twice a month. One cannot blame the Duty Engineer. He may have just taken that one minute longer to reach the Engine Control Room.
On conventional ships, the Duty Engineer’s cabin is in the accommodation (almost) above the Engine Room, so he has easy and quick access to the Engine Control Room.
On a Car Carrier, arguably the most important piece of equipment is the stern ramp, as millions of dollars flow past it in every port, in a never ending stream. The common cars of the world, the more exotic ones, the flashy ones, the royal ones - all flow through the same stern ramp, without distinction.
It - the stern ramp - is also very vulnerable to damage from mishandling, either from lack of expertise or from lack of communication with others who are involved in the lowering and raising of the stern ramp.
Once carried out a few times, a sense of complacency sets in, ultimately leading to a careless approach leading, subsequently, to damage and long delays.
The Bridge, egged on by an impatient Harbour Pilot, can also hinder smooth operations by insisting on a ‘hurry up, hurry up’ approach.
All it takes is one mistake for the ship to be stuck in that port for days, as the 200 ton stern ramp is incapable of being picked up.
On conventional ships, as Chief Engineer, I would stay in the Engine Room - during arrival port - till ‘Finished with Engines’ is given and leisurely make my way up after nearly an hour.
On Self Unloaders, I had to necessarily let the Second Engineer carry out the final functions of an “Arrival Port” routine, leaving the Engine Room much before ‘Finished with Engines’ was given, in order to supervise the starting of the Self Unloader plant and keep the plant and personnel ready for discharge of cargo.
On Car Carriers, due to the vulnerability of the stern ramp operation, along with the Electrical Officer and the Fitter, I would place myself in the hands of the Chief Officer in the lowering and positioning of the Stern Ramp, act as an Observer and quietly warn him - on the W/T - of any impending mishap.
On my first Car Carrier, the ‘Nosac Taishan’, (in 1985) I had realised how short staffed the Chief Officer was for the operation of the Stern Ramp, so I always had made it a point to help.
Reading and hearing about the quick sinking of various ferries, some due to the bow ramps not being properly closed, induced me to pay close attention when the stern ramp was picked up, housed, locked, secured. On a few occasions, I have alerted the Mate and Master that the locks were not fitting in place and, consequently, delayed the ship till all locks were in place.
Vulnerable when there is Water Ingress
Ever since my first Car Carrier in 1985, I had always been apprehensive of the potential for disaster that can be caused by a ramp that gets damaged and is, hence, not capable of being ‘housed in’ properly, leading to inadequate seals for watertightness.
The freeboard of a Car Carrier is low. If water were to enter through a leaking stern ramp - or any side ramp, for that matter - due to the ‘squat’ effect or a following sea, the water will definitely spread across a vast area of the Main Continuous Deck, which is - in most cases - # 7 Deck, the main entry and exit point of all cargo.
The ‘Free Surface Effect’ of a partially flooded compartment of a Car Carrier has always worried me.
Let us assume a vessel size of 160 metres L x 30 metres Beam.
For a 7 holds’ Bulk Carrier, in the event of a hold flooding, the surface area in one hold is a maximum of 20 x 25 = 500 metres square which will have an influence on the ‘free surface effect’.
For a Car Carrier, the same does not hold true.
The uppermost continuous weatherdeck that is supposed to be watertight is - on most Car Carriers - # 7 Deck. Depending on the size of the car carrier, there are one or two gas tight and watertight hydraulic ramps that seal off all the spaces below # 7 deck.
Below # 7 Deck, 3 or 4 further watertight sub divisions, each capable of being sealed off by use of hydraulically operated heavy sliding doors. These watertight doors are kept open only in port for the cargo of cars to pass from one compartment to another.
The design of a Car Carrier is such that the beam of the vessel reduces gradually from # 7 Deck to # 1 Deck (the lowermost one). But not by much.
Moreover the Car Carriers of yesteryear were not double hulled. Are they so now? At the present, I do not know.
So each subdivided space below # 7 Deck has approximately
150/3 x 25 = 1250 square metres surface area, actually less than a Bulk Carrier.
But were the main deck (#7 deck) to get flooded, the surface area becomes 150x30 = 4500 square metres. I know the odds of such a thing happening is low, but the spate of ferry sinkings in the 1980s and 1990s were always at the back of my mind. Because, in finality, a Car Carrier was nothing but an outsized ferry, but braving worse weather than a ferry is ever subjected to.
