Blog 104 == A Bevy of Bulk Carriers
- ranganathanblog
- Jan 1, 2023
- 10 min read

“Marine Musings 34” - “Orchid River”, “Ataman”, “Atlantic”, “Bulk Atlanta” / “Amazon”, "Federal Sumida" / "Lowland Sumida" - 7 Names but Five Bulk Carriers
To all my Friends - Greetings on the occasion of the New Year 2023
I started this Blog exactly a year ago for want of something better to do, other than twiddle my thumbs. My son, Amrith, suggested I write a Blog and publish it regularly, setting up the system and sorting out all my teething problems like how to import images into a blog etc., since it was not a mere 'copy / paste' exercise (it had just one more step).
Before then, I had been writing - and storing - bits and pieces of events, starting from my childhood days, that were most likely not of any significance or interest to anyone but me. From the start of the year 2022, I went back in time and sank into the memories of events of decades ago.
I surprised even myself at the startling depth of memories of events in the formative years, the first 50 years being very vivid, as I plunged into Life, living and enjoying the moment. The love for my job as a Marine Engineer at sea, the omnipresent Sea itself with her myriad moods - all made for a remarkable sticker board of memories.
So, going back and forth into Seaman's Book (CDC), I willed my bits-and-pieces of recollections fall into place and, as more events came cascading down, expanded on what I had started.
Every Sunday morning and Wednesday evening, twice a week, I published what I had written and edited the past week.
Why publish on Sunday morning and Wednesday evening? Why not other times? By a perverse logic, I wanted to publish my Blog twice a week (168 hours). So I tried to send out my Blog every 84 hours, as close as possible.
I do not know if any of my readers realise it, but they have given approximately 17 hours of their time in the year 2022, plodding through my blogs.
Thank you.
“Memory is the Mother of all Wisdom” - Aeschylus wrote 2700 years ago.
The above being true, I would say that I was on the decline, as my memory of the last ten years of my sea career - 1998 to 2008 - is rather sketchy, compared to the first 28 years. Maybe a touch of indifference, complacency, pervading my sea career after 3 decades at sea? Possible.
Or was I falling a victim of “Peter’s Principle”, which states that in any hierarchy every employee rises to his level of incompetence?
Starting from 1998 till 2005, I served on a series of Bulk Carriers, a total of nine.
Except for the “Tachibana”, a new building that I took over from the Yard and the "Federal Sumida" renamed "Lowland Sumida", all others were “manned” vessels, where the crew came from Barbers, but operational management was not Barber’s.
Three of the 8 (Brilliant River, Rubin Power and Orchid River) were managed by ‘Navix’ Singapore. ‘Navix’ were a very good team to work with and I gave my best.
4 of the 8 Bulk Carriers were managed by a European based company, regressive rather than progressive. But, being “manned” vessels, one could not let Barber’s manning to be questioned, that the staff were not competent or professional enough. So it came to a state where all dialogues, plans etc were in the form of e-mails or letters, including repeated requests for the supply of long forgotten essential requisitions. They acted as though the Safety Management System did not apply to them. I, on my part, did not confront them but made sure that all my objections were in writing.
“Marine Musings 34” - “Orchid River”
23rd May 2001 (Mizushima) to
21st Nov 2001 (Mizushima)
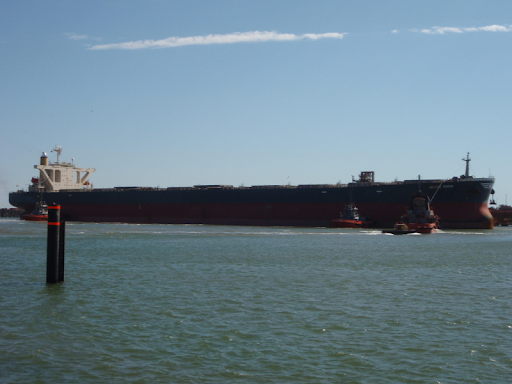

Courtesy Tropic Maritime Images
Vessel Type: Bulk Carrier
Gross tonnage: 85,437 tons
Summer DWT: 170,896 tons
My stay of 6 months on the “Orchid River” was almost an exact rerun of my tenure on the “Brilliant River”. ‘Navix’ Singapore were the Managers.
Good environment, good working conditions, same type of problems, good support from the Singapore ‘Navix’ Office - all made for a pleasant tenure.
Another cause for these happy times on board the larger bulk carriers were the 2 to 3 weeks anchorage stays in various Australian ports, waiting for our cargo to be accumulated in the port.
During these times, there would, inevitably, be international cricket matches being played in Australia. On three occasions it was India versus Australia.
Being a cricket buff, I would ask the Captain to anchor at a place where the TV reception was at its best. So we would wander around seeking the best place to anchor.
