Blog 101 = Of Stripping Eductors, Duct Keels, Bell Mouths and 600 Tons of Unpumpables
- ranganathanblog
- Dec 21, 2022
- 7 min read
ā
“Marine Musings 31” "Brilliant River"

Ballast Valves:
Ballast line hydraulic valves fitted on to the ballast tanks had been giving trouble for at least over a year, with no planned action being taken by anybody. This ad hoc policy had, on occasion, cost the ship dear, in terms of delays or the inability to pump out ballast which resulted in carrying that much less cargo.
The standard practice had been for the Engineers to set up the line - the manual valves involved for either ballasting or deballasting - and hand over the system to the Chief Officer, who would control the rest of the valves - all hydraulic - remotely from the Cargo Control Panel in the Ship’s Office.
Practically in all voyages for the past year or so, the vessel had been sailing out with quite a bit of unpumpable ballast, net result being that much less cargo.
Although the previous Chief Engineers had been told, they used to throw it right back at the Chief Mate, saying that he did not know how to pump out ballast. The wrangle had gone on.
During the ballast voyage, the Chief Mate had been working with me on the hatch covers. He had, then, told me about carrying unpumpable ballast for well over a year and the lack of an analysis and study of why(?) by anybody. I assured him of a thorough study in the first load port.
At the load port, the Second Engineer and I involved ourselves in every bit of action surrounding ballast operations.
Several ballast line and tank side hydraulic valves were troublesome and would operate very slowly, needing to be opened and closed several times to open them fully. Even then, some would open to only varying degrees, 40%, 50% and so on, as indicated on the control panel, indicating - as one of the causes - air in the system.
The stripping of a few of the ballast tanks was very slow.
I helped the Chief Mate in taking out maximum ballast, using a combination of stripping line and the main pumps, taking advantage of list and trim of the vessel to the fullest. My Fifth Engineer experience of being in total charge of deballasting operations stood me in good stead at this time.
We sailed out with about 350 tons of ballast with this particular loading, versus 500 to 600 tons on previous voyages. Nobody had been bothered about the slow but ever increasing unpumpables, as the vessel itself was a 150,000 tonner.
One particular ballast tank had nearly 200 of the total of 350. Noted for inspection.
With coal on board, no hatch cover work was possible.
So concentration was on the ballast system.
With valve opening being problematical, we checked the hydraulic pump and circuit. I suspected that a lot of air had entered the system, making it erratic. The most likely place for air ingress into the system was the pumps’ gland’s mechanical seal.
On overhauling the pumps, the mechanical seal was found broken, which would have caused air entry into the system, renewed.
The hydraulic oil was dirty. We introduced a better filter into the system and cleaned the oil. We could not renew the oil in its entirety as our stock was very little. This was done later after receiving fresh oil.
Running the system, a lot of air was bled out. We would run the system every second day and bleed out decreasing quantities of air, till we reached satisfactory levels.
Then we tackled the ‘stripping’ problem.
There were two eductors.
Both were pitted, worn and needed renewal. We had one spare, which we used. 2 more were requisitioned and, later, the second one renewed.

For access to the tank ballast valves, we had to enter the Duct Keel, diagram below.

Interior of Duct Keel (representative)
Note the rails for a maintenance trolley

There was no record of any inspection of or entry into the Duct Keel. Using portable blowers, the duct keel was ventilated, checked for man entry and entered from the Engine Room side.
Being a large bulk carrier, the Duct Keel was rather large, larger than the image above. A large sized trolley on rails with a unique hand operated system for travel was inside. (Reminded me of inspection trolleys on railway tracks, used in the 1950s and 1960s).
All the pipelines were led through the Duct Keel - ballast, fuel oil, diesel oil, steam, hydraulic pipes, electrical cables etc.
We were now in line with the Double Bottom Tanks, not above it but by the side of the tanks. Only the Keel Plate was below us. All manholes were on the sides of the Double Bottom Tanks.
There was quite a bit of oil + water mix gathered at the after end, hydraulic oil + condensate, but had dirtied the entire floor.
We had our work cut out for us.
Using the bilge suction, we emptied the oily mix. Cleaning took nearly 2 days.
As an aside, I found that Duct Keel aft soundings had never been taken. Now introduced into the ‘Daily Soundings’ record.
It was a combined Deck + Engine operation all through.
Bathi Saab got all the lights going.
We tackled the ballast tank with the maximum unpumpables first. We cracked open the aft manhole door of the tank and let the water flow out at a controllable rate into the Duct Keel, Using a Wilden pump and the Bilge pump, we kept removing the water in the Duct Keel.
Once the water stopped flowing from the partially slack manhole cover, we removed the manhole cover and put in a siphon pipe and a Wilden pump to empty the tank. This took more than a day.
After tank ventilation a thorough tank inspection was carried out for Chief Mate’s report. I led the Mate in pointing out areas that required thorough checks, the condition of steel, frames, brackets, pipelines, ballast line expansion bellows’ condition, supporting brackets, wear on the pipes where the U-clamps were tightened on the pipes, tightness of nuts and bolts etc.
There were many drain holes at the bottom of the vertical floors that were choked with scale preventing the easy flow of water to the suction, all cleaned.
The bell mouth of the ballast line of that tank, representative image below, was loose. Some bolts were loose, some fallen out. There was quite a bit of gap between the two flanges, causing the pump to lose suction when the water level reached the flange level, as air gets sucked in.
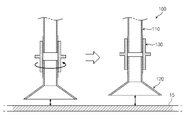

