Blog 105 == A Dry Docking that Quickly Went South - Oft Repeated Words in the Industry "I ----"
- ranganathanblog
- Jan 4, 2023
- 9 min read
"Marine Musings 34"
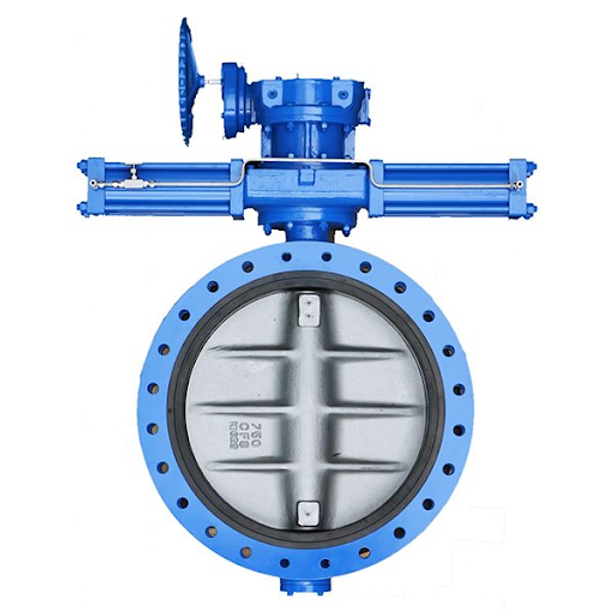
“MV =====”, a Bulk Carrier
01st Apr 2005 Shanghai to
31st July 2005 Dalian
When I came back on another fresh contract, I was asked to join the “======” in Shanghai. When I stepped on board, everything seemed very familiar. After a few minutes, I realised I was back on board a previous ship of mine. For whatever reason, the European Owners had decided to rename the ship as the “=======”.
Having been the one to have drawn up the dry dock specification during my last tenure on board, I found myself having to implement it.
The vessel was expected to dry dock in July 2005, about 3 months further into my tenure.
Looking at the correspondence of the past three months I had not been on board, I found nothing pertaining to the dry dock. I also found that the previous Chief Engineer - whom I had relieved - had left because he did not want to face a dry dock.
It was likely that the General Manager’s visit 2 months before had instilled some fear into him, which made him leave (as per the 2nd Engineer). The old Chief Engineer had performed well during his tenure - as per what I could see - so his reluctance to not continue perplexed me.
A month later, I had the opportunity to come to terms with his departure.
The same General Manager, an Englishman, once again visited the ship.
Rather autocratic, he expected instant obedience to his requirements. I had to tell him plainly that he should have sent us a message with his requirements a few days before his visit, so we could be ready. Now it will take a while. He wasn’t prepared for this kind of repartee, as he expected all of us to scramble at his command.
After a while, the obligatory Engine Room inspection took place. As we were going around, he kept irritating me by saying, again and again, “See what the last Chief Engineer had done in three months what you could not achieve in the 5 months that you were on board in the last tenure.” He pointed out several improvements made by the last Chief Engineer.
He continued in the same vein, but I took it in my stride. Just to provoke me, he added “What, cat got your tongue”?
He was obviously being racist.
I just replied “It is a matter of ethics”.
Him: “What ethics? What do you know about ethics”?
Not able to stand his tirade any longer, I stated “You Englishmen would know nothing about it after the subjugation of colonies around the world for centuries”.
Suffused with anger, he said “Explain yourself”.
I told him “If you had looked at the plans and the requisitions I had sent during my last tenure, you would not be so hasty in condemning me. Obviously, some of the required spares and stores were received after my signing off and the last Chief Engineer carried out what I had planned. But throwing these details in your face would not have been ethical. After I have taken over a ship, I will not complain about my predecessor. Those are my ethics.”
He was dumbfounded.
When back in the Office, I asked him “How is it that there have been no messages from you with respect to the Dry Dock Specifications sent by me? Have they been approved? What are the jobs that we will be carrying out”?
His reply “You don’t have to worry about it. It will be looked after by the Office”.
He left the ship.
Two months later, we were in the shipyard in Dalian, preparatory to the dry dock.
I asked the attending Superintendent what are the items being done in the shipyard / dock. His reply was a curt “You’ll come to know later”.
The next day, the Manager from the ship yard, who would be in charge of our ship, was in the Engine Room with a list, luckily in English with Chinese annotations. I quickly made several copies.
Looking closely at it, I realised that these contained very few of the specifications that I had sent to the Office many months back. Most of the items, about 90%, from my initial specification were missing. These were all items that could be done only in a dry dock.
No additional spares and stores, as requisitioned, had been supplied. A sense of impending dread pervaded me.
Meanwhile, the mandatory hull thickness gauging needed to be started. My suggestion - put up during my last tenure - of a Surveyor and a licensed Gauging Team to sail with the vessel to gauge most of the tanks / hull, had been thrown out of the window. We were now coming to terms with it, after arrival in the Ship Yard.
Suddenly, the entire ship’s crew found itself at the beck and call of the attending Superintendent opening ballast tanks, gas freeing them, in order to escort the Surveyor and the Gauging Team into the tanks as listed in the Enhanced Survey Programme (or whatever it was called in 2005).
As the hours went by, the gauging revealed that more and more hull sections were corroded beyond the 10% allowance and the tons of steel that required to be renewed was climbing up.
The three days of gauging various tanks brought to light rampant corrosion, with the steel quantity for renewal having gone upto nearly 200 tons, with a few more tanks yet to be gauged.
Having used the shipyard’s gauging team and with the attendance of a resident Classification Surveyor, the results could have been favourably tilted to bring more business to the shipyard, but not by much.
Also, now the estimated stay in the yard shot up from 15 days to 25 / 28 days, with all the additional steel work.
Further, with unscheduled and out-of-specification work, the costs went up as the yard could charge 100% of the tariff.
I did not make things any easier for the attending Superintendent by pointing out that I had particularly suggested that this gauging be done well prior docking, so that we can specify each section to be renewed, which would have been tariffed at 50% of what we would be paying now.
More problems and trouble were to follow as we entered the graving dock and the ship rested on the keel blocks.
The Propeller ‘drop’ was within limits.
But the rudder bushes’ clearances were well over the limit, requiring dismantling of the rudder and renewal of the rudder bushes. But they had not been ordered, in spite of my having put up a requisition nearly 8 months ago. An emergency requisition was sent out for new bushes, which would take a month or more to supply.
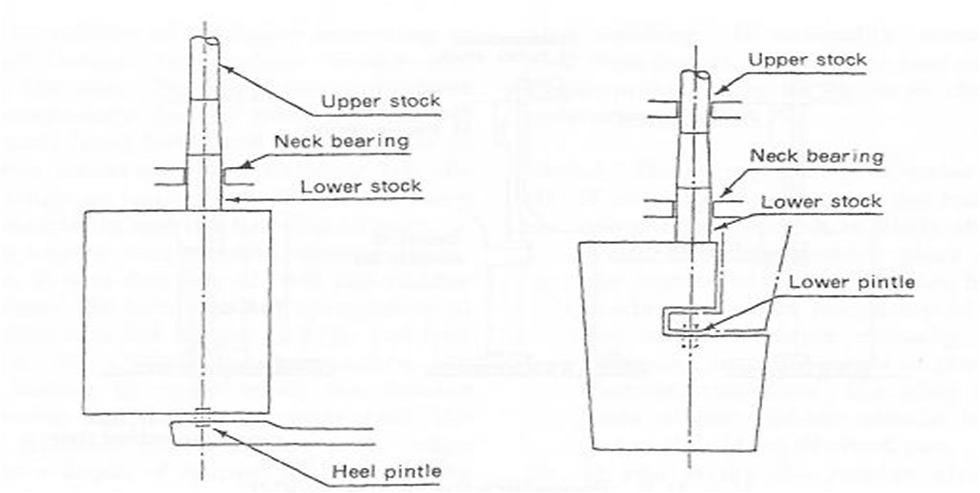


