Blog 100 = "Brilliant River" and Side Rolling Hatches
- ranganathanblog
- Dec 18, 2022
- 9 min read
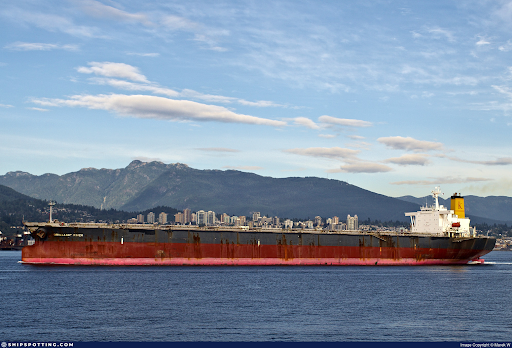
"Brilliant River" “Marine Musings 31”
20-08-1998 (Mizushima) to 29-01-1999 (Mizushima)
150,000 dwt
1994 built
Navix Ship Management Singapore
The downturn in Shipping and in the Japanese economy in the mid and late 1980s forced many a Japanese ship owner to look beyond nationalistic pride and go into survival mode.
Two or three Japanese companies banded together, started Navix Ship Management with headquarters in Singapore.
They turned to some of the established Ship Management Companies to provide them with qualified staff, which is where Barber Ship Management came in, keeping operations to themselves.
I had to first fly to Singapore and be briefed at their Office. They had a good set up which made me think it was a well run company.
For the first time, I saw the existence of a Performance Analysis Wing which kept track of many of the performance parameters sent daily from the ship, analysed them and sent back suggested corrective measures to the ship. I thought it was a very progressive way of increasing the efficiency of running ships. But, like any ‘start up’ in its infancy, the formulations and assumptions were crude, compared to the sophistication of analysis after 2010.
Previous to this, shipboard personnel, especially Chief Engineers, relied on their own experience to set certain important parameters to run the Main Engine or other ancillary equipment.
The only help used to come from Fuel Analysis Reports which specified results and set certain limits for
Water Content and advice on how to get rid of the water
Ash, vanadium, water, aluminium, silicon, sodium - If content is high, what specific treatment is required for the Fuel Oil
Cetane number and Ignition Quality that can be expected
What kind of corrosion and deposits can be expected if certain chemicals such as sulphur, sodium or vanadium are in excess
What temperatures to maintain at the Purifier for optimum purification.
What should be the temperature of fuel oil at injection.
The Analysis Wing in the Navix 0ffice, I found on sailing, regularly advised the vessel on such matters, even though the Fuel Oil Analysis report from the Analysis Laboratory is immediately sent to the ship also. (Over a period of time, I have observed that quite a few Chief Engineers do not bother with the recommendations of the Laboratory). So, they are forced to act on recommendations that come from the Office.
Another aspect I liked about their set up was their commitment to the supply of spare parts and stores.
On receipt of a requisition in the Office, if there is no activity on that requisition for more than a week, the Superintendent will have to answer to his superiors.
If a requisition for spare parts is not sourced and ordered within 15 days, the Superintendent will have to answer to his superiors and also inform the vessel giving reasons for the delay.
Delays in supply also need to be answered.
For the first time, there was accountability on the part of the Office staff.
These measures were all thanks to the implementation of the ISM Code.
To my surprise and the harbinger of good omens, my arrival on board , although expected, quickly brought all the senior staff to the gangway to welcome me. My luggage suddenly disappeared, only to have it reemerge in my cabin.
Looked like my reputation, whether sullied or pristine, preceded me.
Three of the staff had sailed with me when in their junior ranks, the Captain, the Chief Mate and the Third Engineer.
At dinner, an hour or so later, I was effusively welcomed. The Captain then told the Chief Mate, even in front of the outgoing Chief Engineer, “Now that Bada Saab is here, your problems will reduce but your work load will go up”.
As the outgoing Chief Engineer was to leave early next morning, he and I spent the next few hours in ‘handing over - taking over’ details.
I made it plain to the outgoing Chief Engineer that I was disappointed with the state of the Engine Room, given the laid back voyages, a good length of anchorage stays that gave enough of time to improve the ship’s condition. It only needed a bit of organisation, a bit of zeal. I clearly told him that my report - to be sent after a couple of weeks - would not be in his favour.
As my arrival was known to them a week back, the Third Engineer had quietly told the Second Engineer “The new Bada Saab is very particular about many things”, which prompted the Engine Room staff into a flurry of activity, mainly splashing on paint. It fooled nobody.
The condition of the Engine Room bilges on a ship is the best reflector of the quality and depth of maintenance that the Engine Room staff had carried out for the last year or so. It was bad, filthy, oil and water floating around.
Along with some other parameters, I use the condition of bilges to evaluate the sincerity and quality of work done on board.
The Brilliant River was a beautiful ship, but shabbily treated and allowed to run to seed.
Her run was mostly Japan - Australia - Japan, mostly carrying coal.
Within the first few weeks, the year’s plan was formulated, necessary stores and spares requisitioned, 1st batch received, and the vessel embarked on a planned mission.
Perfect coordination was established between the Navix Office and the vessel.
Navix had, till then, been compromised by the fact that they did not have an in depth view and a planned perspective of the ship. Only ad hoc measures were being instituted, based mainly on an Internal Auditor’s Report or a Classification Society’s Inspection or Audit.
Substance always matters more than content. The depth of perception and, subsequently, understanding of a problem or a defect, is what separates a technocrat from an Engineer.
Side Rolling Hatches and Problems
There were two chronic problems, on the side rolling hatch covers and on ballast line hydraulic valves.
On the side rolling hatches the main operational deficiencies could be divided into several parts.
Bearings of hatch rollers very often breaking into pieces, making the opening of the hatch cover a tense and cumbersome process, with the loader hovering around the hatch waiting for it to be opened to start loading cargo into that hold or cranes with grabs waiting for the hatch cover to be opened to discharge cargo.
Delays meant off hire.
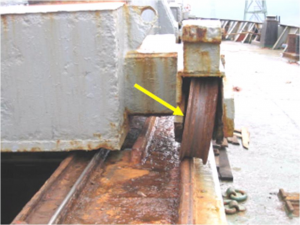
Evidence of a Damaged Bearing
Since it was an often recurring problem, temporary measures were in place - chain blocks, wires, shackles - to open the hatch cover. What was supposed to take 5 minutes now extended itself to 30 minutes to an hour.
The hatch covers were designed to be lifted from their battened down position by the use of hydraulic jacks connected to a hydraulic system. Once the securing cleats are opened, starting the hydraulic pump and operating a lever sends pressurised hydraulic oil to a series of jacks. The hatch cover wheels which, till now, had been resting in the slots cut into the hatch coaming, now start moving up due to the hydraulic jack pressure.