Ballast Line Bell Mouth at suction point
We cleaned the flanges, cut new gaskets and used nuts and bolts with spring washers and put back the bell mouth.
A very interesting observation made at that time was the pitting of the Keel Plate below the bell mouth. The Keel Plate is, very likely, the thickest plate on the ship, unless the vessel was an Ice Breaker.
Moderate pitting was observed. This pitting occurs because of the cavitation caused by air bubbles and water force, when pumping in or pumping out the water. Noted down for dry dock thickness measurements.
Surprisingly, the Stripping line suction bell mouth was also loose. Done.

Stripping Line Bell Mouth
Over the next several months, we completed the inspection of most ballast tanks, with two + two more bellmouths found loose. The Forepeak tank was cavernous and rather forbidding, being the forepeak of a large vessel.
These inspections were done in a phased manner, but were not in any maintenance list. The near future would see these tanks coming under an inspection / maintenance software programme.
As the spares for overhauling the ballast tank hydraulic valves was low, we took up the overhaul of 2 of the suspected valves - the worst ones - and overhauled them, finding several seal rings damaged. Requisitions went out. Almost all were overhauled by the time I left.
Steam leaks, condensate leaks and hydraulic oil leaks were all rectified. I wanted to slowly get the whole duct keel painted, but it was too big a task for the time available and priorities to other jobs.
And, at the next loading, what was our ROB of unpumpable ballast?
100 tons.
Even this came down further as we entered other tanks.
Before this, the staff had been apprehensive of entering Duct Keels and being at the bottom most part of the ship. By now, they were going in and out of it as through an Engine Room entry door.
Side by side, Engine Room machinery and Engine Room general condition were being upgraded, starting from the bilges. All leaks were rectified, inflow on to the tank top was stopped. All pipes were washed down and painted, colour coded.
It started from the bottom and vended its way upwards.
The lethargy and the taking-it-for-granted attitude was thrown out.
I told my staff that they had to make up for all the leisure time that they had enjoyed before, where no work was done at all.
The normal work hours of 8 to 5 were extended from 7 to 6. Meal timings were adjusted to suit. As there was no watchkeeping, I had the full Engine staff on day work. Nobody was spared.
After about 3 months of my being aboard, we had an Internal Audit, External Audit, a Class Annual Inspection and an “AMSA” (Australian Maritime Safety Authority), all quickly following one another, all with no Non-Conformities.
Monthly Maintenance Reports were detailed ones, most of the time with photographs.
During my tenure, the first Captain was with me for about 4 months and the rest with a second Captain.
One of the memories that I carry is of calling a port on the West Coast of Canada (Prince Rupert? Not sure), where we stayed less than a week. The FIFA World Cup Final was being played the day after our arrival. The Captain and I went ashore to watch the match live in a Sports Bar, but found that the bar did not cater to football. They were all interested in ice hockey.
The bartender - who was also the owner - insisted that, as guests from another country, we be allowed to watch the match. Brazil 0 - France 3. We bought the regulars a round for their hospitality.
One of the actions of the second Captain left me a bit bemused, but I let it ride.
Being of a particular religious denomination, he used to gather the entire deck and engine crew, who were all of the same denomination, in the Crew’s Dining Hall on Sundays. He then conducted services for the crew for about 1½ hours. He meticulously prepared for them by making small booklets with the details of the sermon of the day.
Most of the Sundays were off for the crew, when the vessel was at sea. So all the crew, who were of that religious denomination, had no other choice but to attend.
Meanwhile, I would gather all the Engineers in the Engine Control Room for some long sessions of any technical subject till noon.
After 2 such services, the engine crew quietly came to me and asked me to give them work on Sundays, even if they had to work without overtime. I kept them busy, as work is not difficult to find on any ship.
As taught to me by my seniors in South India Shipping Corporation, there are two things a sailor should not discuss nor be a part of the discussion. The first is politics and the second is religion. You never should flaunt your knowledge and opinions of the former, nor lecture others on your adherence to the latter. All other subjects - from philosophy to the other extreme - are permitted, for friendly discussion.
I left the ship with the Managers (Navix) + Owners very happy with all the improvements made.
===== "Marine Musings 32 next =====
Kommentarer