Those were the days that Rahul Dravid earned for himself the title of ‘ The Wall’ and VVS Laxman was at his fluent best.
We would adjust our working hours to conform to the game hours.
MV Ataman

“Ataman”
2nd Nov 2002 (Koshichang) to
13th May 2003 (Singapore)
DWT 72964 T
LxB 234 x 32 mtrs
Engine MAN-B&W, 6S60 ME-C
Year 2001
Builder Samsung S Korea
The only memory I have of this ship is a transit of over 2000 nautical miles up the Amazon to load iron ore in one of the most remote places on earth, surrounded by dense forests.
(I am not even sure if I made the Amazon trip on this ship or am I confusing this with another ship).
The mouth of the Amazon and the transit upriver were truly jaw dropping, due to the sheer size of the river. At the delta, neither bank could be seen. Even after a 1000 nautical miles, the banks were a distant scene. A bit eerie, as there were no fish, only flotsam.
We had to sail up into one of the tributaries to our load point. It was just an outpost surrounded by the dense jungle, through which a solitary cargo belt came meandering along, appearing suddenly out of the dense jungle. I am not sure how far was the mine.
“MV Atlantic”
18th Sept 2003 Gladstone to
25th Apr 2004 Singapore

“MV Bulk Atlanta”
01st Aug 2004 Rotterdam to
06th Jan 2005 Amsterdam
This ship was also managed and operated by a European based company, with Barber’s providing the manpower.
All I can remember of the”Bulk Atlanta” was the fact that she was due for drydocking in July 2005, nearly one year after my joining.
The first month was spent in detailed planning for the year prior drydock, with necessary requisitions going out to support the plan. All (exhaustive) details and reasons were given.
The next 4 months were busy with detailed specifications for a Dry Dock and the requisitions of spares that were needed for use in the dry dock.
A Dry Dock happens to be a period that is very important to the longevity of a ship, the ship being an asset of the Owner. I used to start preparations for a Dry Docking about 10 to 12 months prior the docking. Why so early?
All items or parts of the ship that are always under water are exposed during this particular period.
As an example, take the rudder. Rudder pintle bearings, rudder bushes wear down over the years and may require renewal. An educated calculation needs to be made if these parts will last till the next docking. So, one digs up all the old records and, tabulating them all in a table, calculates the wear rate per annum or running hours. The manufacturer’s limits are noted. The rate of wear is never linear and increases with increased clearances. Drawing a graph and extrapolating, one can arrive at an educated solution.
The older the ship, the more difficult it is to source spares for rudders, as no off-the-shelf spares are kept after the first year of a new ship.
Moreover, the Shipyard - where the ship was built - may have gone out of business. These spares are more or less made-to-order, so to source somebody who would make them takes time. Manufacturing them also takes time. Supply to the ship sometimes is done practically at the last minute. Only after the spares are available can we risk opening up the rudder.
The same applies to steering gears. The steering gear manufacturer may have closed down. Spares are obsolete. Since steering gear jobs - complete overhaul - are not done by ship’s staff, a service engineer with expertise in that particular brand and make has to be hunted down and kept on standby.
Or the ship may be having a Controllable Pitch Propeller, which needs that particular maker’s service technician to carry out the service.
Or an engine part needs overhaul, like an obsolete piece of equipment - “Roots Blowers”.
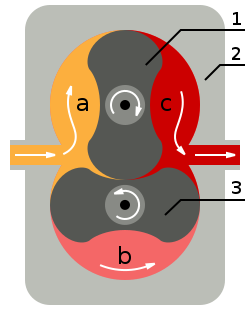
A Roots blower with two-lobed rotors. Most real Roots blowers' rotors have three or four lobes. (animated version) Key:
Rotary vane 1
Pump body
Rotary vane 2
Intake
Pumping
Forced air or air-fuel mixture into intake manifold
Courtesy Wikipedia
Although not complicated, the job is cumbersome and takes a lot of time, which kind of time is available only when the vessel goes into a dry dock.
If everything is arranged well in advance, these jobs will not delay a vessel. But where a ship has to order for spares, technicians, on the basis of on-site inspections, the delays can be quite damaging to an Owner’s budget and business.
Perhaps the maximum delays that take place to a ship in a dry dock is the unplanned steel renewal - renewal in areas where there has been heavy corrosion and steel thicknesses have reduced by more than 10% of the original. This may require other ancillary work, such as emptying, cleaning and gas freeing a fuel tank, that delays the ship further.
The better and more detailed the planning and submission of specifications to the Ship Yard, the cheaper it becomes for the Owner of the vessel.
Ship Yards normally have a “Tariff” document that specifies the cost they will charge for each item.