Courtesy MacGregor - Note the Blue Coloured Hatch Wheel resting in a Slot, on top of a hydraulic jack. On operating the hydraulic jack, the blue wheel moves up. The yellow coloured T- piece also moves up to become part of the trackway. The red portion is the hydraulic jack.
This hatch cover is in the ‘closed’ position.
The pistons of these hydraulic jacks have a T-shaped bar screwed into the top of the piston which pushes the wheels upwards, till the top of the T aligns itself with the rest of the hatch rail or coaming. The wheels are then capable of moving along the width of the hatch coaming.

Overhauled Spare Hydraulic Jacks
2. The hydraulic pump is now switched to operating a hydraulic motor that has two sprocket wheels on its shaft, over which the hatch opening / closing chains pass.
3. With the hydraulic motor operational, the two hatch covers are pulled apart, like in the image below, the chains being involved in the pulling. By changing the direction of rotation of the hydraulic motor, the two covers are pulled inwards to close off the hatch.

Courtesy MacGregor
Hydraulic Motor with Double Sprocketed Wheel

An Aerial View of Hatches / Hatch Covers - Not a Chain Type
Courtesy MacGregor
Side-rolling hatch covers stow in a transverse direction. For open hatch bulk carriers (OHBCs), rolling covers of the piggy-back type are preferred if the deck allows little or no free space for stowing the covers when the hatches are open.
A traditional side-rolling cover consists of two panels per hatch, each panel rolling sideways on a pair of transverse ramps. This minimises obstacles to be considered by the shore crane or other loading/unloading device operator when loading and unloading. Our side-rolling hatch covers can have a variety of different drive systems. The two main options are rack-and-pinion or chain-drive.
The main variables in side-rolling hatch cover designs are the drive system, the lifting system and the cleating system, which usually depends on the specified lifting system – Roll-up-Roll (with auto cleats) or wheel lifters (with manual cleats).
Key features
For single and double panel solutions; depending on the available deck space, VLOCs come with a single panel.
Hydraulic or electric-drive lifting operations
Rack-and-pinion or chain-drive types
Manual or auto-cleating systems
Bearing pads for ease of installation and to minimise friction and wear
Reliable sealing solutions to match hull deformations
Adjustable fittings (to compensate for wear)
High-quality components for a long service life
Standardised well-proven design and spares
What were the problems?
Broken or damaged bearings, sometimes causing the wheel to slip off from its track and misaligning the whole hatch cover. (Image below)
Too little space adjacent to the wheel to insert a manual hydraulic jack and lift the hatch cover enough to remove the damaged wheel from the shaft.
The bearing of the wheel is frozen on the shaft and needs to be heated for removal of the inner race of the bearing. But because the vessel is carrying coal, hot work is not possible, as it could result in an explosion.
(Hence the chain blocks to pull the hatch covers open or closed, with the hot work relegated to the period when the vessel is on ballast).