Feeler gauge in use to check bush clearances

Different Sized Rudder Bushes
The estimated number of days’ stay in the shipyard was increasing.
4 days had passed since coming into the Shipyard and I was still not aware of what items of my initial specifications had been sanctioned and what had been thrown out.
With me being kept in the dark about the dry dock, the mismanagement of the first four days, the essential spares that needed to be supplied for the work that I had listed - which had not even been ordered - including the rudder bushes, led me to believe that the whole dry dock was intended to be a sham, with the least work being carried out at the lowest cost, the only aim being to get the renewal of all trading certificates over and done with.
To my way of thinking, gleaned over 3 decades, the philosophy behind a dry dock was to primarily ensure the water tight integrity of the vessel at least for the next five years, so that she does not flood from a weak hull or pipelines and also ensure the propeller or the rudder does not break or drop off midocean. This is for the safety of the personnel and the ship.
With the way things were going, a confrontation with the Superintendent was inevitable and it took place the same morning that the Class Surveyor was supposed to carry out his Engine Room inspection.
I had not been told by the Superintendent what jobs had been authorised. The Superintendent told me - in fact, ordered me - to steer the Surveyor away from areas that would invite deeper scrutiny, so as to keep dry dock costs down. My point blank refusal upset him- I told him that the Class Surveyor’s inspection was for the benefit and safety of the ship, not for skimping on essentials.
I led the Surveyor to the worst areas and discussed renewals, repairs with him, in spite of the Superintendent’s efforts.
Net result
Thickness gauging of the box like sea chest areas that protrude into the Engine Room were wasted away and needed steel renewal.
The stub pipes on the sea chest before the main sea valves were wasted and needed renewal.
All the other valves on the sea chests - steam blowing valves, air vent valves - were all in bad condition and needed renewal.
Being a large ship, the sea chest valves, for suction from sea, of the Ballast System and the Main Sea Water Cooling System were individual and also large in size. (600 mm and 400 mm?)
After removing the sea suction strainers on each line, we could crawl into the ballast pipeline and check closely the condition of all butterfly valves on the line, including the intermediate valves.
Nearly 60% of the valves had their rubber elastomer seats damaged to varying degrees.
Why do butterfly valves fail?
The most common failure of a high performance butterfly valve is the rubber elastomer inside the butterfly valve. It can tear, wear, wear or perforate and even fall off after continuous use. The conventional thermal vulcanization procedure is not able to meet the repairs on-site.