The simplest of examples is the renewal of a particular pipeline. They charge separately for
Length of pipeline - suppose the length to be renewed is 9 meters, they will calculate their invoice on the basis of 12 meters length, as pipelines are supplied in 6 meter sections, with 3 meters (supposedly) going to waste.
Material of pipeline - different types of steel, galvanised or ungalvanised, maybe rubber coated internally, bronze, copper or other materials
Diameter of pipeline
Thickness of pipeline - usually denoted as Schedule 40, Schedule 80, Schedule 160 etc., which are standard thicknesses in the maritime industry.
How many branches - and of what diameter and length - on the pipeline
How many bends on the pipeline and what angle the curvature of the bends
How many flanges - thickness, diameter, bolt hole sizes, size, number and material of bolts, nuts
Each detail takes time to gather.
Suppose that is the entirety of the details that you would have to give for one pipeline, specifications that a ship submits increases ad infinitum as the number of items for dry dock increases.
The Shipyard, when they receive this specification, take out their “Tariffs” document and calculate on the basis of each detail. Where it was calculated manually 50 years ago, these days dedicated software takes care of it in seconds. This tariff has an inbuilt clause for their manpower charges.
Suppose, as per their tariff, it works out to $1000.
The Owner / Manager has specified a certain provisional date of vessel likely to enter the shipyard. During that date and period, (suppose) the Shipyard is expected to be full with many other ships.
The Yard is, then, likely to charge 100% of the tariff, $1000.
If the Yard is likely to be near empty during the period that the Owner has specified, just to attract some business and keep their employees busy, the Shipyard will give a 40% or 50% or even 60% reduction from their tariff, halving the cost of changing that pipeline to $500.
The details of the specifications then become important, for a total estimate of the full dry docking costs.
So does the wording of the contract - Memorandum of Agreement - between the Owner and the Shipyard.
During the five month period, I prepared the Dry Dock Specifications in detail and sent it along.
Included were
The two Main Sea Water Suction Shipside valves - both were leaking badly, making the cleaning of suction filters a tense job. (Luckily, the Sea Suction Strainer Inlet valves were water tight).
Several Ballast Line valves, shipside and intermediate, were leaking. Because of the leaking valves, the main ballast lines were always under pressure, upto the Ballast Tank Hydraulic Valves. Deballasting had become a complicated affair, due to the leaky intermediate valves.
Water tight integrity of a ship is not only for the hull, but also for all the sea water valves, whether ship’s side or intermediate. With different valves holding (tight), one can work on other sections of pipelines without fear of flooding.
As per Class Rules, only the shipside valves have to be overhauled and shown to the Surveyor. If being renewed, then the supplier has to provide a Certificate that the valve has been hydrotested in the presence of a Class Surveyor.
Many smaller valves were overdue for renewal, all of which were included in the specifications.
Most of the valves on this ship were ‘Butterfly Valves’. I anticipated that the rubber seats of these valves were either damaged or worn and/or the valve discs broken.
Specifying the sizes, dimensions, I left the option of either renewal of the valve or the renewal of parts of the valve to the Superintendent.
Main Engine jobs included chemical cleaning of air coolers and overhaul of the turbochargers.
With increasing age of the ship, more stringent Class inspections were being introduced, especially for bulk carriers and oil tankers. These included thickness gauging of the hull, stiffeners, web frames etc, with special attention being paid to underwater sections. With each dry dock, the Continuous Survey Programme and the Enhanced Survey Programme requirements for hull gauging expanded to include several more tanks, all of which takes up a lot of time if done in the dry dock. Moreover, if a wasted section needed to be renewed, further delays can be expected as they were all unplanned, untariffed, unbudgeted.
In order to reduce downtime in the Dry Dock, I outlined a plan wherein, over a period of several months prior drydock, we get an authorised gauging team and a Class Surveyor to sail with the vessel and carry out Thickness Gauging. All areas with reduction of thickness of 10% or more can then be marked off. These can be included in the Dry Dock Specifications, quoted for in terms of cost and time.
The full bunch of Specifications and the related requisitions were now in the hands of the Superintendent when I left the ship in Jan 2005.
In the 5 months that I was on board during this tenure, nothing was supplied. By this time, I had been a Chief Engineer for 23 years and I was getting tired of fighting with Managers for spares and stores for improving a ship.
With the exception of ‘Navix’ Ship Management Group and about 50% of the Barber managed vessels, it was an uphill task all the way, mostly useless, unless you stood your ground again and again and again. This year, I found that the gusto for a continued argument with the Management was missing, especially after the excellent relations with ‘Navix’.
The reason for my rather exhaustive narrative about Dry Dock Specifications will, likely, be self explanatory when reading about what transpired on my next tenure.
===== Continued in Blog 105 =====
Comments