Was I right in being apprehensive of flooding of any one compartment?
Moreover, the thought process of this type of vulnerability to weakening of stability due to ‘Free Surface Effect’ led me to check the pumping arrangements from each compartment. They were woefully inadequate on all the ships that I worked on, having just a few bilge wells in the aft corners of the compartment, which were led through small diameter pipes to the Bilge Pump in the Engine Room.
I compensated for this lack by ordering two air operated Wilden pumps and kept them ready for use, also training staff during drills by actually connecting up and pumping out some water from the bilge wells. I used to regularly inspect the bilge wells and insist that they be kept clean of debris, rust.
Many on board used to think of this as one of my many phobias and overdoing a scenario when in the initial stages of my arrival on board, but used to humour me. Within a few weeks, they would have come to understand the importance of this vigil, after a couple of explanations from me during drills.
The two main precautions to prevent flooding
Ensure water tightness of the stern ramp and gangway access watertight door. Ensure stern ramp is housed properly and locked in place prior departure any and every port. The normal tendency is to instruct the Bosun and crew to 'square up' after departure. A responsible officer needs to cross check and double check the locking arrangements.
Very careful navigation to ensure no collisions take place. Any breach of the hull can be catastrophic.
Fire aspect on a Car Carrier - Inherent Weaknesses - Vulnerabilities
Another aspect of a Car Carrier that is very hard to control is a fire in the car decks. Fighting a fire with men entering the fire zone is fraught with danger. The space is so vast, and with impediments of hundreds of vehicles that can catch fire any time, it can be difficult to reach the seat of fire.
The alternative is to flood the area with CO2.
Then, we are confronted with another problem, that of completely sealing off and isolating that space before the release of CO2.
Depending on the size of the Car Carrier, the number of ventilation fans - all of them heavy duty ones, with large sized motors taking up a lot of the electrical load - can be anywhere from 20 to 40.
Although many in number, Ventilation equipment, fan motors, fan impellers, fan casings and - of utmost importance - the closing flaps, are one of the most neglected pieces of equipment on board.
These fans are totally under the control of the Chief Mate, with the Electrical Officer being called in case of any electrical failure. Their starting, whether on ‘supply’ mode or ‘exhaust’ mode, how many for each compartment that it services, how long in terms of time - are all decided by the Mate. He is the one in charge of lubricating the ventilation flaps and keeping them operable. The Engineers also should be involved but, almost always, never do so.
As narrated in Blog 86 (the ‘Anna’), it could lead to a situation where the flap handles are free to operate, but the flap inside has eroded badly or hardly exists.
After having joined a ship, I had the habit of checking all ventilation on board - Engine Room, Funnel, Deck, Car Decks, Galley, Accommodation - thoroughly, accompanied by the Second Engineer or the Chief Officer. They had to demonstrate the operation in front of me, as they were the ones who were responsible for their testing, upkeep and maintenance. To observe the flap movement and gauge its sealing potential, I would get the casing’s side inspection covers removed.
Invariably, at least 60 to 70% of the flaps would have eroded, some badly, some less. Motors would be rusty, casings thick with rust. Getting them back to a good condition would take months.
If the flaps are not sealing, how can the injection of CO2 into these spaces be effective in extinguishing a fire?
So the ship, especially a Car Carrier, becomes a deadly vehicle in case of a fire in the car decks.
So, after a detailed Condition Analysis, I would initiate Risk Assessment protocols and come up with methods of identifying and lowering the intensity of potential risks.
This led to a rather tortuous cycle for two men, the Electrical Officer and a helper, who would check all Fire Sensors in the Car Decks on a rotational basis. Side by side, fused lights used to be repaired. (In a Car Carrier, there would be more than a thousand tube lights).
Another was to keep tarpaulins ready to temporarily cover the defunct ventilators, till their repairs are completed.
The others, such as the heavy watertight doors, booby hatches, liftable ramps which seal one space from another, were easily checked and, if necessary, repaired.
Once a month I would gather the Bridge personnel to explain and make them familiar with the Alarm Panel for the Fire Alarms and the Indicator Panels of Watertight Doors and, on the later vessels, the booby hatches.

MacGregor
===== Continues in Blog 107 =====
Comments