Hand operated butterfly valve through bevel gears to whatever angle is required (from 0 to 90 degrees)

One step quick operating butterfly valve - need to turn the handle anywhere from 0 to 90 degrees - meant for smaller sized valves

Butterfly valve operated by hydraulic cylinders - remote operation - indicator on top of cylinder (not visible in image) shows to what degree valve is open - 0 to 90 degrees
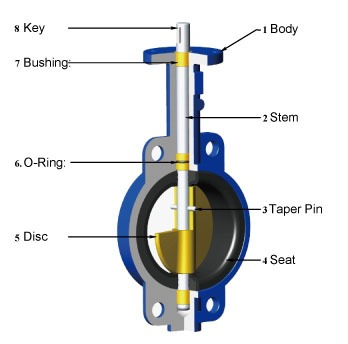
The main parts of a butterfly valve

Different parts of a butterfly valve - spares difficult to procure unless you go to the manufacturers directly, with the exact model number.
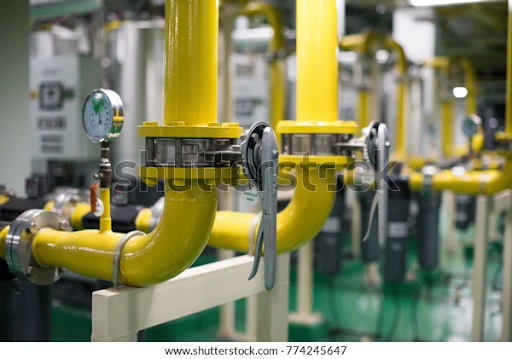
Some smaller butterfly valves on the line

Courtesy Shutterstock
Rubber elastomer seats in which the disc rotates 90 degrees.
Elastomer seats get damaged mostly due to over tightening the valve, the other cause is age of the valve, maybe 15 years or more.
The Surveyor was only interested in seeing the hull mounted valves and recommended their overhaul.
Now, there had been requisitions pending for all these valves for over 6 months but none of them had been supplied.
The insistence of the Superintendent that he will only overhaul the hull valves as per the Surveyor’s recommendation and not one single one more, had me fuming. It came about that those very valves could not be overhauled and had to be renewed. The Yard had to purchase Class approved ones at a high cost.
I had a hot argument with the Superintendent about the renewal of the intermediate valves on the ballast line, as they had been giving us trouble and could cause heavy flooding of the Engine Room. He remained adamant.
Having thought long and hard about it, I sent out my resignation letter - effective immediately - stating that I will not be a party to compromising the vessel’s watertight integrity because of an obstinate and technically ill informed Superintendent. The e-mail went out to Barber’s, copy to Owners.
The next morning, I took the Ship Yard Manager and instructed him to renew all the valves that I had listed, telling him that I will sign for them. I owed at least that much to those who would be coming in my place in the future - good, tight, reliable valves on the sea water line as well as the ballast line.
The overhauling of turbochargers, steering gear, cleaning of air coolers - the company can be either coerced into doing them at a future date or forced into doing them due to failures.
A couple of days later, the General Manager - whom I had met before - flew in. After being briefed by his Superintendent that the Chief Engineer was not co-operating, he came to me with a “What’s this all about?” expression. I did not say a word, but straight away took him down to the Engine Room and showed him the condition of all the valves - all had been removed from place.
He agreed that all valves required renewal. I sat with him for a few hours and went through the details of the specifications I had sent to the Office 6 or 7 months ago, of which more than 90% had been cancelled. In the interest of the safety of the ship, I asked him to at least overhaul the steering gear, to which he agreed.
He then asked me to withdraw my resignation / immediate leave application.
I said no and told him that I am tired of fighting officialdom, inexperience and downright ignorance every step of the way while working for his company in the last 4 ships.
My reliever came 2 weeks later.
By then, the vessel had been towed out to anchorage, awaiting the spare rudder bushes, all other work having been completed.
I handed over and left, with the vessel at anchor.
I believe she waited more than a month to get the rudder spares, re-enter dry dock for the fitting and then sail out.
All-in-all, what was supposed to take 15 to 18 days, took 50 days.
=====
My next ship was the Federal Sumida, renamed Lowland Sumida, a Bulk Carrier. I have no recollection of this ship.
“Federal Sumida”
10th Dec 2005, Yokaiichi, Japan
To
09th March 2006, Myrtle Grove, Florida
Renamed
“Lowland Sumida”
09th March 2006, Myrtle Grove, Florida
To
01st June 2006, Mobile, Alabama
===== Continued in Blog 106 === "Marine Musings 35" =====
Comments