Courtesy Brittania P&I Club
Broken Bearing, Wheel Gets Misaligned, falls off trackway,
Hatch cover is unable to move

Courtesy McGregor
Cracked Hatch Cover Wheel
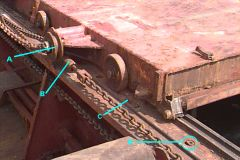
Turn Buckles (8) Are used to Adjust Length of Chains

Turn buckles, also wrongly called ‘bottle screws’.
One side thread is left handed, the other side right handed
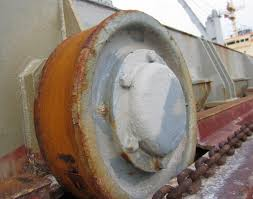
Asian Ocean Power Engineering
A Damaged Wheel
On my first voyage, we were on ballast, a convenient time for hot work. Good weather. The Mate and I spent an entire day opening and closing hatch covers and noting down what were the damages indicated.
It was then that I noted that the pulling chains were not aligned properly, some shorter, some longer, causing a sideways movement of the hatch cover which, in turn, put pressure on the bearings of the wheels, causing them to break, like glass. Nobody was sure how to adjust the lengths, which meant differing opinions and different procedures till now.
Subsequently, I found many bearings broken into small pieces. The chain links also were found to break.
Now, two jobs were being carried out simultaneously.
The first was to align the chains, so that the pull on the hatch cover was even at the forward end as well as the aft end. The first hatch cover alignment took time to achieve. The others went faster, as a more scientific approach was applied (euphemistically called ‘using your brain’), with precise measurements.
Some chains needed renewal as they were weak or the links elongated. One problem was the quality of the new chains, probably dubiously sourced. Requisitions went out immediately for the correct chains, giving tensile strengths, link sizes, material etc.
The second was to weld inverted brackets on to the sides of hatch covers, adjacent to all the wheels, so that 30 ton manual hydraulic jacks can easily be inserted under the bracket. On pumping, the hatch cover would be lifted about 8”, giving enough space to fit extractors to pull out the wheel. In some cases, hot work was needed. Being on a ballast passage, safety was ensured.
One serious error that was being committed on a regular basis by the Chief Engineers and the Engine Fitter was in the fitment of new bearings. They used to hammer the bearing into the wheel, it being a tight fit, using any and all means, as long as the bearing goes in. This was for the outer race of the bearing. When fitting it on to the shaft protruding out from the hatch cover, they used to hammer the inner race of the bearing till it went ‘home’. The damage to the bearing begins from here.
I taught them to keep the bearings in the Meat Room (-18 deg C) for 8 hours or so, whereon the bearing minutely reduces in diameter / circumference. The bearing, then, easily slides into the wheel and, on attaining normal temperature, the outer race expands to fit tightly into the wheel.
When fitting this wheel + bearing assembly back on to the stub shaft on the hatch cover, a different approach is taken. Using a small flame, the inner race of the bearing - which is inside the wheel - is heated for just a minute or so, just enough for the wheel + bearing assembly to just slide ‘home’ into place.
The assembly is then kept greased.
Within two months, we overhauled practically all the wheels and the failure rate came down to zero. The Office was very supportive in providing us quality spares frequently.
There were, then, no off hires due to hatch cover problems.
I put the Second Engineer on removing hydraulic jacks, overhauling them, renewing all seal and O rings and also rectifying hatch covers’ hydraulic line leaks. The Third Engineer would overhaul three or four everyday and keep them ready.
Being a UMS ship (Unmanned Machinery Spaces), although short staffed, I had the advantage of putting the full complement of Engineers and Engine Crew on several jobs at the same time.
Several hatch cover rubber packings were damaged or missing or hanging loose. Sections were renewed and glued on, after preparing the surfaces, Chief Officer continuing the same on other hatch covers.
Worn out bushes (almost all) of fast acting hatch cleats were renewed.
Top cleats' worn or cracked brackets were renewed,

The Chief Officer continued the momentum of the work being done and carried it over into deck and hatch maintenance and, finally, painting. Within 3 months, she started looking like a different ship from the one I boarded 3 months ago.

Present Day
Electric hatch covers - You Tube
Good to Have? The Jury is Out

Bearing Pads (under 12) and Locking Pins - Courtesy Wartsila
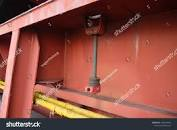
Quick Acting Cleats

Top Cleats - Britannia P&I Club
===== Blog 101 Follows =====
Comments